Tipus de fosa de ferro
Tipus de fosa de ferro
Aquest capítol tractarà els diferents tipus de fosa de ferro.
Fosa de ferro gris
La característica de la fosa grisa és la microestructura gràfica, que és capaç de provocar fractures al material i tenir un aspecte gris. Aquest és el tipus de ferro colat més utilitzat i també el material de fosa utilitzat habitualment en funció del pes. La majoria de les ferros colades grises tenen una descomposició química del 2,5% al 4% de carboni, de l'1% al 3% de silicona i la resta és una composició de ferro.
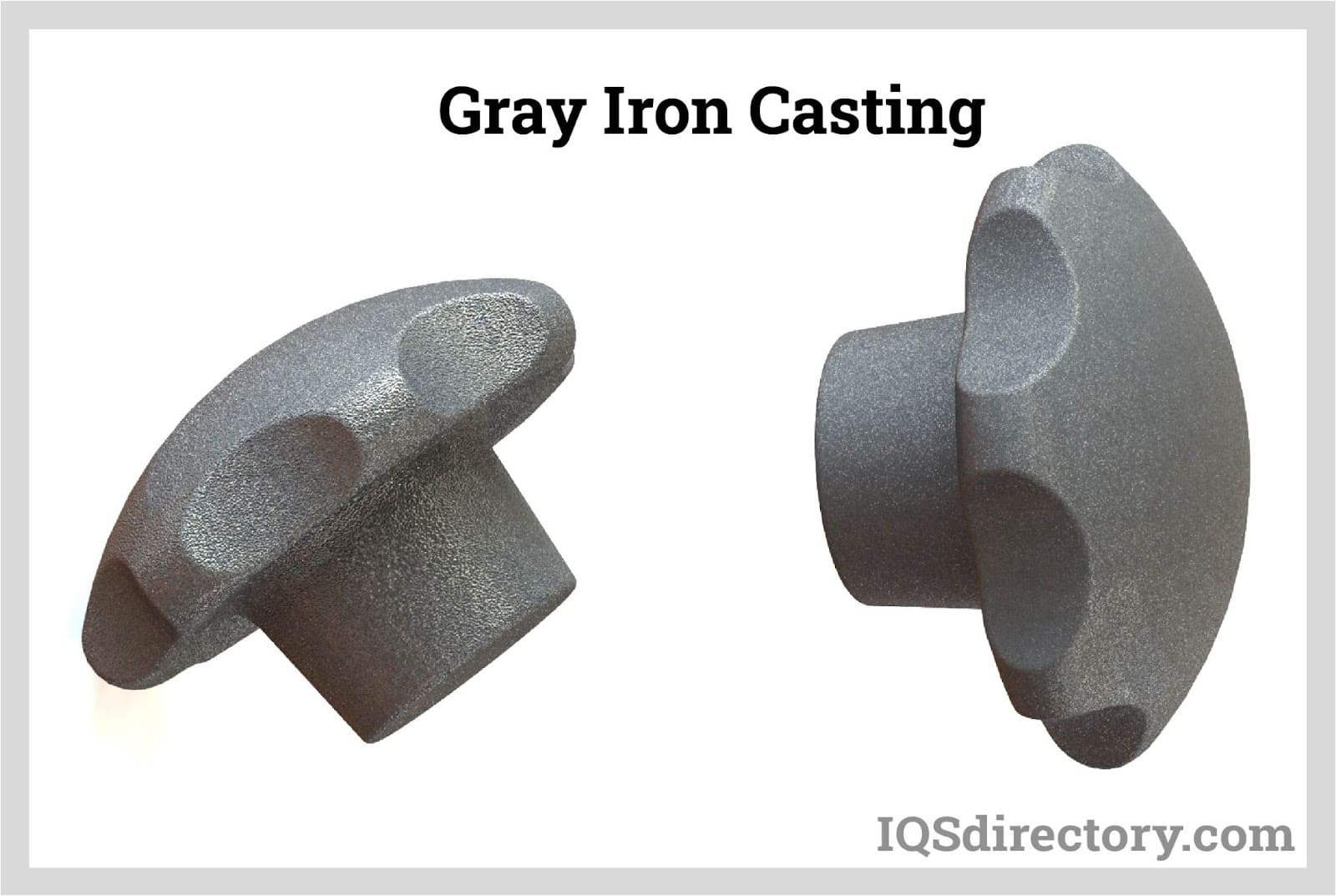
Aquest tipus de ferro colat té menys resistència a la tracció i menys resistència als cops en comparació amb l'acer. La seva resistència a la compressió és comparable a l'acer de carboni baix i mitjà.
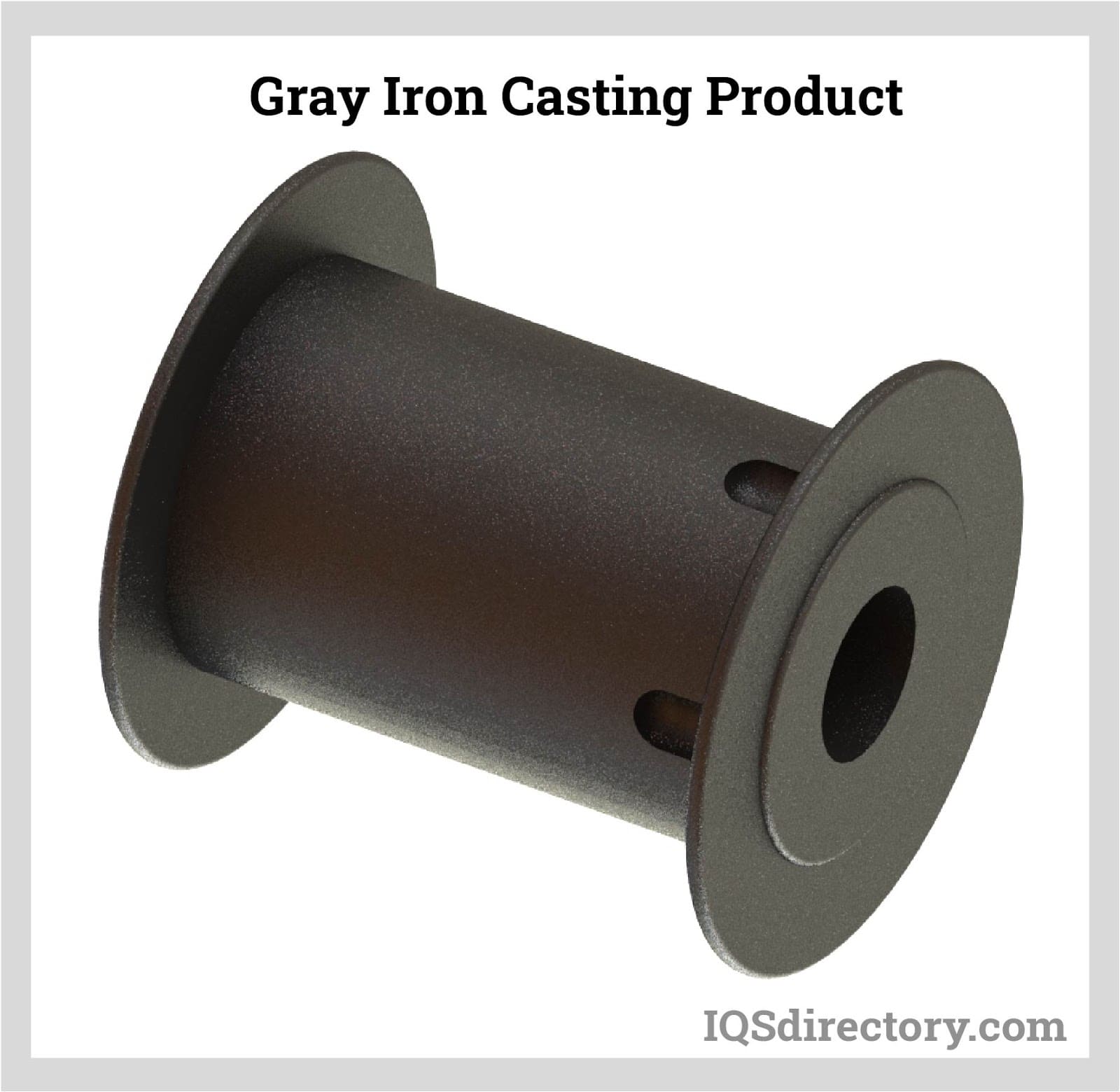
Totes aquestes propietats mecàniques estan controlades per la forma de les escates de grafit i la mida de les escates de grafit, que estan presents a la microestructura de la fosa grisa.
Fundició de ferro blanc
Aquest tipus de ferro té superfícies fracturades que són blanques a causa de la presència d'un precipitat de carbur de ferro anomenat cementita. El carboni que conté la fosa blanca precipita fora de la fosa com a cementita de fase estable i no com a grafit. Això s'aconsegueix amb un contingut de silici més baix com a agent de grafitització i una velocitat de refrigeració subministrada més ràpida. Després d'aquesta precipitació, la cementita es forma com a grans partícules.
Durant la precipitació del carbur de ferro, el precipitat extreu carboni de la fosa original, movent així la mescla cap a una més propera a l'eutèctic. La fase restant és baixar el ferro a austenita de carboni, que es transforma en martensita un cop refredat.
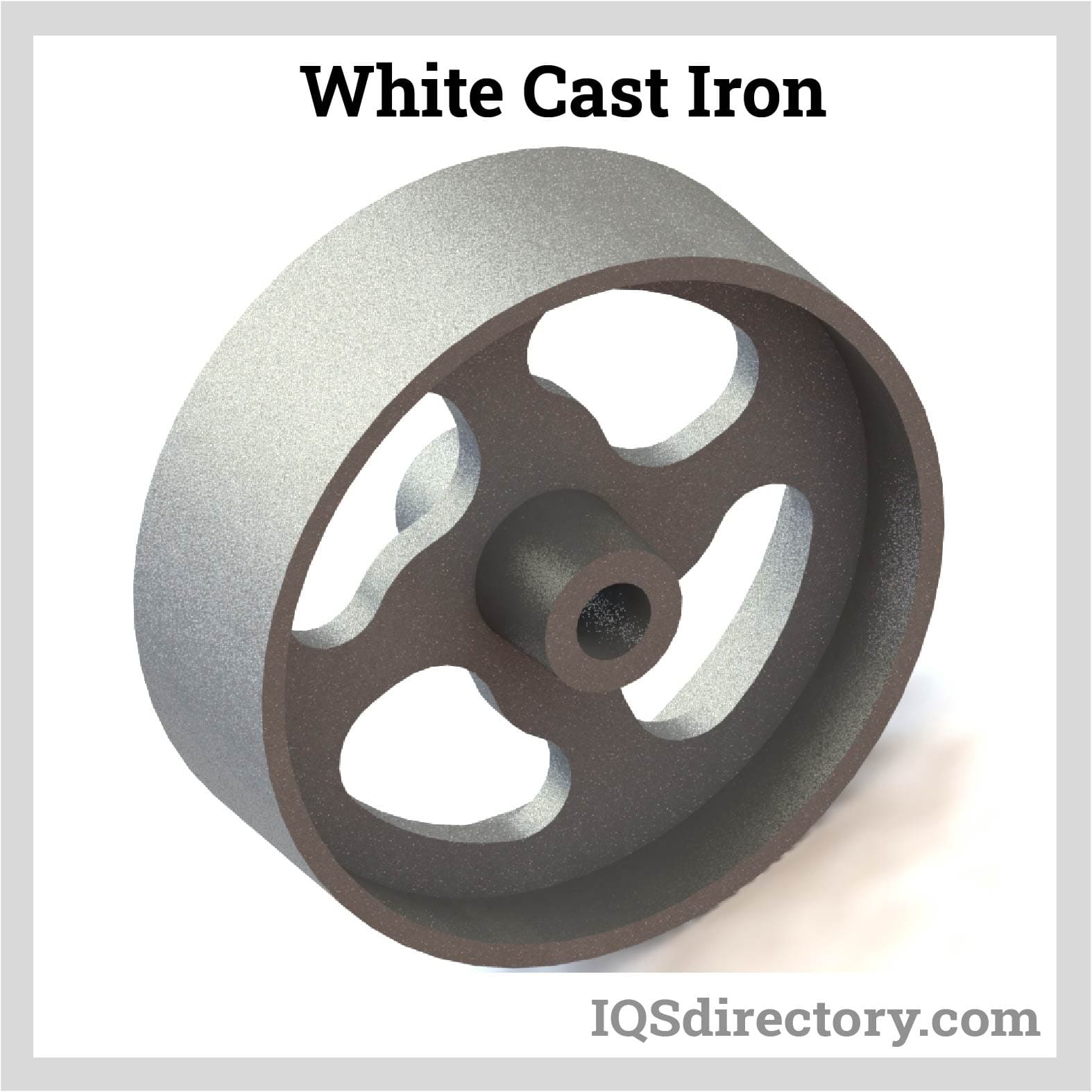
Aquests carburs eutèctics continguts són massa grans per oferir el benefici de l'enduriment per precipitació. En alguns acers hi podria haver precipitats de cementita molt més petits que podrien portar la deformació del plàstic impedint el moviment de les dislocacions a través de la matriu de ferrita de ferro pur. Tenen un avantatge, ja que augmenten la duresa a granel de la fosa simplement per la seva pròpia duresa i fracció de volum. Això fa que la duresa a granel es pugui aproximar mitjançant una regla de mescles.
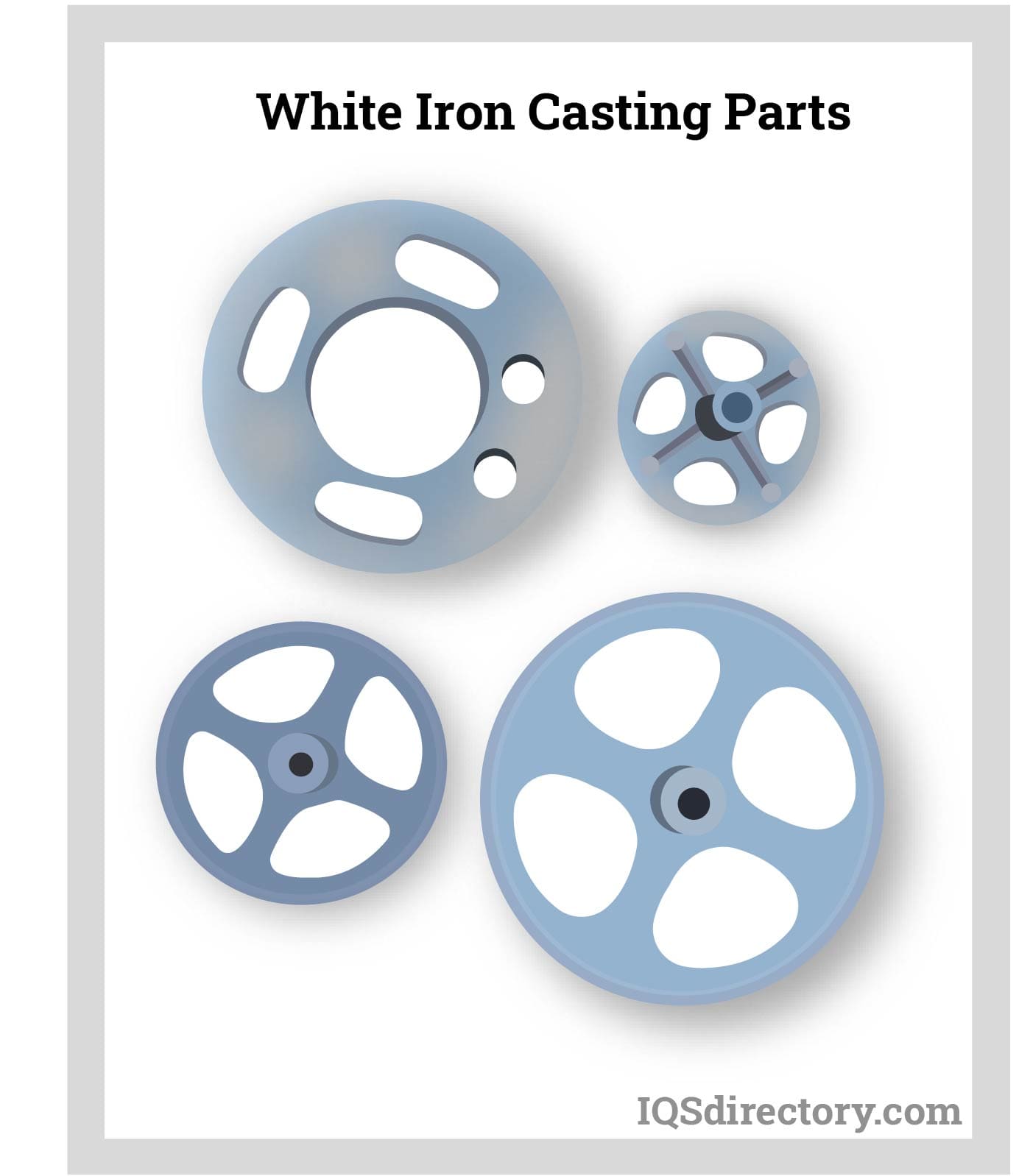
Aquesta duresa s'ofereix a costa de la duresa en qualsevol cas. El ferro colat blanc es pot classificar generalment com a ciment, ja que el carbur constitueix una fracció més gran del material. El ferro blanc és massa fràgil per utilitzar-se en components estructurals, però a causa de la seva bona duresa, resistència a l'abrasió i baix cost, es pot utilitzar com a superfície de desgast de les bombes de purins.
És difícil refredar peces de fosa gruixudes a un ritme més ràpid que és suficient per solidificar la fosa com a ferro colat blanc, però es pot utilitzar un refredament ràpid per solidificar un infern de ferro colat blanc i després d'això quedarà una resta. refredar a un ritme més lent formant així un nucli de ferro colat gris. Aquesta fosa resultant s'anomena fosa refrigerada i conté els avantatges de tenir una superfície dura però amb un interior més resistent.
Els aliatges de ferro blanc d'alt crom tenien la capacitat de permetre la fosa massiva d'unes 10 tones d'impulsor de sorra. Això es deu al fet que el crom redueix la velocitat de refrigeració necessària per produir carburs a través dels majors gruixos de material. Els elements de crom també produeixen carburs amb una excel·lent resistència a l'abrasió.
Fundició de ferro mal·leable
La fosa mal·leable comença com una fosa de ferro blanc, després es tracta tèrmicament a temperatures d'uns 950 °C durant dos o un sol dia, i després es refreda durant el mateix període de temps.
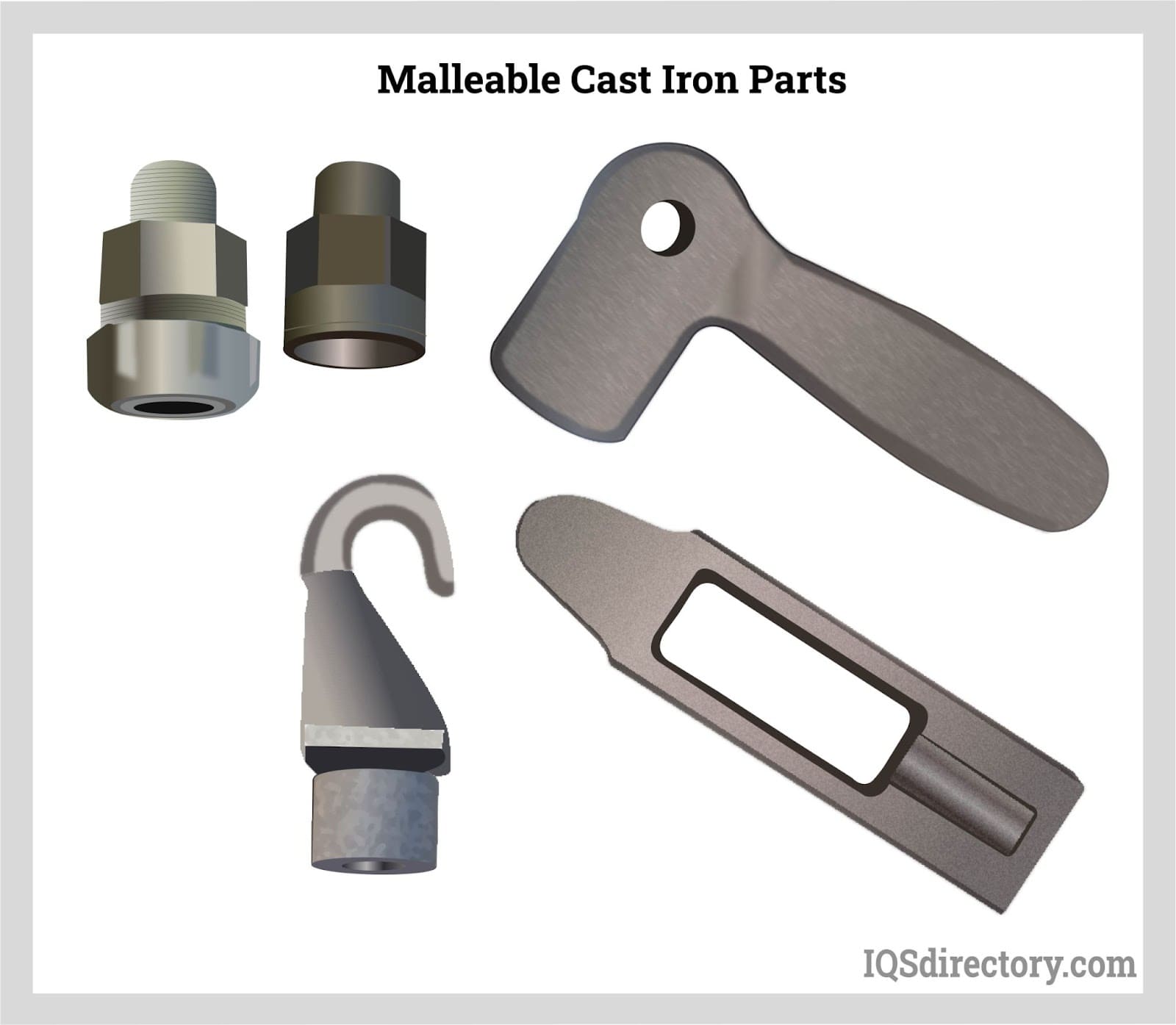
El carboni del carbur de ferro es transforma després en grafit i ferrita més carboni a causa d'aquest procés d'escalfament i refredament. Aquest és un procés baix, però permet que la tensió superficial transformi el grafit en partícules esferoïdals en lloc de flocs.
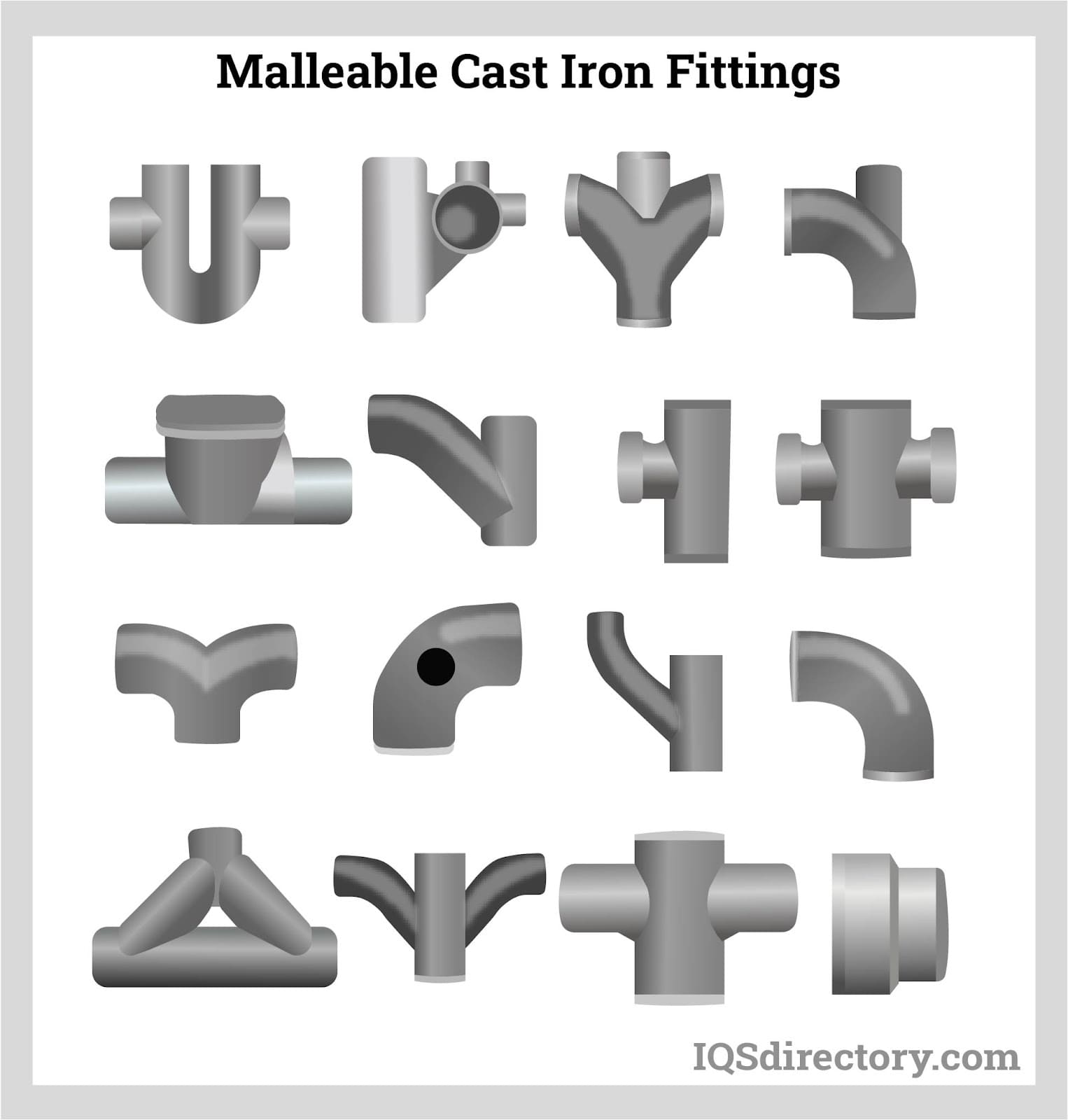
Els esferoides són relativament curts i més allunyats els uns dels altres a causa de la seva baixa relació d'aspecte. També contenen una secció transversal inferior, esquerda de propagació i un fotó. A diferència dels flocs, contenen límits contundents que participen en l'alleujament dels problemes de concentració d'estrès que es troben a la fosa grisa. Amb tot, les propietats incloses en la fosa mal·leable s'assemblen més a les de l'acer de naturalesa suau.
Fundició de ferro dúctil
De vegades denominat ferro colat nodular, aquest ferro colat té el seu grafit en forma de nòduls molt petits, amb el grafit en forma de capes que són concèntriques i formen així els nòduls. Per això, les propietats deferro colat dúctilsón els d'un acer esponjós que no té efectes de concentració de tensions produïts per les escates del grafit.
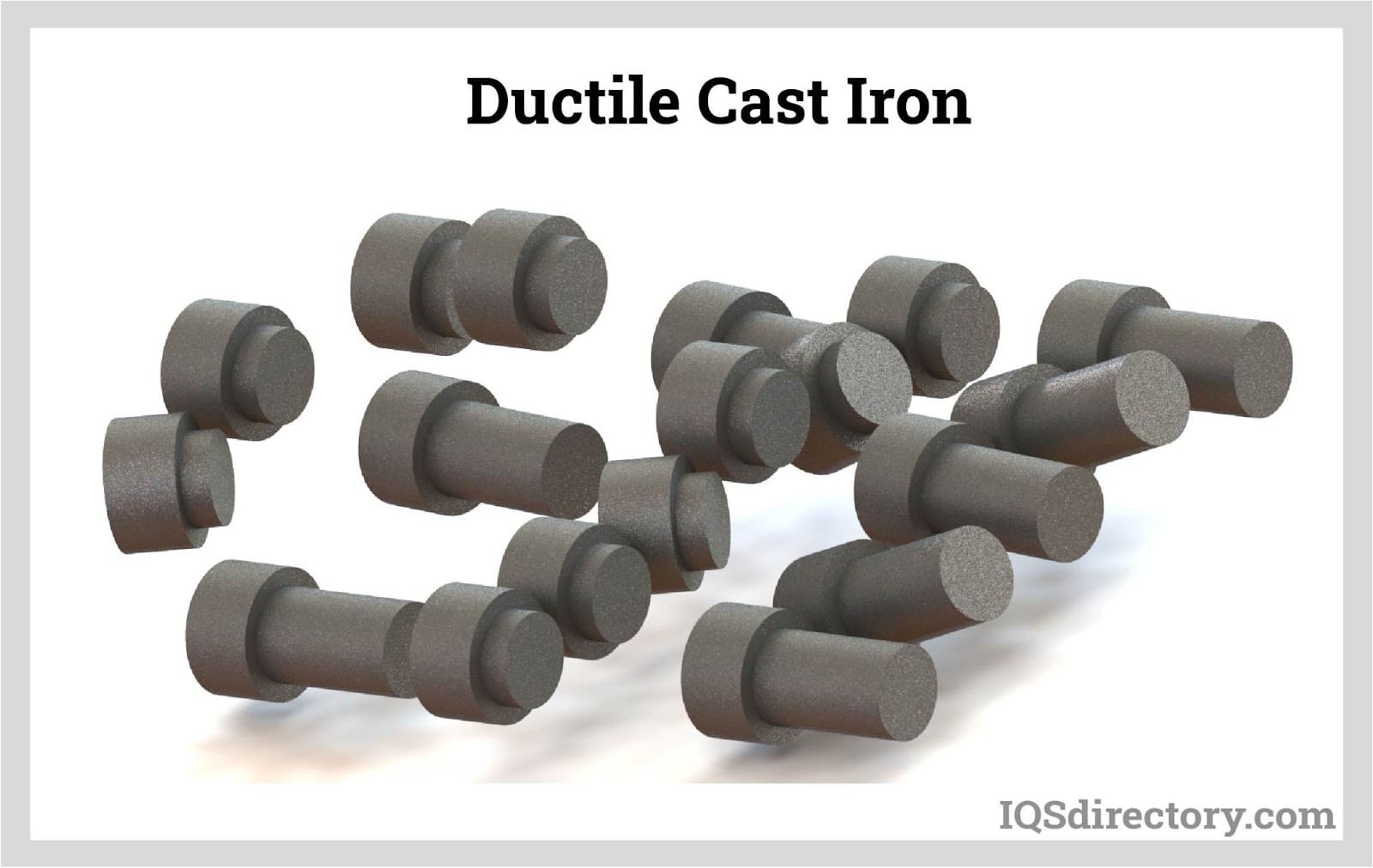
La quantitat de concentració de carboni continguda és d'entre el 3 i el 4 per cent, i la de silici és d'entre l'1,8 i el 2,8 per cent. Petites quantitats del 0,02% al 0,1% de magnesi i només del 0,02% al 0,04% de ceri quan s'afegeixen a aquests aliatges frenen la velocitat a la qual creix la precipitació de grafit mitjançant la unió a les vores dels carrils de grafit.
El carboni pot tenir la possibilitat de separar-se com a partícules esferoïdals a mesura que el material es solidifica, a causa del control acurat d'altres elements i el moment adequat durant el procés. Les partícules resultants són similars al ferro colat mal·leable, però les peces es poden colar amb seccions més grans.
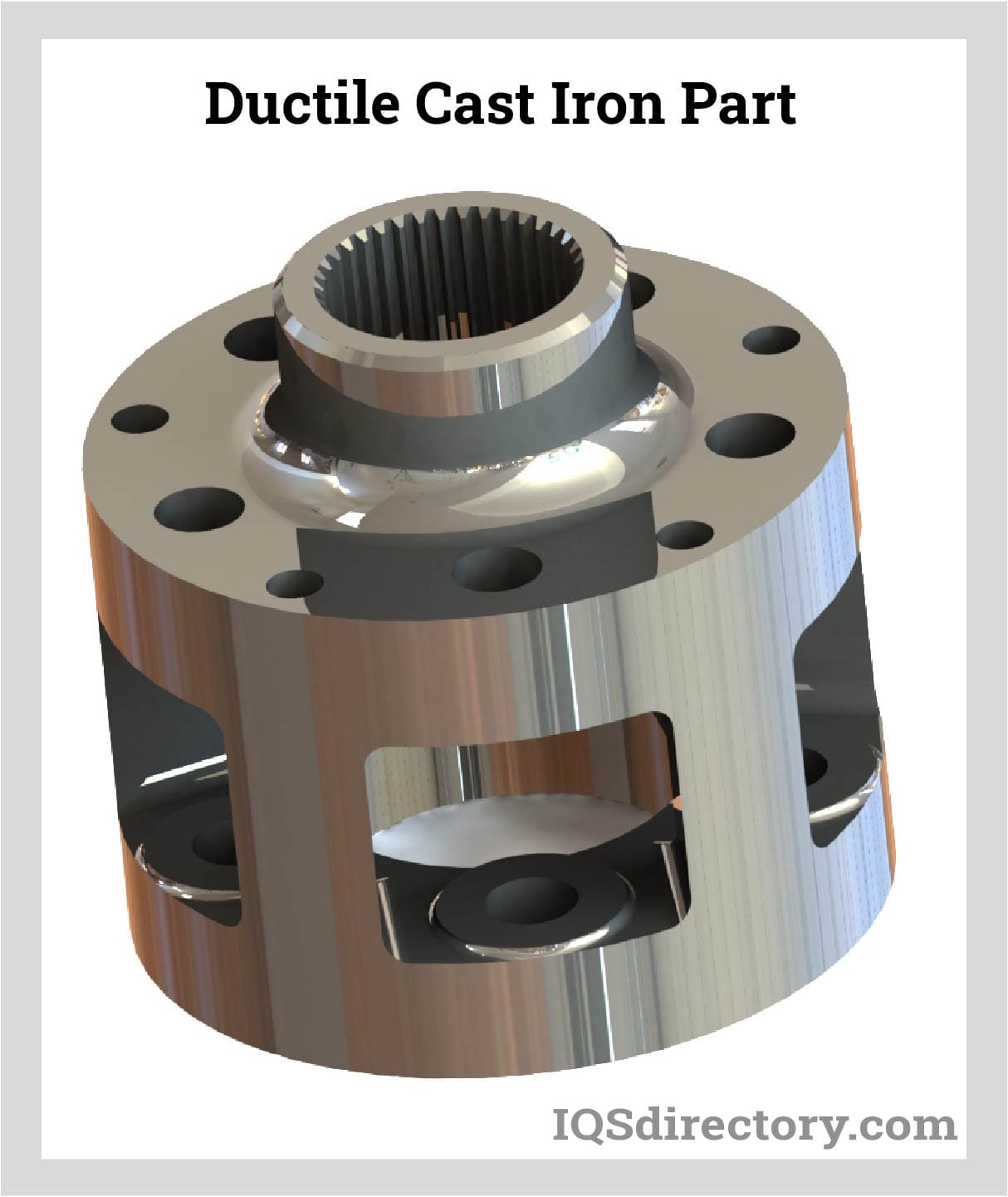
Elements d'aliatge
Les propietats de la fosa es modifiquen i s'afegeixen en diversos elements d'aliatge o aliatges a la fosa. En línia amb el carboni es troba l'element silici perquè té la capacitat de forçar el carboni a sortir de la solució. Un percentatge menor de silici no pot aconseguir-ho completament, ja que permet que el carboni romangui a la solució, formant així carbur de ferro i produint també ferro colat blanc.
Un percentatge o concentració més gran de silici és capaç de forçar el carboni fora de la solució i després formar grafit i també produir ferro colat gris. Altres agents d'aliatge no assenyalats inclouen manganès, crom, titani i després vanadi. Aquests contraresten el silici, també afavoreixen la retenció de carboni i per tant també la formació de carburs. El níquel i l'element coure tenen un avantatge ja que augmenten la resistència i la mecanització, però no poden canviar la quantitat de carboni format.
El carboni que es troba en forma de grafit dóna com a resultat un ferro més tou, reduint així l'efecte de la contracció, disminuint la resistència i disminuint la densitat continguda. El sofre és majoritàriament un contaminant quan està contingut, i forma sulfur de ferro que impedeix la formació de grafit i també augmenta la duresa.
L'inconvenient que imposa el sofre és que fa que la fosa fosa viscosa, la qual cosa provoca defectes. Per atendre i eliminar els efectes del sofre, s'afegeix manganès a la solució. Això es fa perquè quan els dos es combinen formen sulfur de manganès en lloc de sulfur de ferro. El sulfur de manganès resultant és més lleuger que la fosa i tendeix a surar fora de la fosa i entrar a l'escòria.
La quantitat aproximada de manganès necessària per cancel·lar els efectes del sofre és d'1,7 unitats de contingut de sofre i un 0,3 per cent addicional afegit a la part superior. L'addició de més d'aquesta quantitat de manganès dóna lloc a la formació de carbur de manganès i això augmenta la duresa i el refredament, excepte en el ferro gris, on fins a un 1 per cent de manganès pot augmentar la força i la densitat continguda. El níquel és un dels elements d'aliatge més generals perquè té una tendència a refinar la perlita i l'estructura del grafit, millorant així la tenacitat i uniformitzant la diferència de duresa entre els gruixos de la secció.
S'afegeix crom en petites quantitats per reduir el grafit lliure i produir un fred. Això es deu al fet que el crom és un potent estabilitzador de carbur i, en alguns casos, pot funcionar juntament amb el níquel. També per al crom, es pot afegir una petita quantitat substitutiva d'estany. El coure s'afegeix a la cullera o al forn de l'ordre del 0,5% al 2,5% per aconseguir un refredament reduït, refinar el grafit i augmentar la fluïdesa. També es pot afegir molibdè de l'ordre del 0,3% a l'1% per augmentar també el fred, refinar el grafit i refinar l'estructura de la perlita.
Normalment s'afegeix treballant en línia amb níquel, coure i crom per produir ferros d'alta resistència. L'element titani s'afegeix per funcionar com a desgasificador i desoxidant, i augmenta la fluïdesa. S'afegeixen proporcions del 0,15% al 0,5% de l'element vanadi al ferro colat i ajuden a estabilitzar la cementita, per augmentar la duresa i resistir el desgast i els efectes de la calor.
El zirconi ajuda a formar grafit i s'afegeix en proporcions d'entre 0,1 i 0,3 per cent. Aquest element també ajuda a desoxidar i augmentar la fluïdesa. En les foses de ferro mal·leable, per augmentar la quantitat de silici que es pot afegir, s'aboca bismut en una escala del 0,002% al 0,01%. En el ferro blanc, s'afegeix l'element bor, que ajuda a la producció de ferro que és mal·leable i redueix l'efecte gruixut de l'element bismut.