Tipos de fundición de ferro
Tipos de fundición de ferro
Neste capítulo trataranse os distintos tipos de fundición de ferro.
Fundición de ferro gris
A característica da fundición gris é a microestrutura gráfica, que é capaz de provocar fracturas no material e ter un aspecto gris. Este é o tipo de fundición máis utilizado e tamén o material de fundición de uso habitual en función do peso. A maioría das fundicións grises teñen unha descomposición química de 2,5 por cento a 4 por cento de carbono, 1 por cento a 3 por cento de silicona e o resto é unha composición de ferro.
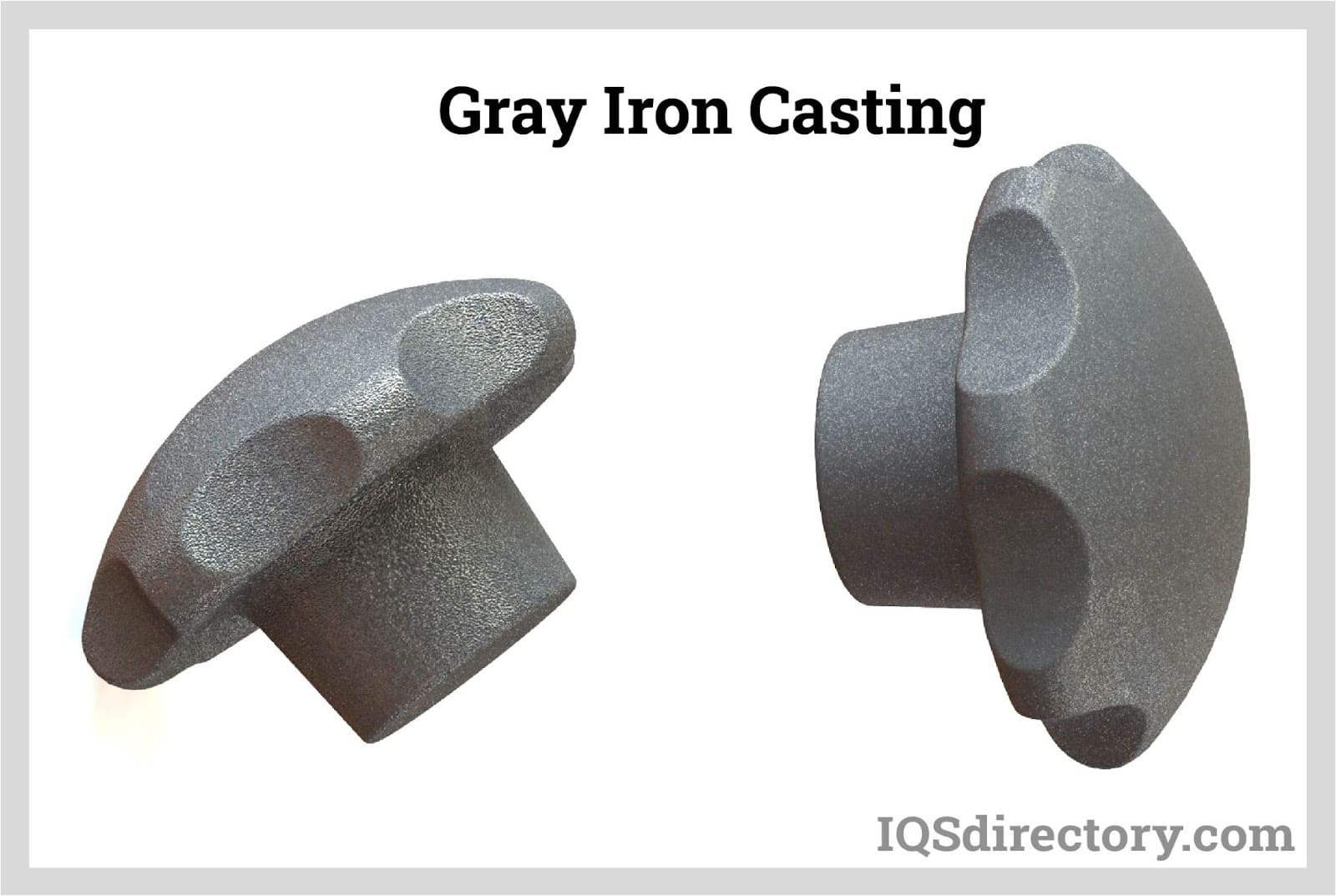
Este tipo de fundición ten menos resistencia á tracción e menor resistencia ao choque en comparación co aceiro. A súa resistencia á compresión é comparable á do aceiro de baixo e medio carbono.
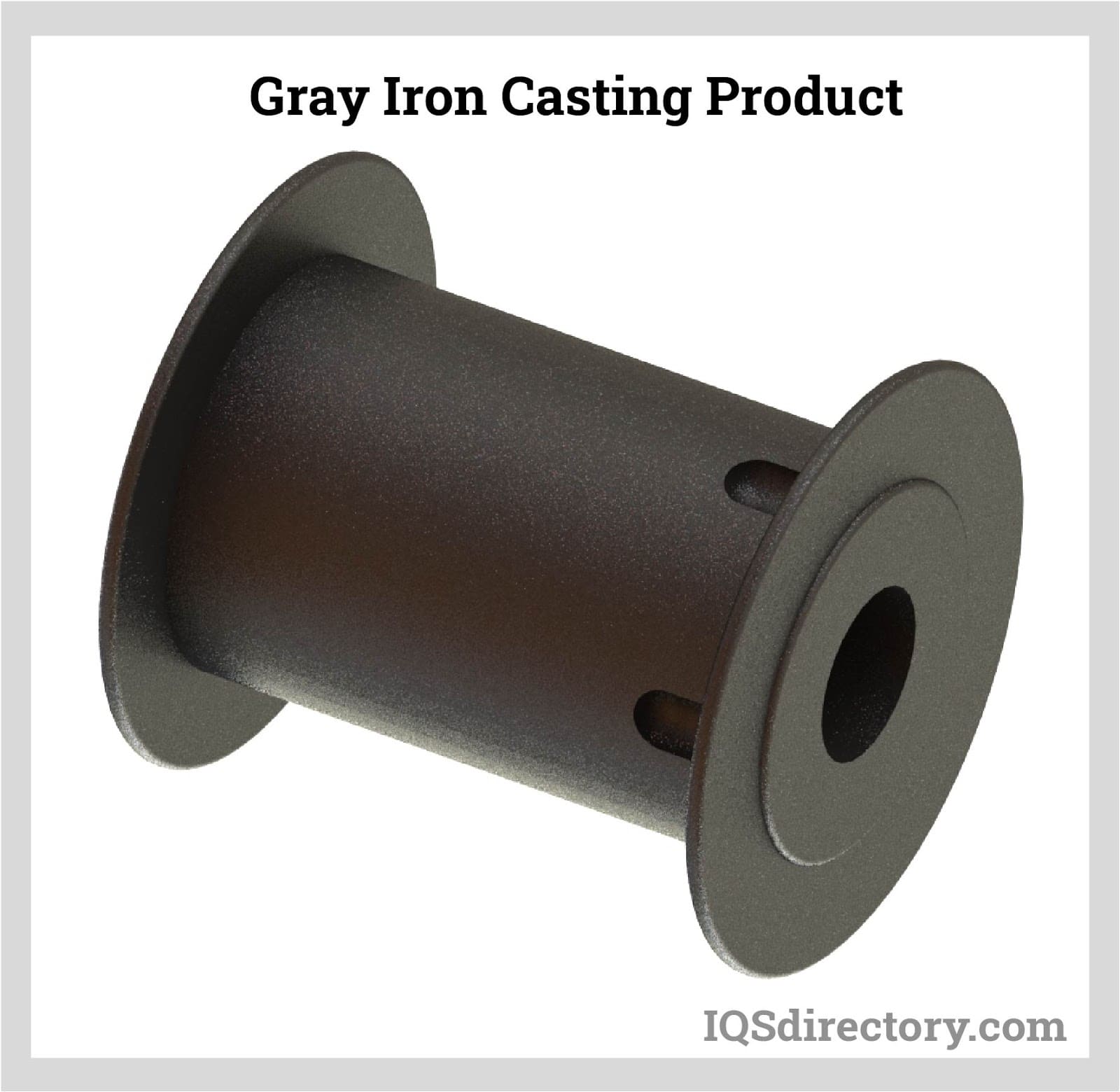
Todas estas propiedades mecánicas están controladas pola forma da escama de grafito e o tamaño das escamas de grafito, que están presentes na microestrutura da fundición gris.
Fundición de ferro branco
Este tipo de ferro ten superficies fracturadas que son brancas debido á presenza dun precipitado de carburo de ferro chamado cementita. O carbono que está contido no ferro fundido branco precipita fóra do fundido como cementita de fase estable en lugar de como grafito. Isto conséguese cun menor contido de silicio como axente de grafitización e unha velocidade de refrixeración subministrada máis rápida. Despois desta precipitación, a cementita fórmase como partículas grandes.
Durante a precipitación do carburo de ferro, o precipitado extrae carbono do fundido orixinal, movendo así a mestura cara a outra máis próxima ao eutéctico. A fase restante é baixar o ferro a austenita de carbono, que se transforma en martensita unha vez arrefriada.
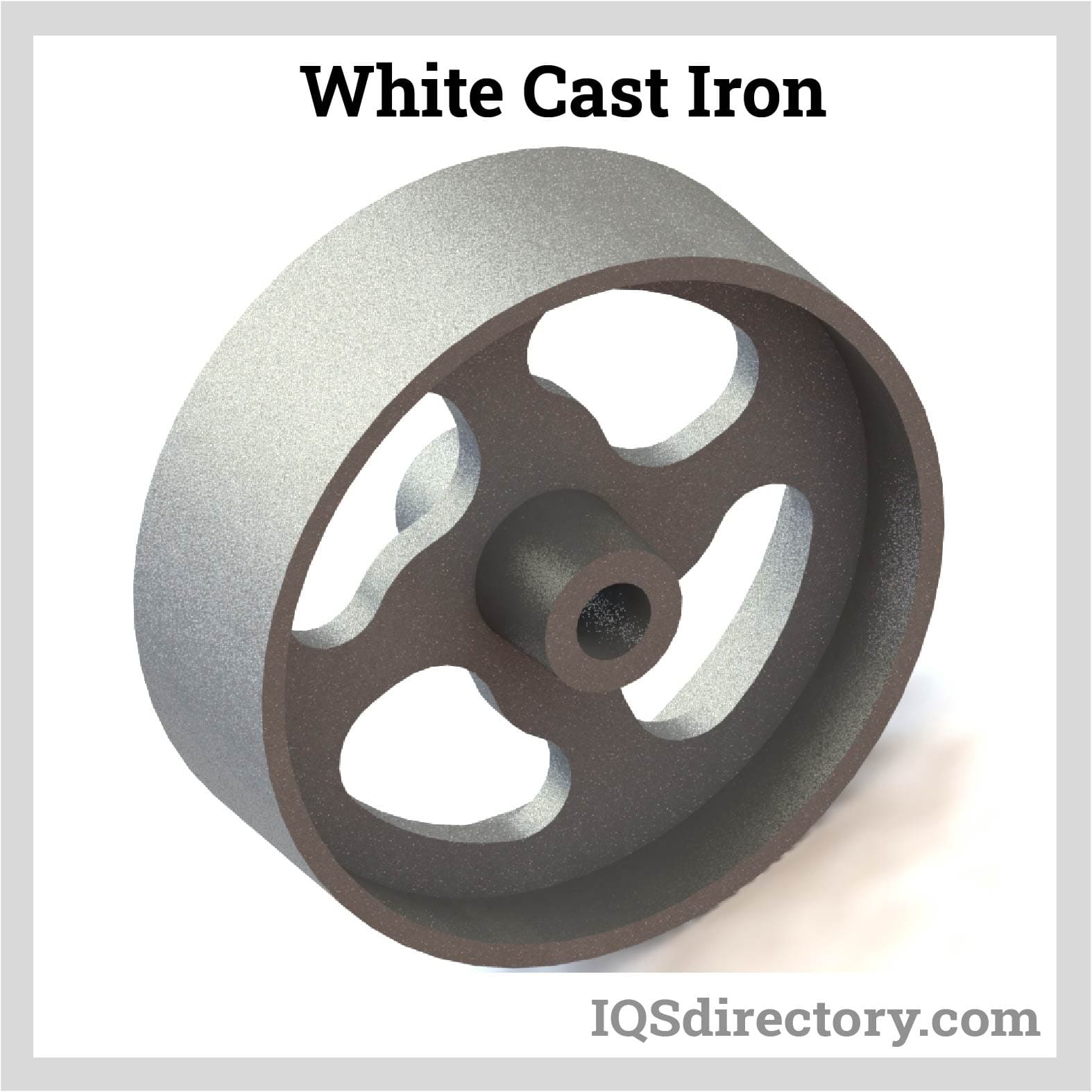
Estes carburos eutécticos contidos son demasiado grandes para proporcionar o beneficio do endurecemento por precipitación. Nalgúns aceiros pode haber precipitados de cementita moito máis pequenos que poden levar a deformación do plástico ao impedir o movemento das dislocacións a través da matriz de ferrita de ferro puro. Teñen unha vantaxe xa que aumentan a dureza do ferro fundido simplemente pola súa propia dureza e fracción de volume. Isto fai que a dureza a granel poida ser aproximada mediante unha regra de mesturas.
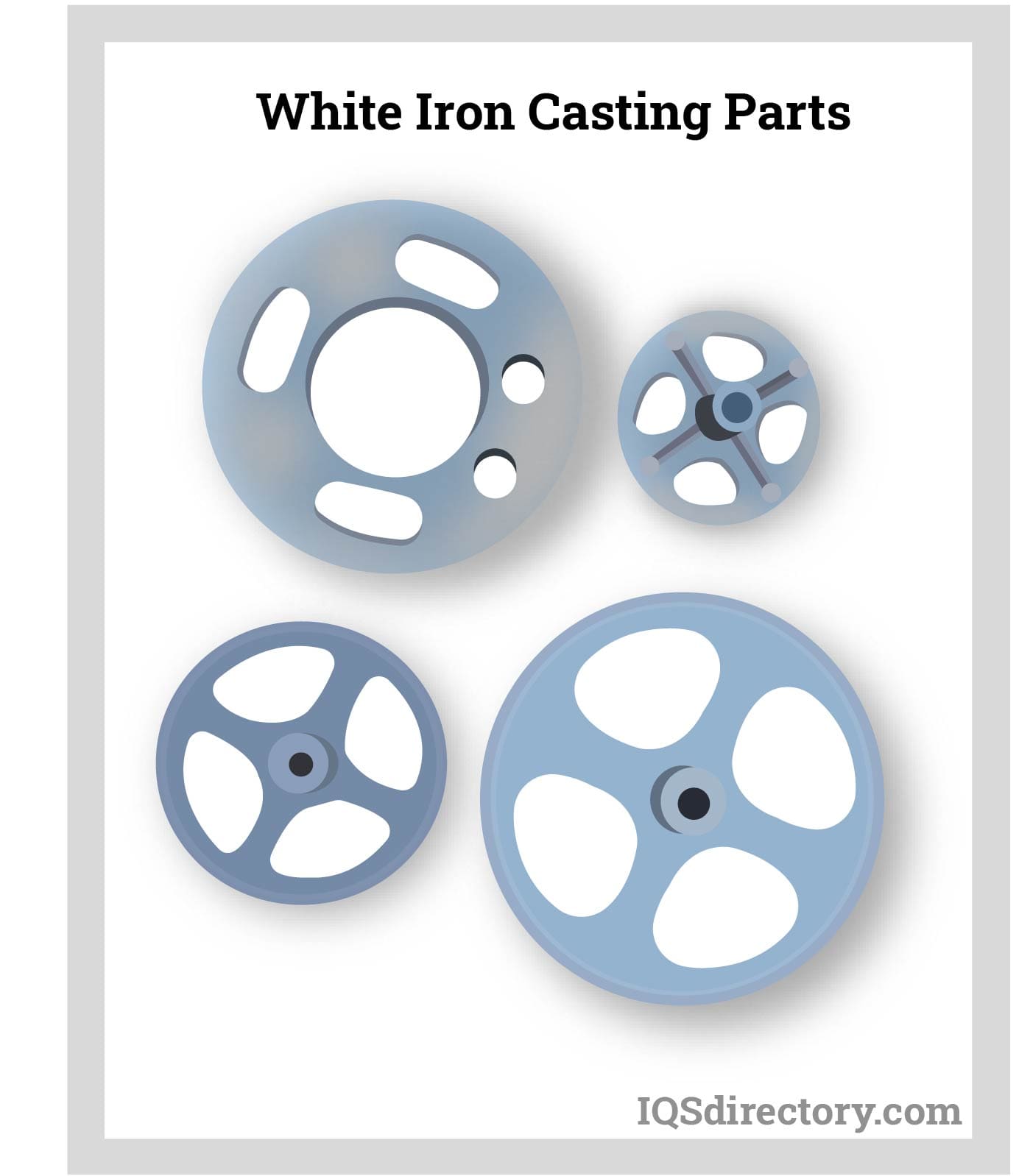
Esta dureza ofrécese a costa da dureza en calquera caso. O ferro fundido branco pódese clasificar xeralmente como cemento, xa que o carburo constitúe unha fracción maior do material. O ferro branco é demasiado fráxil para ser usado en compoñentes estruturais, pero debido á súa boa dureza, resistencia á abrasión e baixo custo, pódese usar como superficie de desgaste das bombas de purín.
É difícil arrefriar pezas de fundición grosas a un ritmo máis rápido, o que é suficiente para solidificar a fundición como fundición branca, sen embargo, pódese utilizar un arrefriamento rápido para solidificar un inferno de fundición branca e despois quedará o resto. arrefriar a un ritmo máis lento formando así un núcleo de fundición gris. Esta fundición resultante chámase fundición fría e contén os beneficios de ter unha superficie dura pero cun interior máis resistente.
As aliaxes de ferro branco de alto cromo tiñan a capacidade de permitir a fundición masiva dun impulsor de 10 toneladas para ser fundido en area. Isto débese ao feito de que o cromo reduce a velocidade de arrefriamento necesaria para producir carburos a través dos maiores espesores de material. Os carburos cunha excelente resistencia á abrasión tamén son producidos por elementos de cromo.
Fundición de ferro maleable
O ferro fundido maleable comeza como unha fundición de ferro branco, despois tratado térmicamente a temperaturas duns 950 °C durante dous ou un só día, e despois arrefríase durante o mesmo período de tempo.
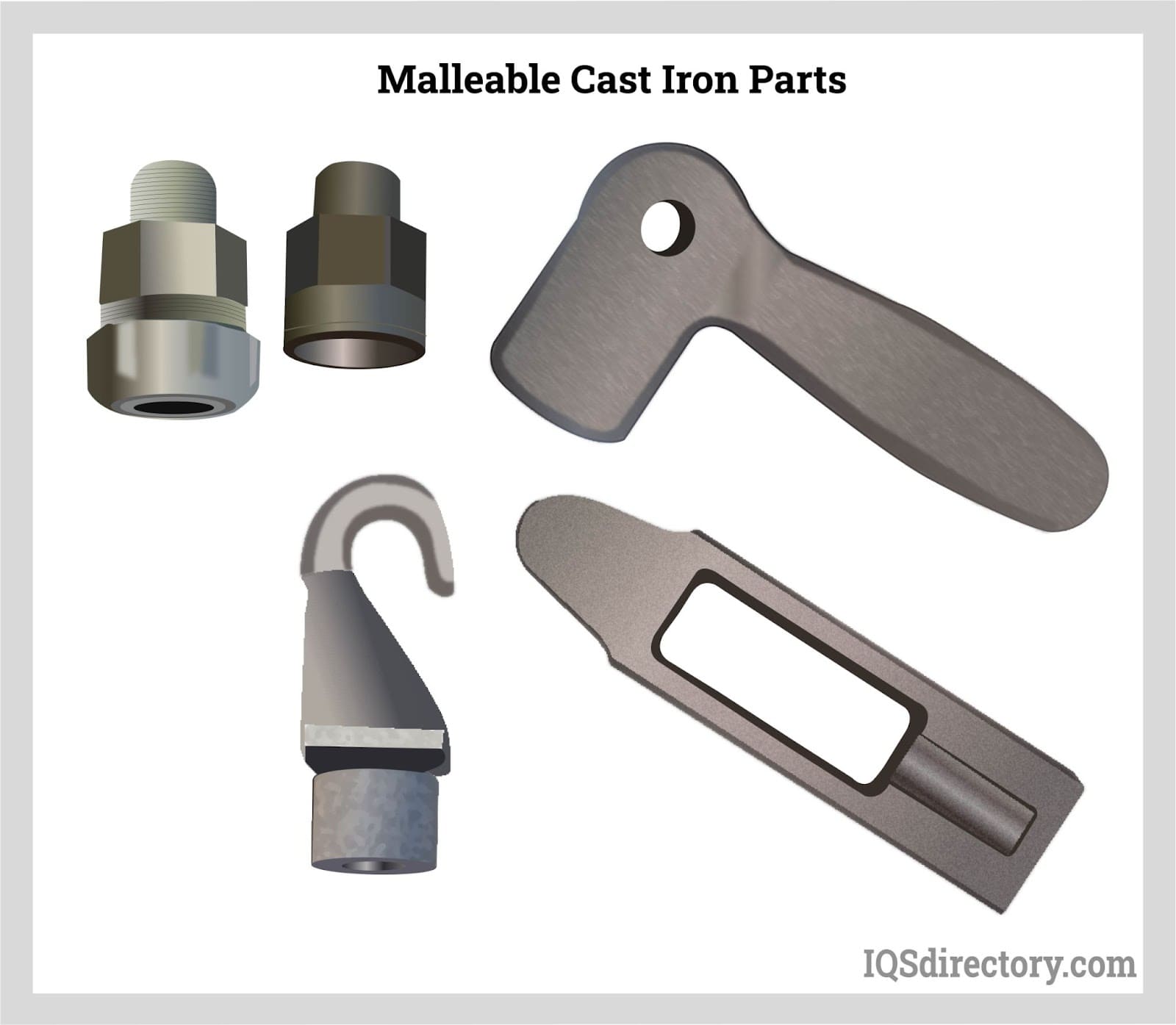
O carbono do carburo de ferro transfórmase despois en grafito e ferrita máis carbono debido a este proceso de quecemento e arrefriamento. Este é un proceso baixo, pero permite que a tensión superficial transforme o grafito en partículas esferoidais en lugar de escamas.
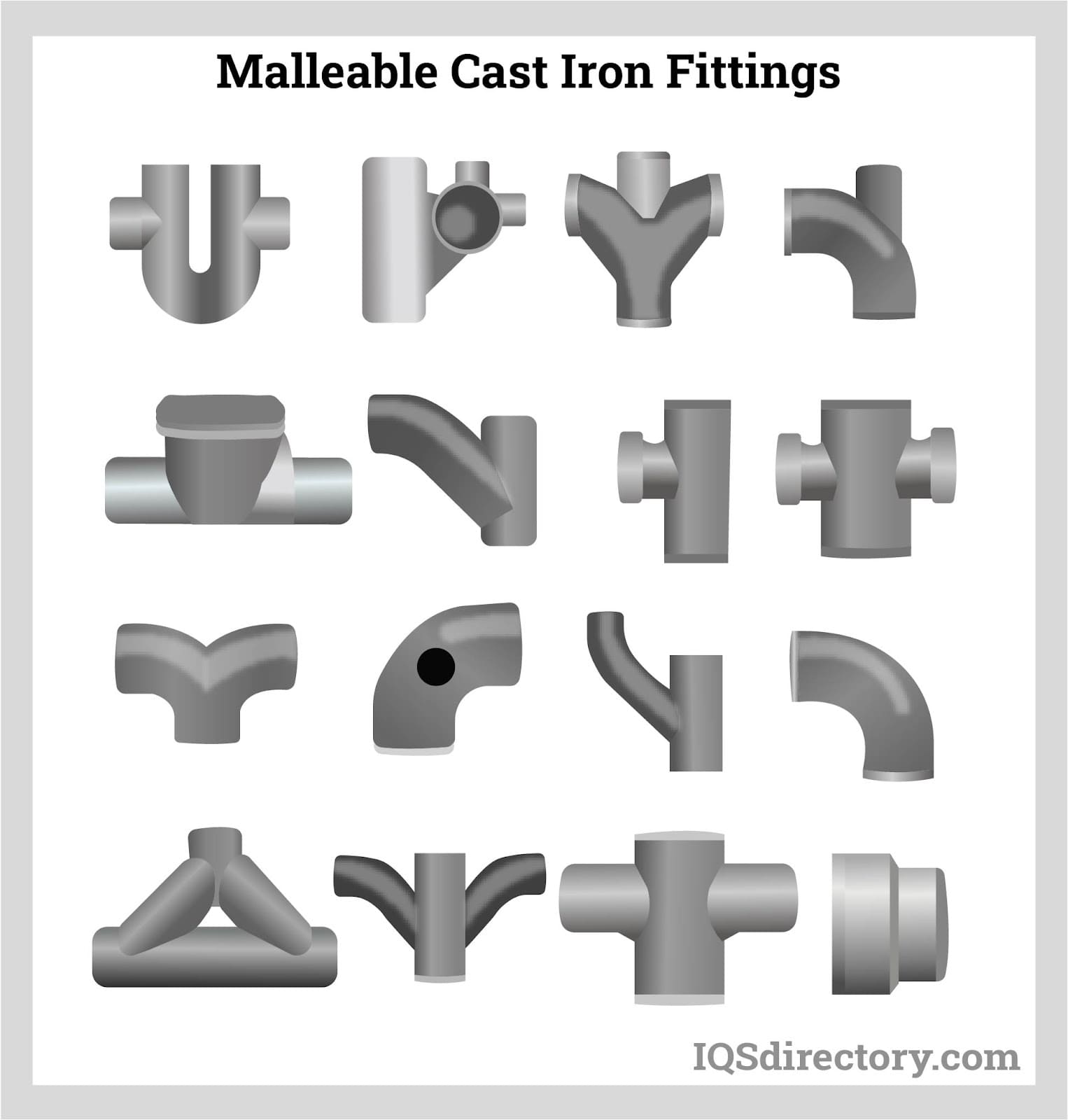
Os esferoides son relativamente curtos e están máis afastados uns dos outros debido á súa baixa relación de aspecto. Tamén conteñen unha sección transversal inferior, fenda de propagación e un fotón. A diferenza dos flocos, conteñen límites contundentes que participan no alivio dos problemas de concentración de estrés que se atopan na fundición gris. Con todo, as propiedades incluídas na fundición maleable parécense máis ás do aceiro de natureza suave.
Fundición de ferro dúctil
Ás veces denominada fundición nodular, esta fundición ten o seu grafito en forma de nódulos moi pequenos, tendo o grafito a forma de capas que son concéntricas e forman así os nódulos. Debido a isto, as propiedades defundición dúctilson os dun aceiro esponxoso que non ten efectos de concentración de tensión producidos polas escamas do grafito.
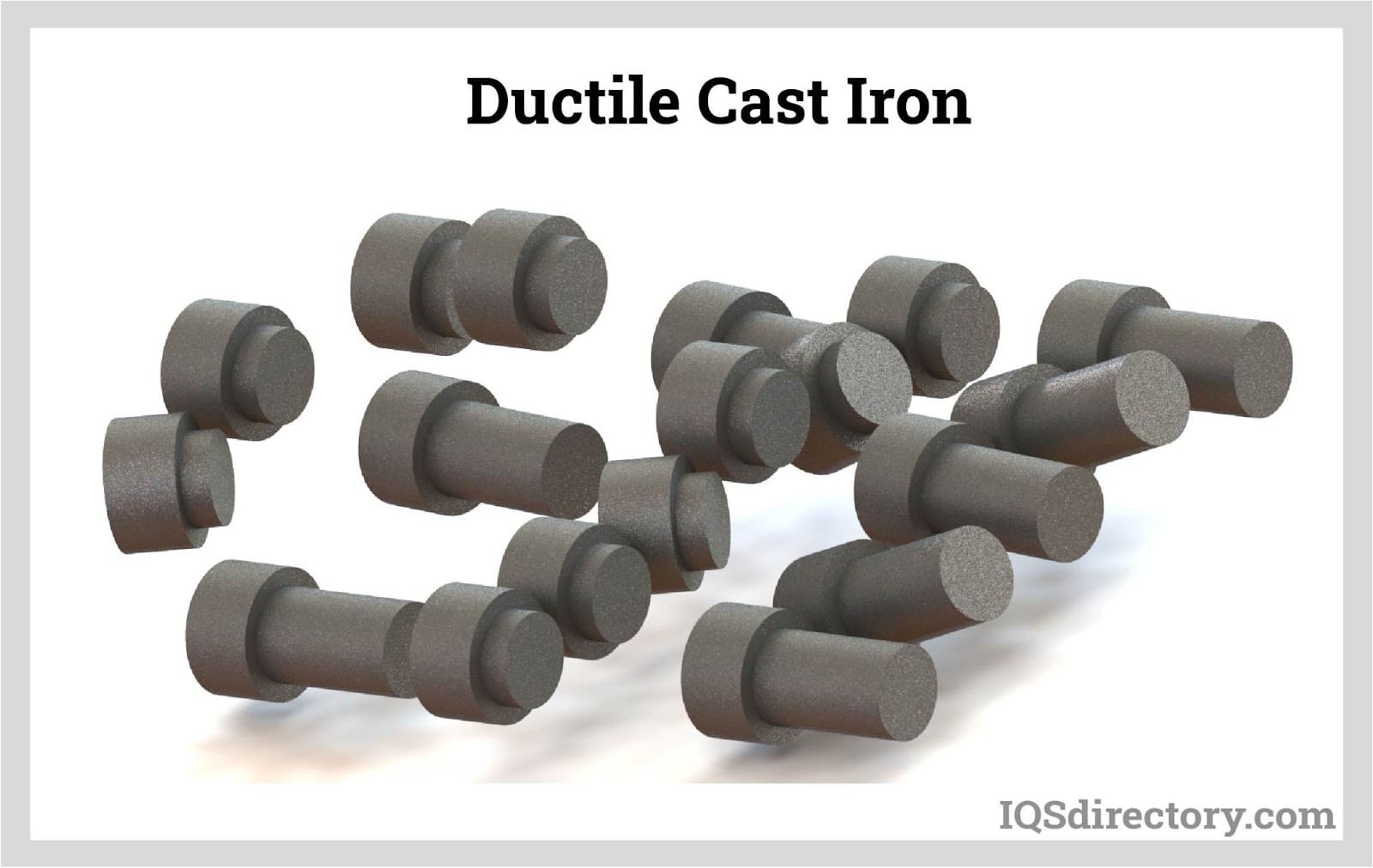
A cantidade de concentración de carbono contida é de entre o 3 e o 4 por cento, e a de silicio é de entre o 1,8 e o 2,8 por cento. Pequenas cantidades de 0,02 por cento a 0,1 por cento de magnesio e só de 0,02 por cento a 0,04 por cento de cerio cando se engaden a estas aliaxes ralentizan a velocidade á que crece a precipitación do grafito a través da unión aos bordos das pistas de grafito.
O carbono pode ter a posibilidade de separarse como partículas esferoidais a medida que o material se solidifica, debido ao control coidadoso doutros elementos e ao tempo adecuado durante o proceso. As partículas resultantes son similares á fundición maleable, pero as pezas pódense fundir con seccións máis grandes.
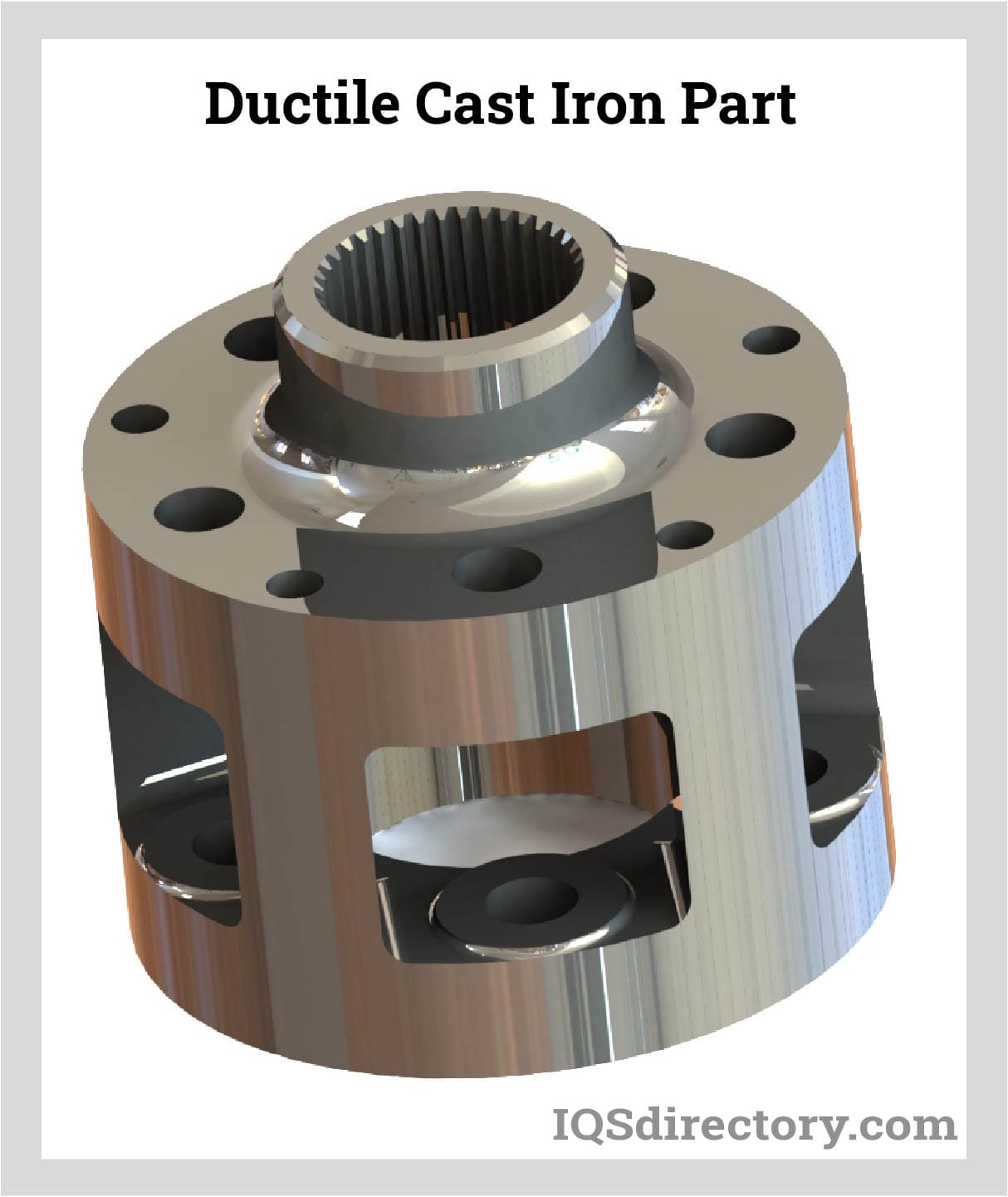
Elementos de aleación
As propiedades do ferro fundido cámbianse e engádense en varios elementos de aliaxe ou aliantes na fundición. En liña co carbono está o elemento silicio porque ten a capacidade de expulsar o carbono da solución. Unha porcentaxe menor de silicio non pode conseguilo completamente xa que permite que o carbono permaneza na solución, formando así carburo de ferro e producindo tamén fundición branca.
Unha maior porcentaxe ou concentración de silicio é capaz de forzar o carbono fóra da solución e despois formar grafito e tamén producir fundición gris. Outros axentes de aliaxe non sinalados inclúen manganeso, cromo, titanio e despois vanadio. Estes contrarrestan o silicio, tamén favorecen a retención de carbono e así tamén a formación de carburos. O níquel e o elemento cobre teñen unha vantaxe xa que aumentan a resistencia e a maquinabilidade, pero entón non poden cambiar a cantidade de carbono formado.
O carbono que está en forma de grafito dá como resultado un ferro máis brando, reducindo así o efecto da contracción, diminuíndo a resistencia e diminuíndo a densidade contida. O xofre é principalmente un contaminante cando está contido, e forma sulfuro de ferro que impide a formación de grafito e tamén aumenta a dureza.
A desvantaxe imposta polo xofre é que fai viscoso o ferro fundido, o que provoca defectos. Para atender e eliminar os efectos do xofre, engádese manganeso á solución. Isto faise porque cando os dous se combinan forman sulfuro de manganeso en lugar de sulfuro de ferro. O sulfuro de manganeso resultante é máis lixeiro que a fusión e tende a saír flotando da fusión e entrar na escoura.
A cantidade aproximada de manganeso necesaria para cancelar os efectos do xofre é de 1,7 unidades de contido de xofre e un 0,3 por cento adicional engadido na parte superior. A adición de máis desta cantidade de manganeso dá como resultado a formación de carburo de manganeso e isto aumenta a dureza e o arrefriamento, excepto no ferro gris onde ata o 1 por cento de manganeso pode aumentar a resistencia e a densidade contida. O níquel é un dos elementos de aliaxe máis xerais porque ten tendencia a refinar a perlita e a estrutura do grafito, mellorando así a tenacidade e igualando a diferenza de dureza entre os espesores de sección.
Engádese cromo en pequenas cantidades para reducir o grafito libre e producir un arrefriamento. Isto débese a que o cromo é un poderoso estabilizador de carburo e, nalgúns casos, pode funcionar xunto co níquel. Para o cromo tamén se pode engadir unha pequena cantidade de estaño. O cobre engádese na cuchara ou no forno na orde do 0,5 por cento ao 2,5 por cento para conseguir un arrefriamento reducido, o grafito refinado e o incremento da fluidez. Tamén se pode engadir molibdeno na orde de 0,3 por cento a 1 por cento para aumentar tamén o arrefriamento, refinar o grafito e refinar a estrutura da perlita.
Normalmente engádese traballando en liña con níquel, cobre e cromo para producir ferros de alta resistencia. O elemento titanio engádese para funcionar como desgasificador e desoxidante, e aumentar a fluidez. Proporcións de 0,15 por cento a 0,5 por cento do elemento vanadio engádense ao ferro fundido e axudan a estabilizar a cementita, para aumentar a dureza e resistir o desgaste e os efectos da calor.
O circonio axuda a formar grafito e engádese en proporcións de aproximadamente 0,1 por cento a 0,3 por cento. Este elemento tamén axuda a desoxidar e aumentar a fluidez. Nas fontes de ferro maleable, para aumentar a cantidade de silicio que se pode engadir, bótase bismuto nunha escala de 0,002 por cento a 0,01 por cento. No ferro branco, engádese o elemento boro, que axuda á produción de ferro que é maleable e reduce o efecto de engrosamento do elemento bismuto.