Tipos de piezas de fundición de hierro
Tipos de piezas de fundición de hierro
En este capítulo se analizarán los distintos tipos de piezas de fundición de hierro.
Fundición de hierro gris
La fundición gris se caracteriza por su microestructura gráfica, que puede causar fracturas y presentar un aspecto gris. Este tipo de fundición es el más utilizado y también el material de fundición más común en términos de peso. La mayoría de las fundiciones grises presentan una descomposición química de entre el 2,5 % y el 4 % de carbono, entre el 1 % y el 3 % de silicio y el resto de hierro.
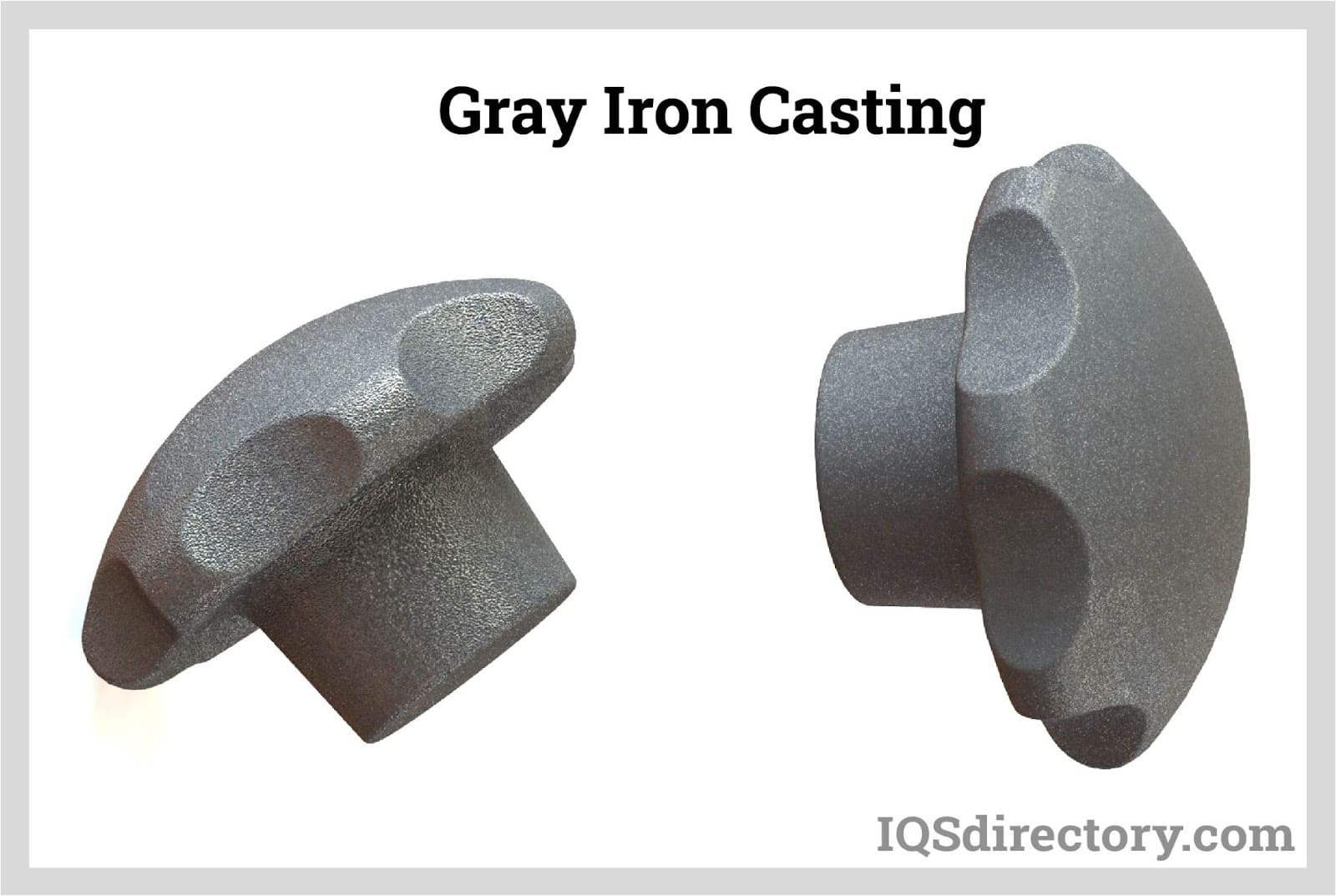
Este tipo de hierro fundido presenta menor resistencia a la tracción y a los impactos que el acero. Su resistencia a la compresión es comparable a la del acero de bajo y medio carbono.
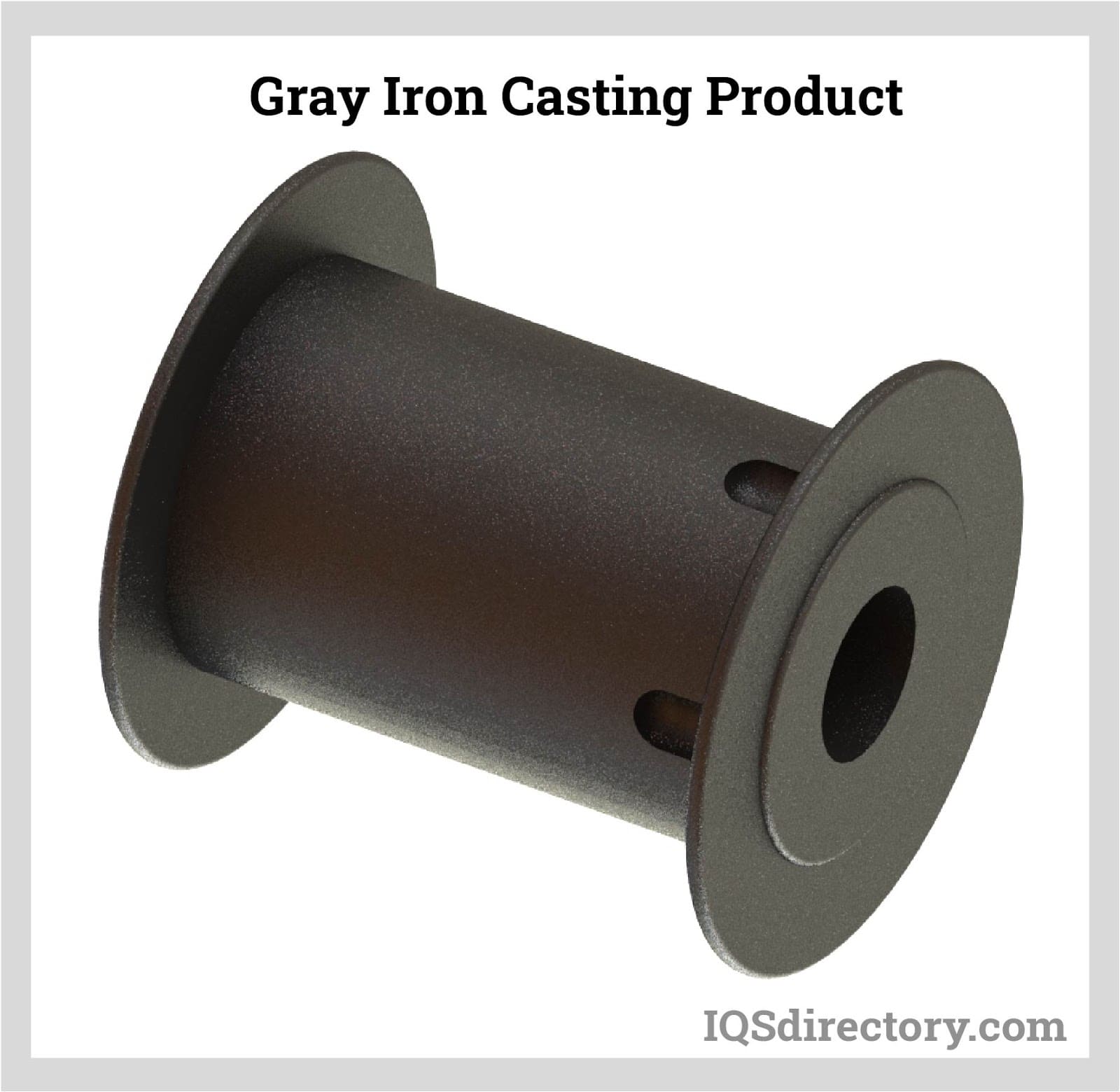
Todas estas propiedades mecánicas están controladas por la forma de las escamas de grafito y el tamaño de las escamas de grafito, que están presentes en la microestructura de la fundición gris.
Fundición de hierro blanco
Este tipo de hierro presenta superficies fracturadas de color blanco debido a la presencia de un precipitado de carburo de hierro llamado cementita. El carbono presente en el hierro fundido blanco precipita de la masa fundida como cementita, una fase estable, en lugar de grafito. Esto se logra con un menor contenido de silicio como agente grafitizante y una mayor velocidad de enfriamiento. Tras esta precipitación, la cementita se forma en partículas grandes.
Durante la precipitación del carburo de hierro, el precipitado extrae carbono de la masa fundida original, lo que acerca la mezcla a una fase más eutéctica. La fase restante reduce el hierro a austenita carbonada, que se transforma en martensita al enfriarse.
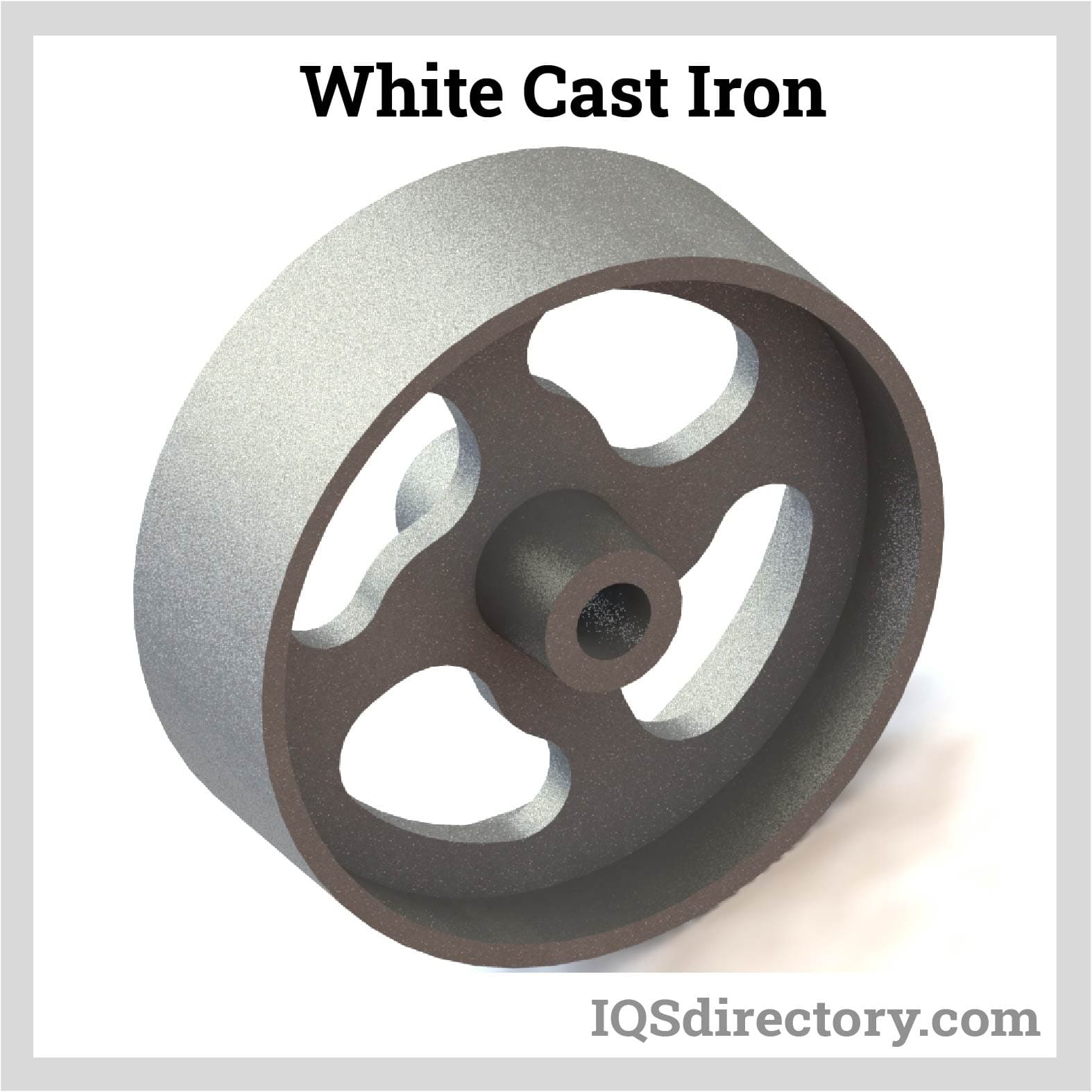
Estos carburos eutécticos contenidos son demasiado grandes para proporcionar el beneficio del endurecimiento por precipitación. En algunos aceros, puede haber precipitados de cementita mucho más pequeños que podrían contribuir a la deformación plástica al impedir el movimiento de dislocaciones a través de la matriz de ferrita de hierro puro. Presentan la ventaja de aumentar la dureza aparente del hierro fundido simplemente por su propia dureza y fracción volumétrica. Esto permite aproximar la dureza aparente mediante una regla de mezclas.
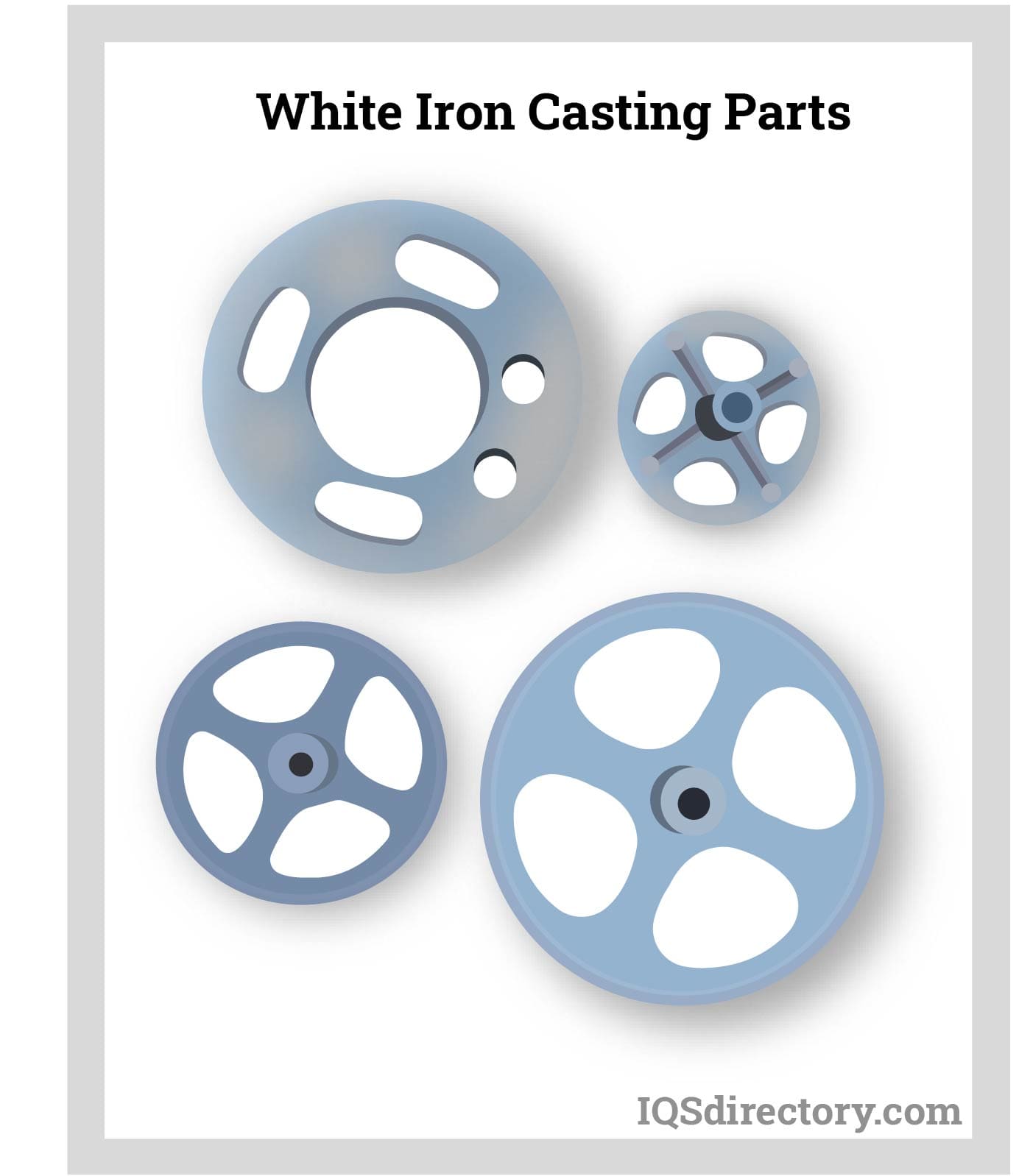
Esta dureza se ofrece en cualquier caso a expensas de la tenacidad. El hierro fundido blanco puede clasificarse generalmente como cemento, ya que el carburo constituye una fracción mayor del material. El hierro blanco es demasiado frágil para usarse en componentes estructurales, pero debido a su buena dureza, resistencia a la abrasión y bajo costo, puede usarse como superficie de desgaste en bombas de lodos.
Es difícil enfriar piezas fundidas gruesas a una velocidad suficiente para solidificar la masa fundida como hierro fundido blanco. Sin embargo, se puede usar un enfriamiento rápido para solidificar una gran cantidad de hierro fundido blanco. Posteriormente, el resto se enfriará a un ritmo más lento, formando así un núcleo de hierro fundido gris. Esta pieza resultante se denomina fundición enfriada y ofrece la ventaja de tener una superficie dura, pero un interior más resistente.
Las aleaciones de hierro blanco con alto contenido de cromo permitieron la fundición en arena de un impulsor de aproximadamente 10 toneladas. Esto se debe a que el cromo reduce la velocidad de enfriamiento necesaria para producir carburos a través de mayores espesores de material. Los elementos de cromo también producen carburos con excelente resistencia a la abrasión.
Fundición de hierro maleable
El hierro fundido maleable comienza como una pieza de hierro blanco, luego se trata térmicamente a temperaturas de aproximadamente 950 °C durante dos o un día, y luego se enfría durante el mismo período de tiempo.
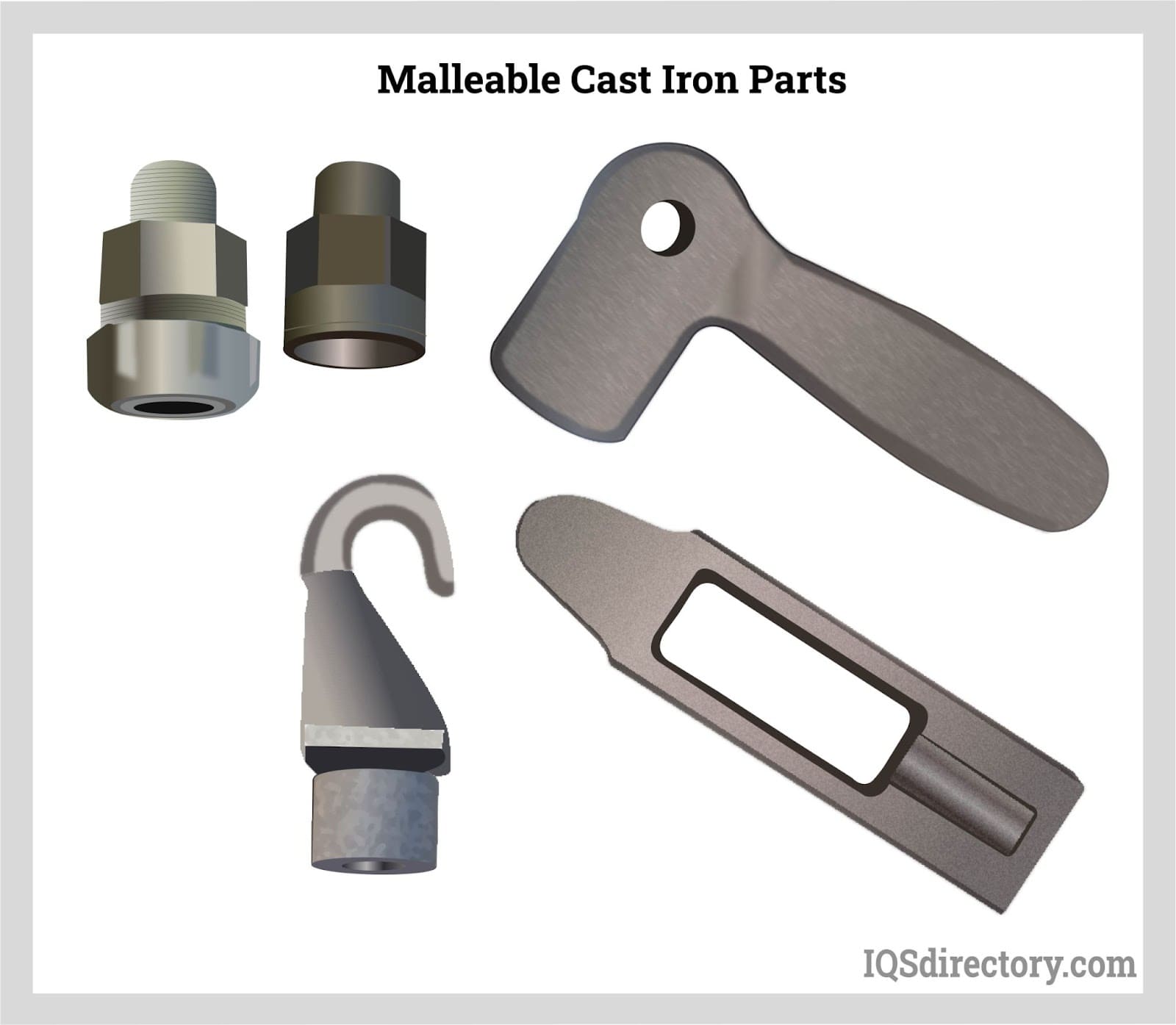
El carbono del carburo de hierro se transforma en grafito y ferrita, además de carbono, gracias a este proceso de calentamiento y enfriamiento. Este proceso es lento, pero permite que la tensión superficial transforme el grafito en partículas esferoidales en lugar de escamas.
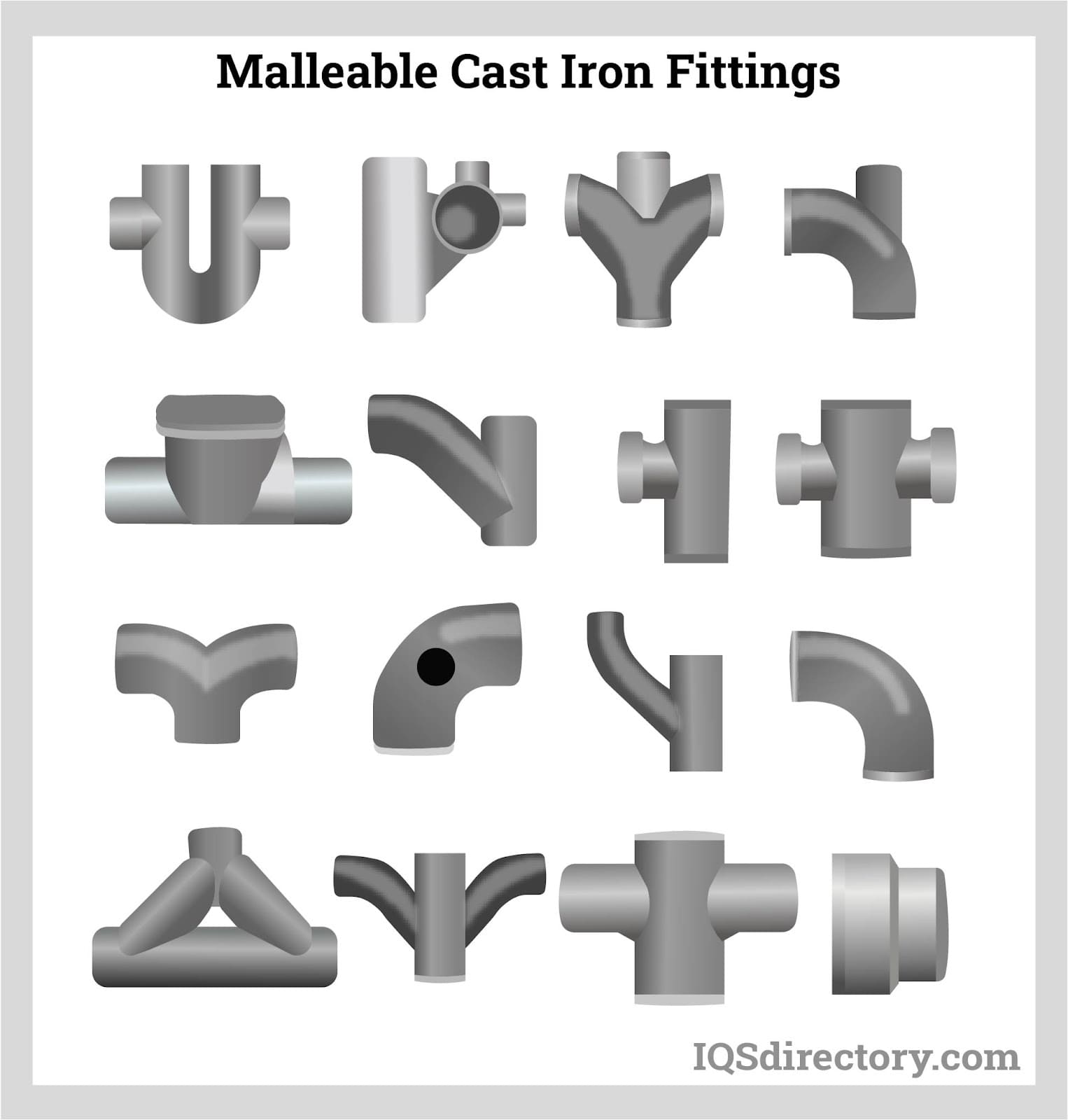
Los esferoides son relativamente cortos y están más separados entre sí debido a su baja relación de aspecto. Además, presentan una sección transversal más baja, grietas que se propagan y un fotón. A diferencia de las escamas, presentan límites romos que contribuyen a mitigar los problemas de concentración de tensiones presentes en la fundición gris. En resumen, las propiedades de la fundición maleable se asemejan más a las del acero, que es de naturaleza dulce.
Fundición de hierro dúctil
A veces denominada fundición nodular, esta fundición presenta su grafito en forma de nódulos diminutos, que forman capas concéntricas. Por ello, las propiedades dehierro fundido dúctilson las de un acero esponjoso que no tiene efectos de concentración de tensiones producidos por las escamas del grafito.
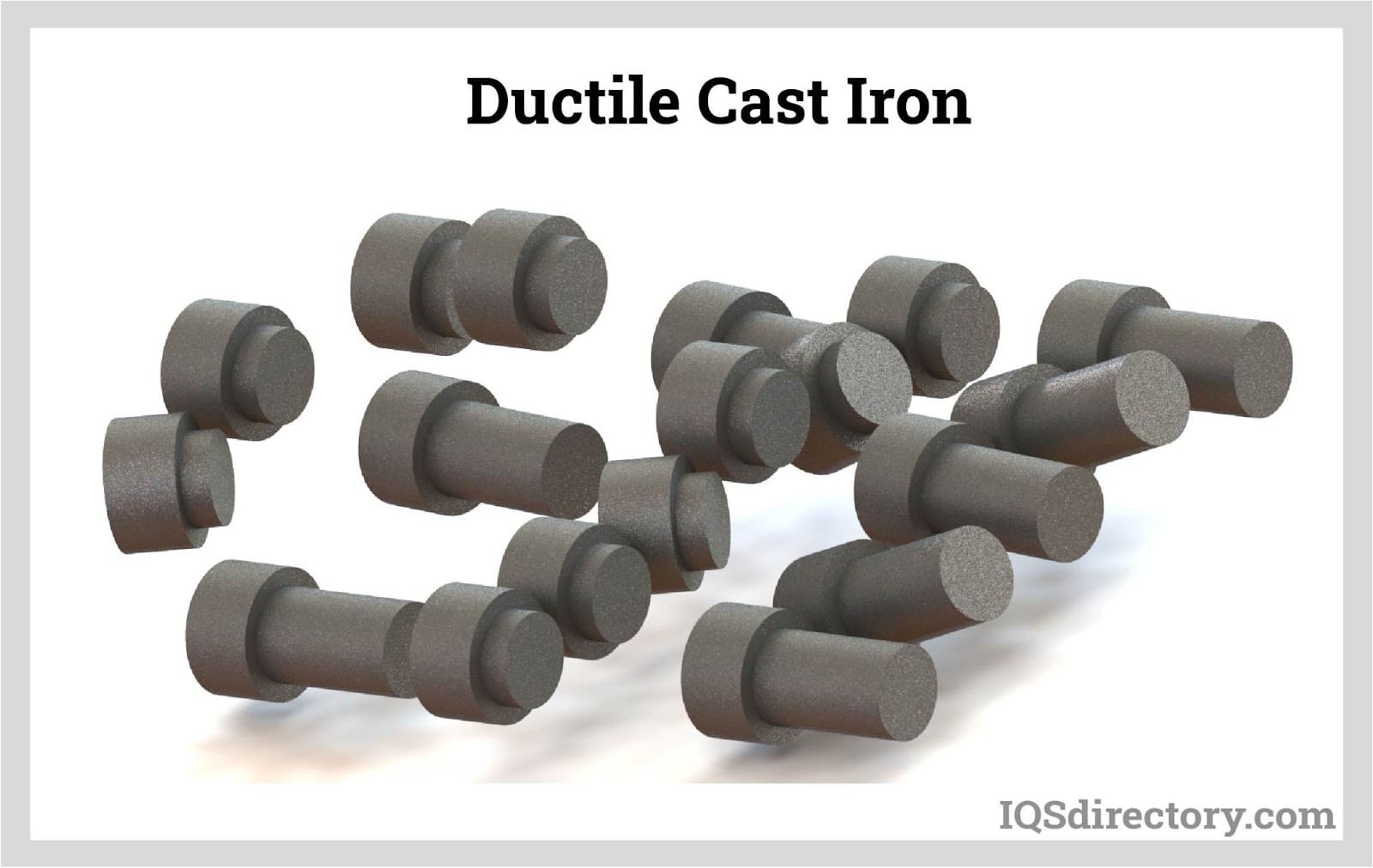
La concentración de carbono contenida oscila entre el 3 % y el 4 %, y la de silicio, entre el 1,8 % y el 2,8 %. La adición de pequeñas cantidades de magnesio (entre el 0,02 % y el 0,1 %) y de cerio (solo entre el 0,02 % y el 0,04 %) a estas aleaciones ralentiza la velocidad de precipitación del grafito al unirse a los bordes de las bandas.
El carbono puede separarse en partículas esferoidales a medida que el material se solidifica, gracias al control cuidadoso de otros elementos y a la sincronización adecuada del proceso. Las partículas resultantes son similares a las del hierro fundido maleable, pero las piezas pueden fundirse con secciones más grandes.
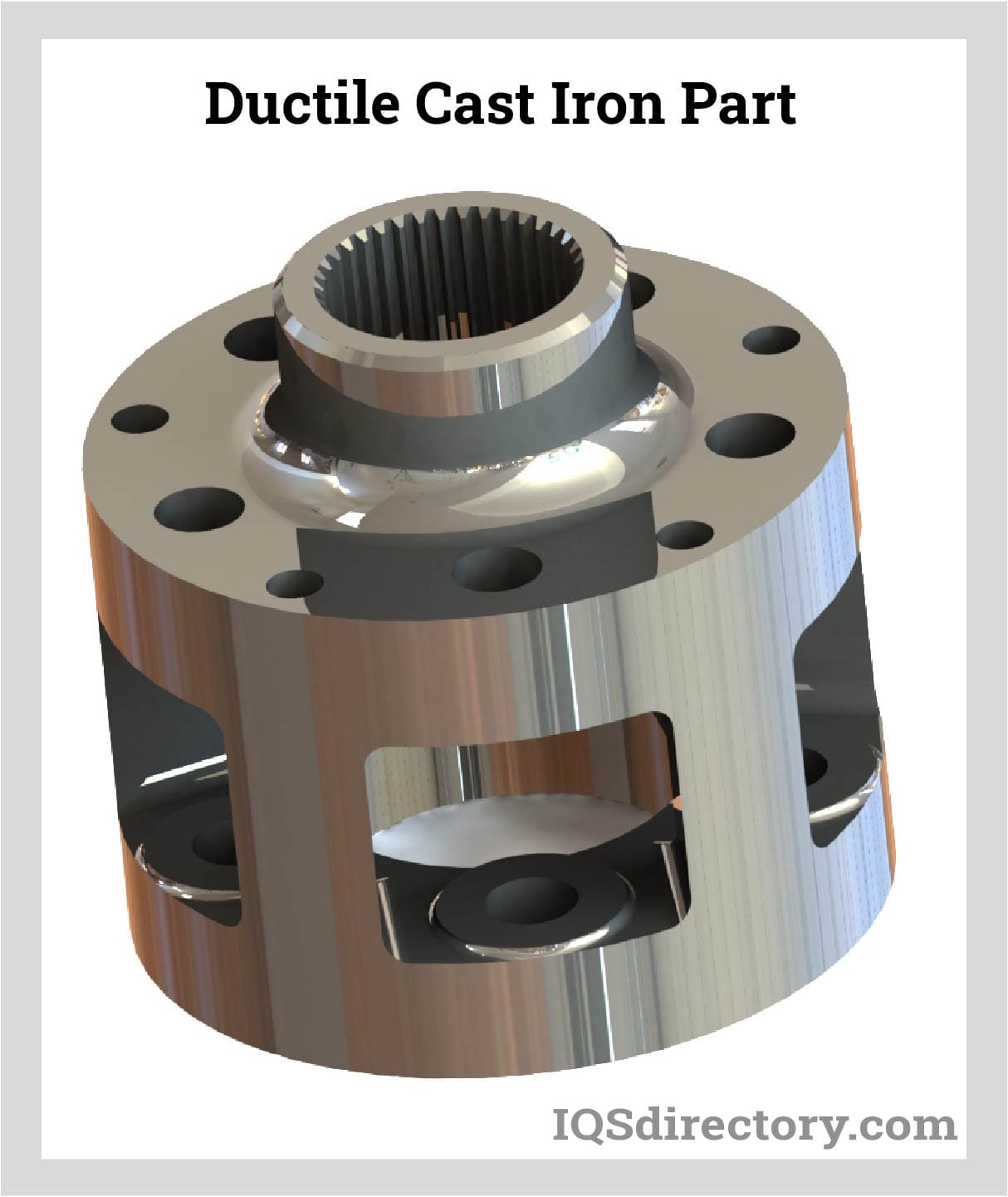
Elementos de aleación
Las propiedades del hierro fundido se modifican y se añaden a él mediante diversos elementos o aleantes. El silicio, en consonancia con el carbono, tiene la capacidad de expulsar el carbono de la solución. Un porcentaje menor de silicio no puede lograrlo plenamente, ya que permite que el carbono permanezca en la solución, formando así carburo de hierro y, además, produciendo hierro fundido blanco.
Un mayor porcentaje o concentración de silicio puede expulsar el carbono de la solución y, por lo tanto, formar grafito, además de producir fundición gris. Otros agentes de aleación no mencionados incluyen manganeso, cromo, titanio y, finalmente, vanadio. Estos contrarrestan el silicio y promueven la retención de carbono y, por lo tanto, la formación de carburos. El níquel y el cobre tienen la ventaja de aumentar la resistencia y la maquinabilidad, pero no pueden modificar la cantidad de carbono formado.
El carbono en forma de grafito produce un hierro más blando, lo que reduce el efecto de la contracción, disminuye la resistencia y disminuye la densidad contenida. El azufre, cuando está contenido, es principalmente un contaminante y forma sulfuro de hierro, lo que impide la formación de grafito y aumenta la dureza.
La desventaja del azufre es que viscosifica el hierro fundido, lo cual causa defectos. Para contrarrestar y eliminar los efectos del azufre, se añade manganeso a la solución. Esto se debe a que, al combinarse, se forma sulfuro de manganeso en lugar de sulfuro de hierro. El sulfuro de manganeso resultante es más ligero que la masa fundida y tiende a flotar y a integrarse en la escoria.
La cantidad aproximada de manganeso necesaria para contrarrestar los efectos del azufre es de 1,7 unidades de azufre, más un 0,3 % adicional. Añadir una cantidad superior de manganeso produce carburo de manganeso, lo que aumenta la dureza y el enfriamiento, excepto en la fundición gris, donde hasta un 1 % de manganeso puede aumentar la resistencia y la densidad. El níquel es uno de los elementos de aleación más comunes, ya que tiende a refinar la perlita y la estructura del grafito, mejorando así la tenacidad y equilibrando la diferencia de dureza entre los espesores de las secciones.
Se añade cromo en pequeñas cantidades para reducir el grafito libre y producir un enfriamiento. Esto se debe a que el cromo es un potente estabilizador de carburo y, en algunos casos, puede funcionar junto con el níquel. Para el cromo, también se puede añadir una pequeña cantidad de estaño como sustituto. Se añade cobre en la cuchara o el horno en una proporción del 0,5 % al 2,5 % para reducir el enfriamiento, refinar el grafito y aumentar la fluidez. También se puede añadir molibdeno en una proporción del 0,3 % al 1 % para aumentar el enfriamiento, refinar el grafito y la estructura de la perlita.
Se suele añadir trabajando en conjunto con níquel, cobre y cromo para producir hierros de alta resistencia. El titanio se añade para actuar como desgasificador y desoxidante, y para aumentar la fluidez. Se añaden proporciones de vanadio del 0,15 % al 0,5 % al hierro fundido para ayudar a estabilizar la cementita, aumentar la dureza y resistir los efectos del desgaste y el calor.
El circonio contribuye a la formación de grafito y se añade en proporciones de entre el 0,1 % y el 0,3 %. Este elemento también contribuye a la desoxidación y a aumentar la fluidez. En las fundiciones de hierro maleable, para aumentar la cantidad de silicio que se puede añadir, se vierte bismuto en una proporción del 0,002 % al 0,01 %. En el hierro blanco, se añade boro, lo que facilita la producción de hierro maleable y reduce el efecto de engrosamiento del bismuto.