Tipi di getti di ghisa
Tipi di getti di ghisa
In questo capitolo verranno esaminati i vari tipi di getti di ghisa.
Fusione di ghisa grigia
La caratteristica della ghisa grigia è la microstruttura grafica, che può causare fratture al materiale e conferire un aspetto grigio. Questa è la tipologia di ghisa più comunemente utilizzata e anche il materiale di fusione più comunemente utilizzato in base al peso. La maggior parte delle ghise grigie presenta una decomposizione chimica del 2,5-4% di carbonio, dell'1-3% di silicio e il resto è una composizione di ferro.
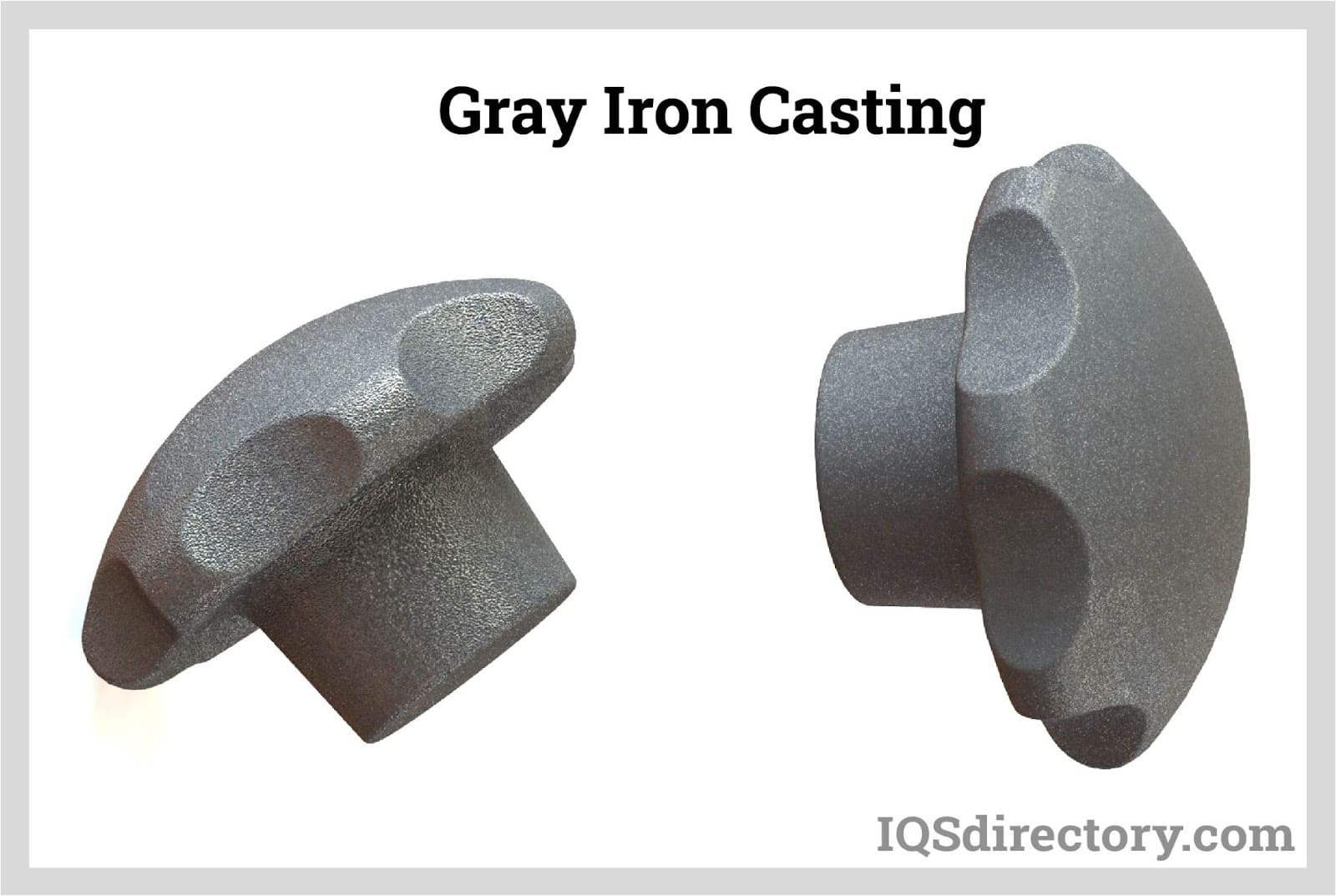
Questo tipo di ghisa ha una minore resistenza alla trazione e agli urti rispetto all'acciaio. La sua resistenza alla compressione è paragonabile a quella dell'acciaio a basso e medio tenore di carbonio.
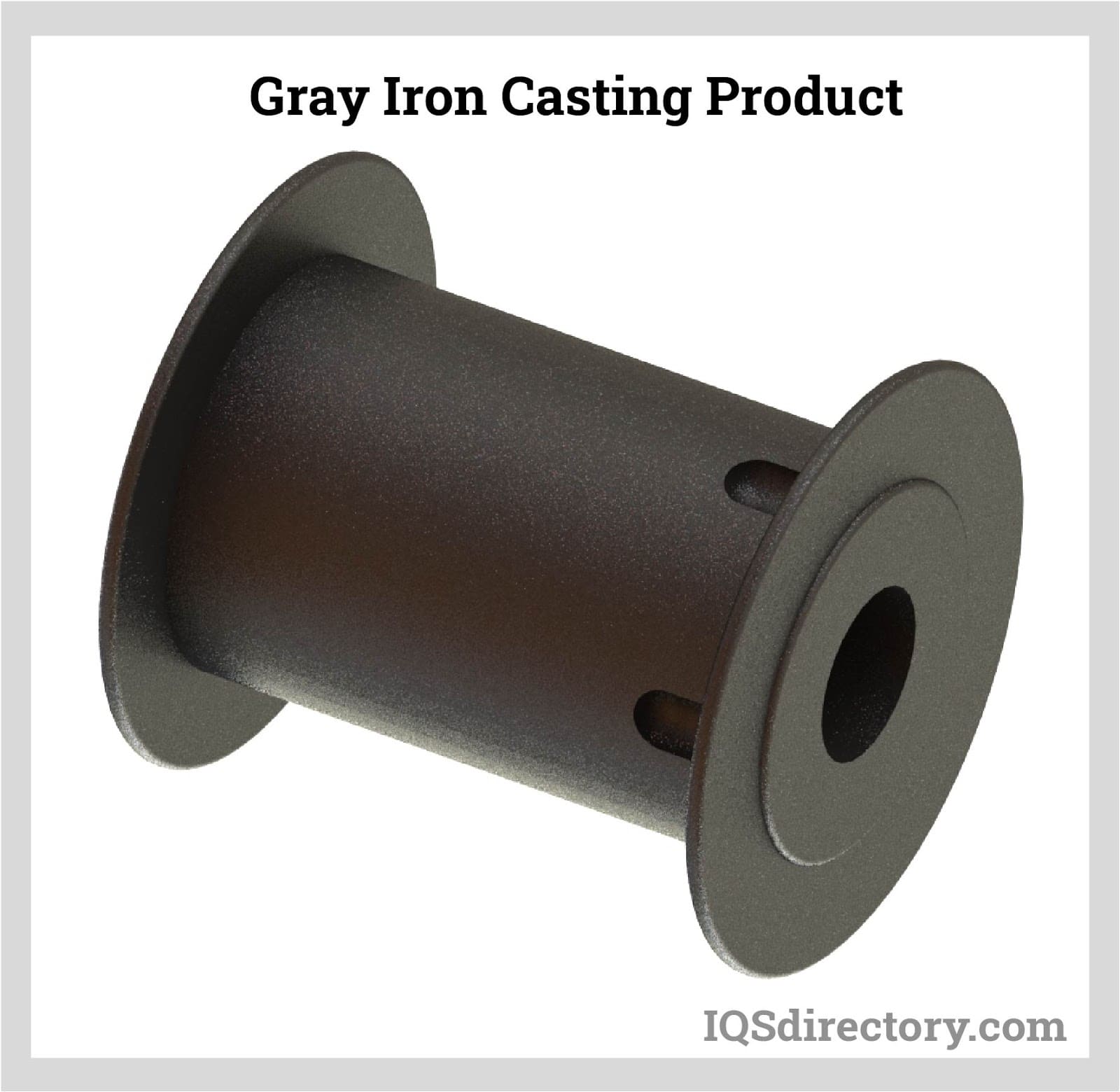
Tutte queste proprietà meccaniche sono controllate dalla forma e dalle dimensioni delle scaglie di grafite, presenti nella microstruttura della ghisa grigia.
Fusione di ghisa bianca
Questo tipo di ghisa presenta superfici fratturate di colore bianco a causa della presenza di un precipitato di carburo di ferro chiamato cementite. Il carbonio contenuto nella ghisa bianca precipita dalla fusione sotto forma di cementite in fase stabile anziché di grafite. Questo risultato si ottiene grazie a un minore contenuto di silicio come agente grafitizzante e a una maggiore velocità di raffreddamento. Dopo questa precipitazione, la cementite si forma in particelle di grandi dimensioni.
Durante la precipitazione del carburo di ferro, il precipitato assorbe carbonio dalla massa fusa originale, spostando così la miscela verso una fase più vicina all'eutettico. La fase rimanente è l'austenite di ferro che si riduce a carbonio, trasformandosi in martensite una volta raffreddata.
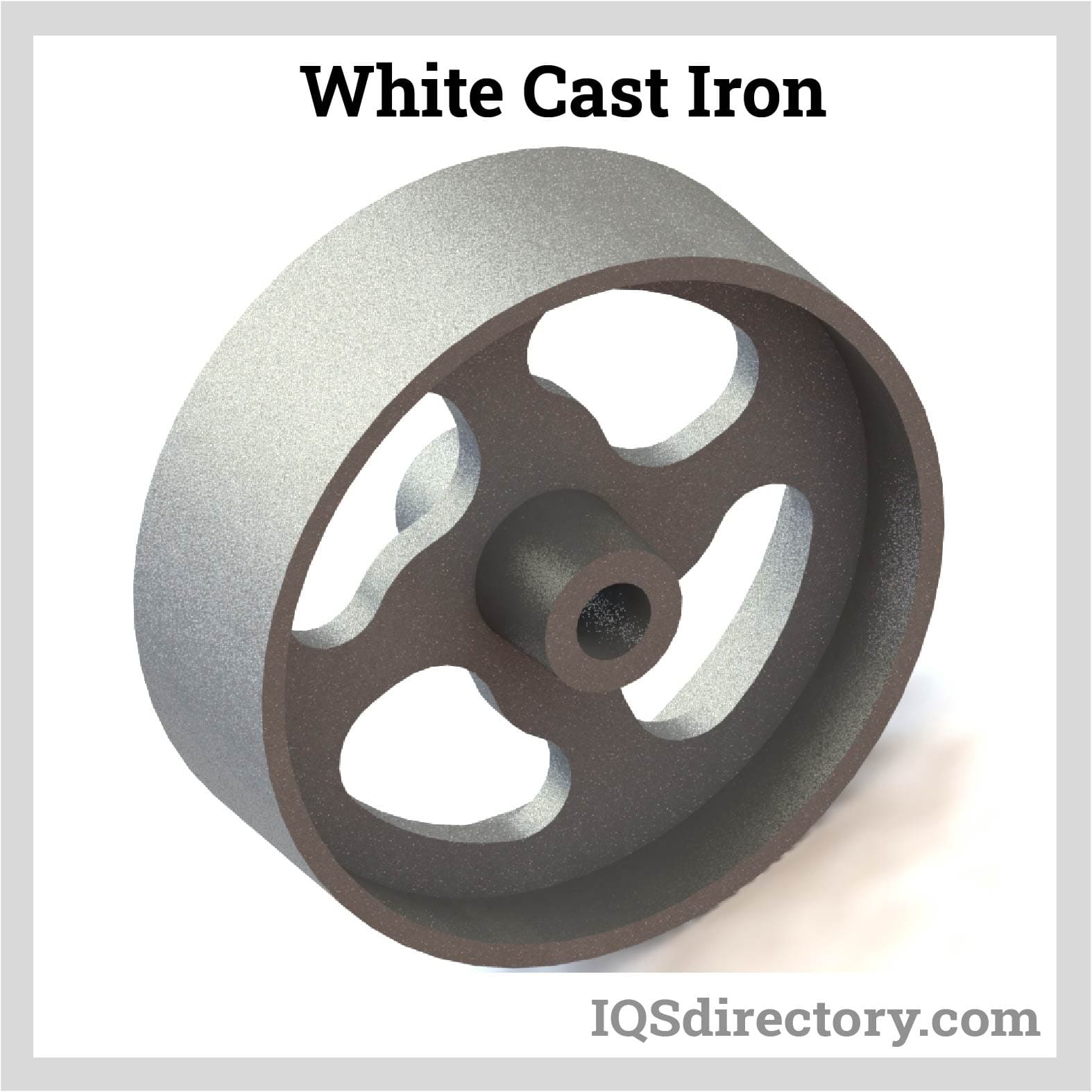
Questi carburi eutettici contenuti sono troppo grandi per offrire i benefici dell'indurimento per precipitazione. In alcuni acciai potrebbero essere presenti precipitati di cementite molto più piccoli che potrebbero favorire la deformazione plastica impedendo il movimento delle dislocazioni attraverso la matrice di ferrite pura. Questi presentano un vantaggio in quanto aumentano la durezza di massa della ghisa semplicemente grazie alla loro durezza e frazione di volume. Ciò consente di approssimare la durezza di massa con una regola di miscele.
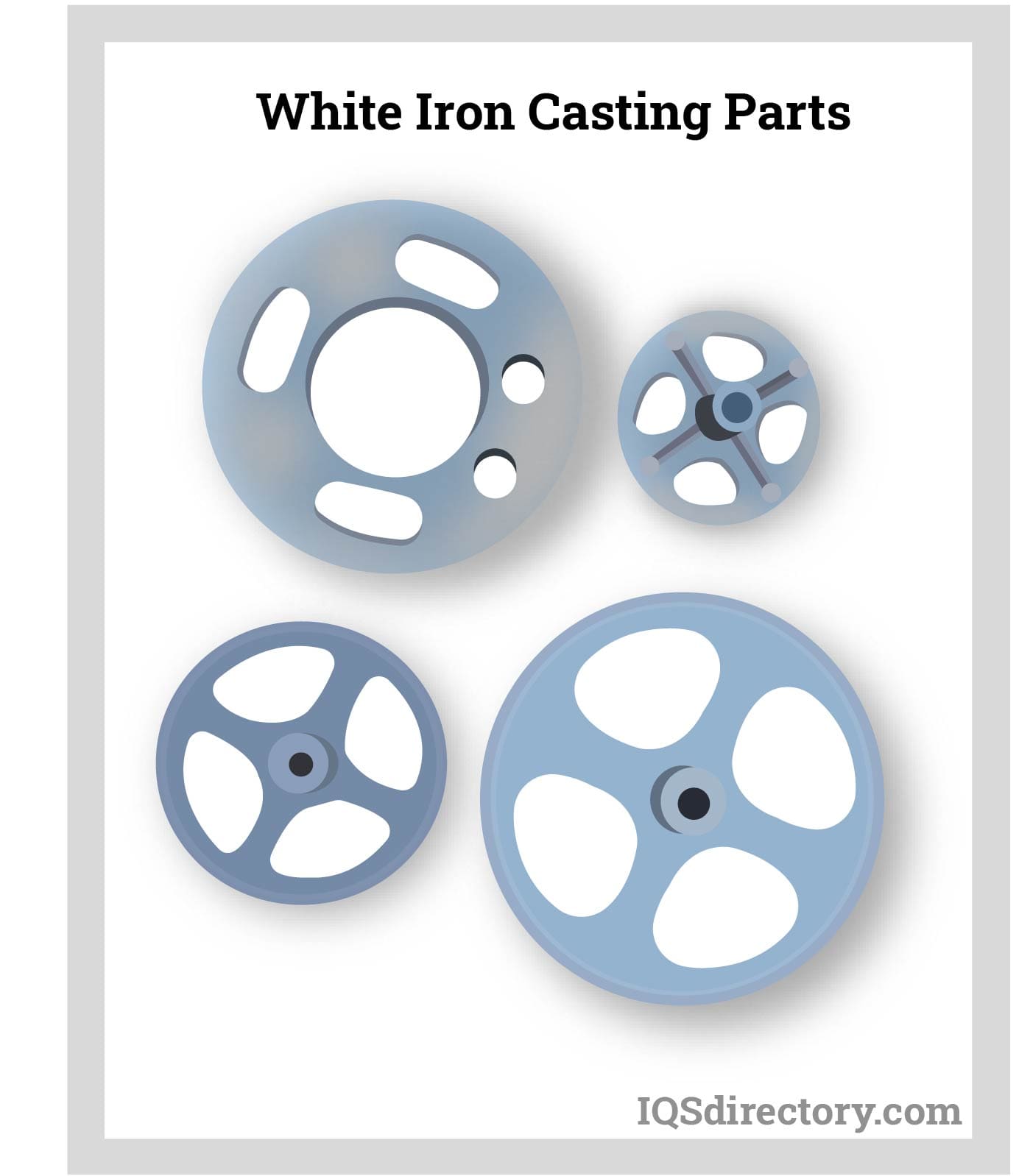
Questa durezza è comunque offerta a scapito della tenacità. La ghisa bianca può essere generalmente classificata come cemento, poiché il carburo costituisce una frazione maggiore del materiale. La ghisa bianca è troppo fragile per essere utilizzata in componenti strutturali, ma grazie alla sua buona durezza, alla resistenza all'abrasione e al basso costo, può essere utilizzata come superficie di usura delle pompe per fanghi.
È difficile raffreddare getti spessi a una velocità sufficiente a solidificare la fusione come ghisa bianca, tuttavia è possibile utilizzare un raffreddamento rapido per solidificare una grande quantità di ghisa bianca e successivamente raffreddare la parte rimanente a un ritmo più lento, formando così un nucleo di ghisa grigia. La fusione risultante è chiamata fusione raffreddata e presenta i vantaggi di avere una superficie dura ma un interno più resistente.
Le leghe di ferro bianco ad alto tenore di cromo avevano la capacità di consentire la fusione in sabbia di una girante di circa 10 tonnellate. Ciò è dovuto al fatto che il cromo riduce la velocità di raffreddamento necessaria per produrre carburi grazie al maggiore spessore del materiale. Anche gli elementi al cromo producono carburi con un'eccellente resistenza all'abrasione.
Fusione di ghisa malleabile
La ghisa malleabile inizia come fusione di ghisa bianca, quindi viene trattata termicamente a temperature di circa 950 °C per due o un solo giorno e poi raffreddata per lo stesso periodo di tempo.
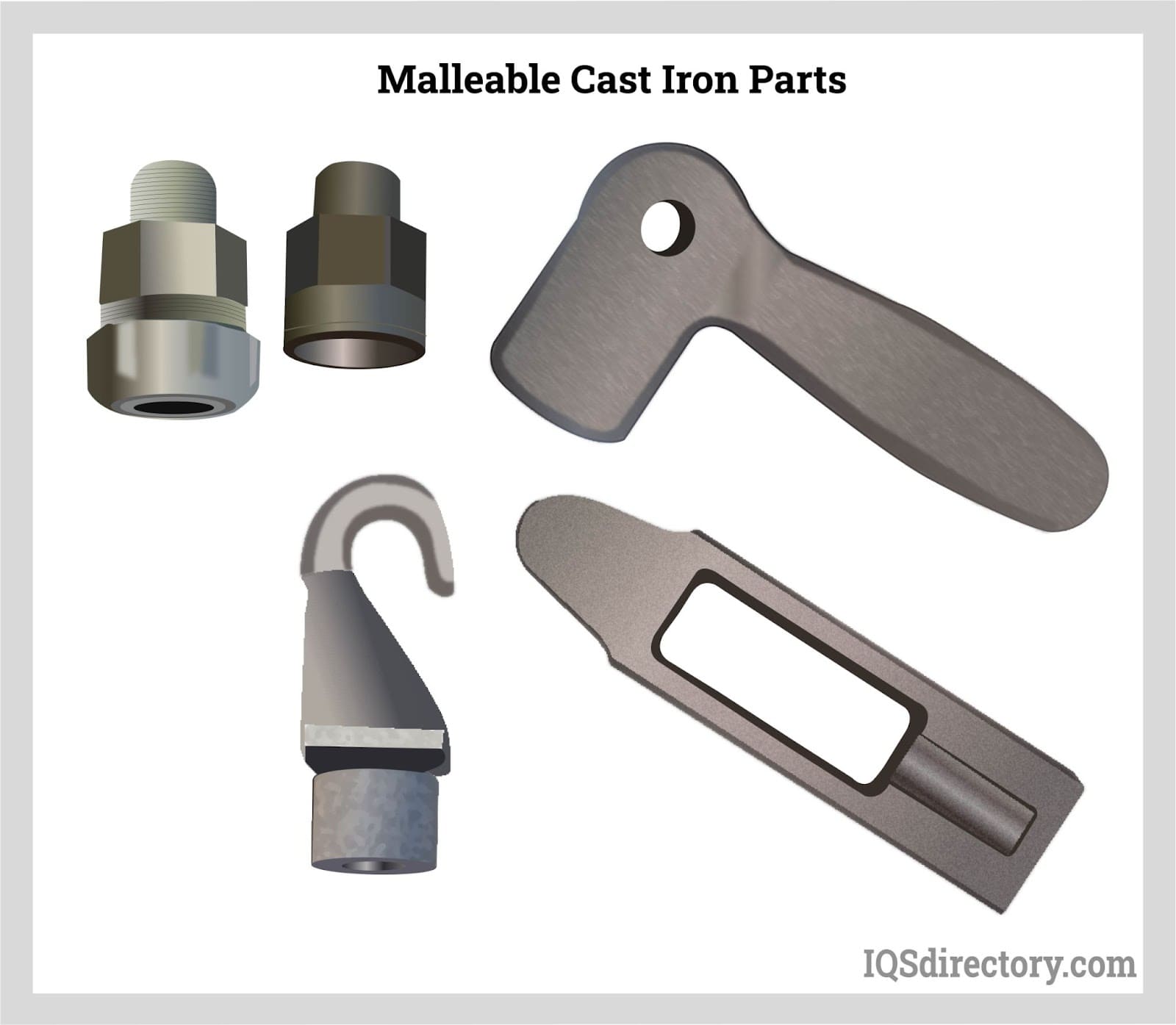
Il carbonio presente nel carburo di ferro si trasforma quindi in grafite e ferrite, più carbonio, grazie a questo processo di riscaldamento e raffreddamento. Si tratta di un processo a bassa energia, ma consente alla tensione superficiale di trasformare la grafite in particelle sferoidali anziché in scaglie.
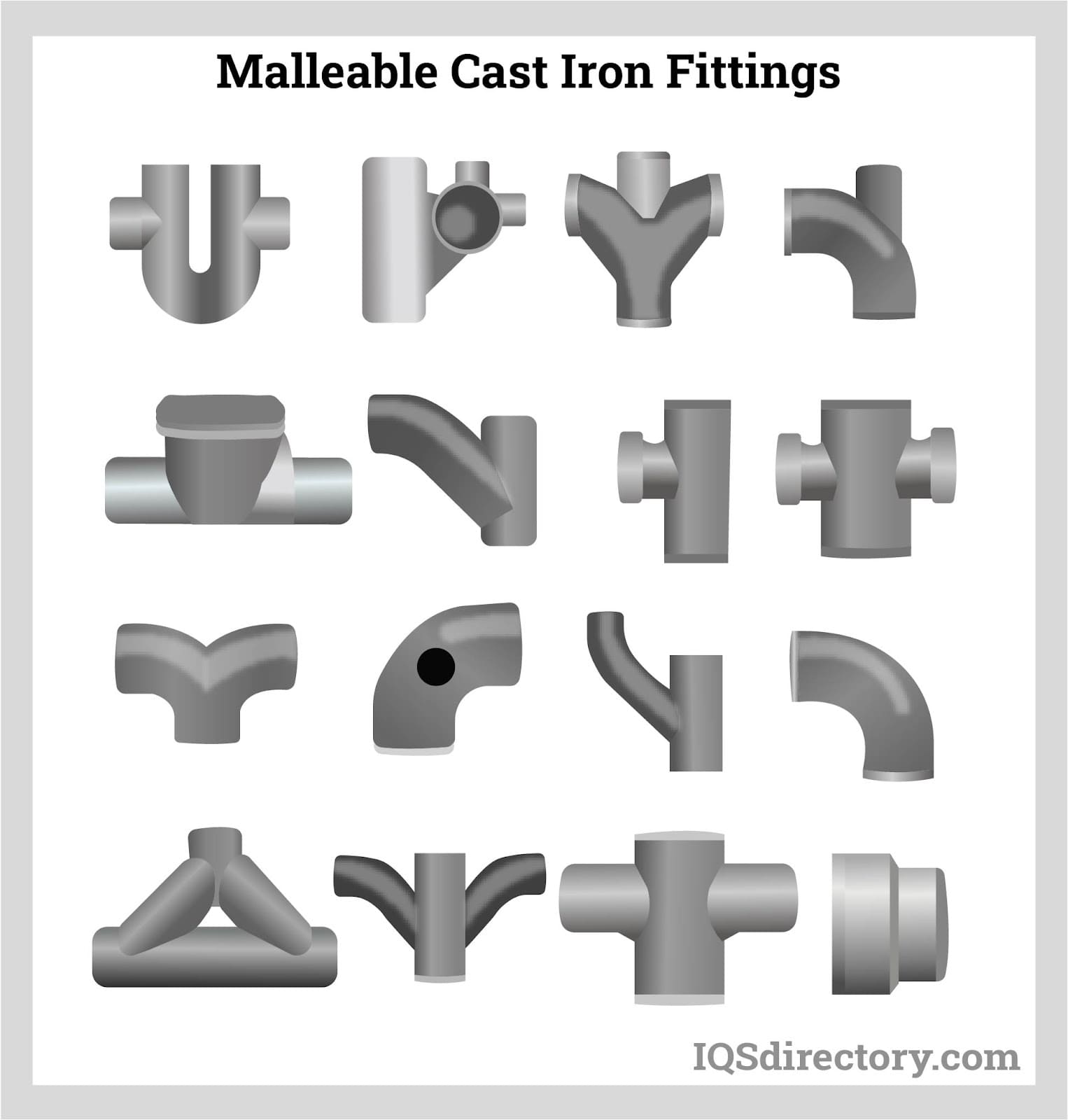
Gli sferoidi sono relativamente corti e più distanti tra loro a causa del loro basso rapporto d'aspetto. Presentano inoltre una sezione trasversale inferiore, una cricca che si propaga e un fotone. A differenza delle scaglie, presentano bordi smussati che contribuiscono ad alleviare i problemi di concentrazione degli sforzi tipici della ghisa grigia. Nel complesso, le proprietà della ghisa malleabile sono più simili a quelle dell'acciaio, che è di natura dolce.
Fusione di ghisa duttile
Talvolta definita ghisa nodulare, questa ghisa presenta la sua grafite sotto forma di noduli molto piccoli, con la grafite che presenta strati concentrici che formano i noduli. Per questo motivo, le proprietà dighisa duttilesono quelle di un acciaio spugnoso che non presenta effetti di concentrazione di stress prodotti dalle scaglie di grafite.
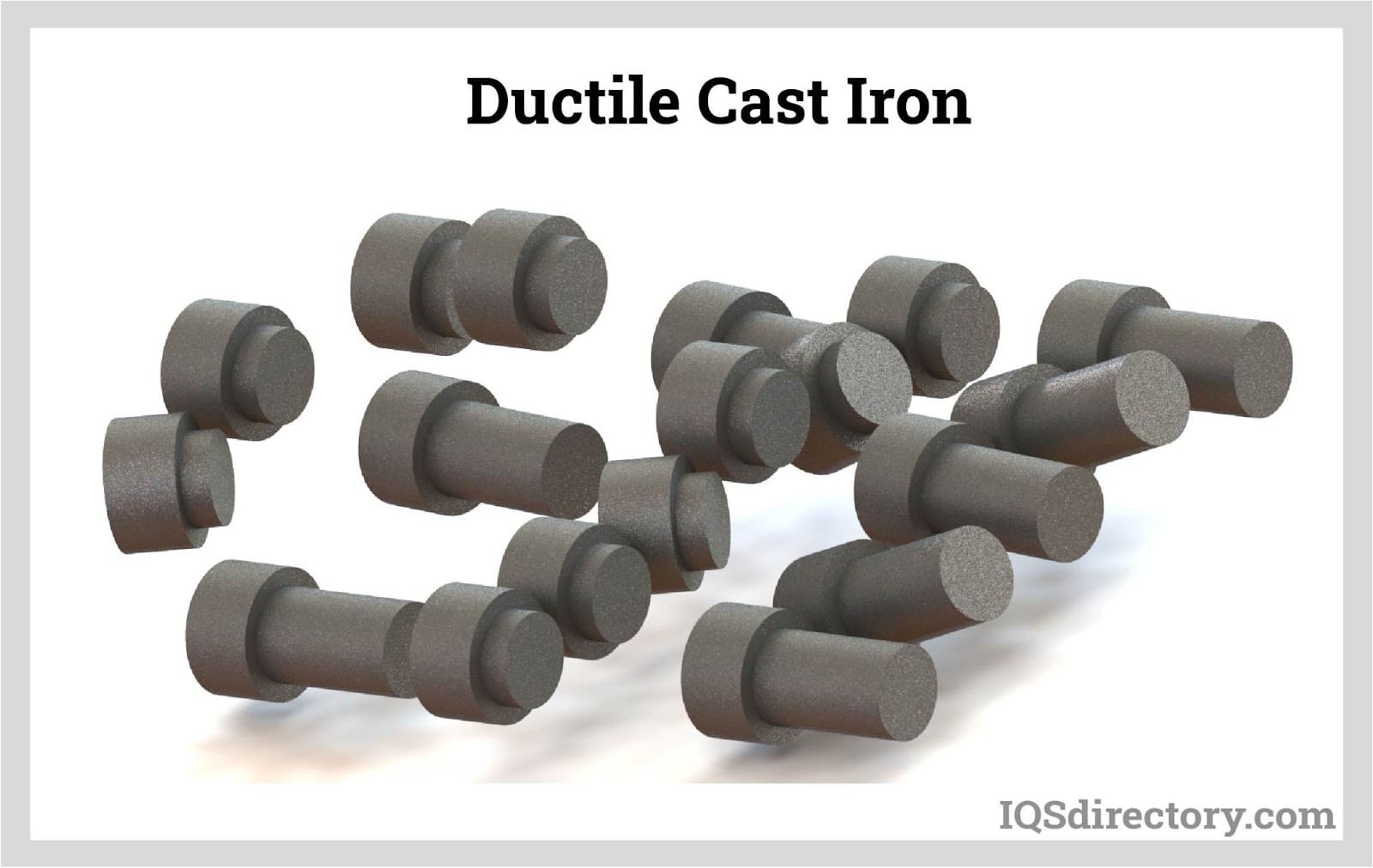
La concentrazione di carbonio contenuta è compresa tra il 3 e il 4% circa, mentre quella di silicio è compresa tra l'1,8 e il 2,8%. Piccole quantità di magnesio, tra lo 0,02 e lo 0,1%, e solo tra lo 0,02 e lo 0,04% di cerio, aggiunte a queste leghe, rallentano la velocità con cui la grafite precipita attraverso il legame con i bordi delle corsie di grafite.
Il carbonio può presentare la possibilità di separarsi in particelle sferoidali durante la solidificazione del materiale, grazie all'attento controllo degli altri elementi e alla corretta tempistica durante il processo. Le particelle risultanti sono simili alla ghisa malleabile, ma è possibile fondere i pezzi con sezioni più grandi.
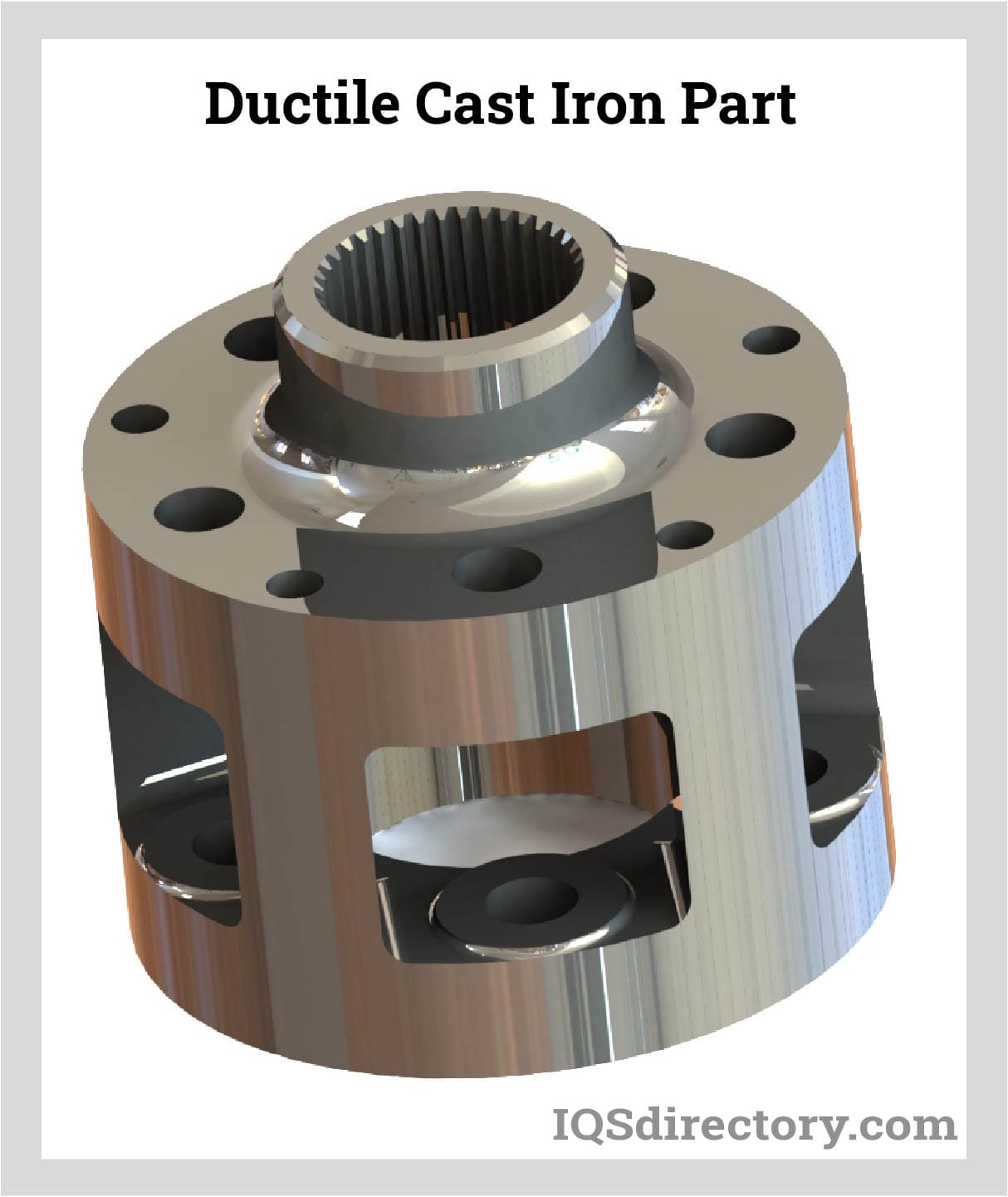
Elementi di lega
Le proprietà della ghisa vengono modificate e aggiunte a vari elementi di lega o alliganti. In linea con il carbonio, il silicio è un elemento che ha la capacità di espellere il carbonio dalla soluzione. Una percentuale inferiore di silicio non è in grado di raggiungere pienamente questo obiettivo, poiché consente al carbonio di rimanere nella soluzione, formando così carburo di ferro e producendo anche ghisa bianca.
Una percentuale o concentrazione maggiore di silicio è in grado di espellere il carbonio dalla soluzione e quindi formare grafite, producendo anche ghisa grigia. Altri agenti di lega non menzionati includono manganese, cromo, titanio e poi vanadio. Questi contrastano il silicio, promuovono anche la ritenzione del carbonio e quindi la formazione di carburi. Il nichel e il rame presentano un vantaggio in quanto aumentano la resistenza e la lavorabilità, ma non sono in grado di modificare la quantità di carbonio formato.
Il carbonio presente sotto forma di grafite conferisce al ferro una maggiore morbidezza, riducendo così l'effetto di ritiro, la resistenza e la densità. Lo zolfo, se presente, è principalmente un contaminante e forma solfuro di ferro, che impedisce la formazione di grafite e ne aumenta la durezza.
Lo svantaggio dello zolfo è che rende la ghisa fusa viscosa, causando difetti. Per compensare ed eliminare gli effetti dello zolfo, si aggiunge manganese alla soluzione. Questo perché, combinandosi, i due elementi formano solfuro di manganese anziché solfuro di ferro. Il solfuro di manganese risultante è più leggero della fusione e tende a fuoriuscire dalla fusione e a depositarsi nella scoria.
La quantità approssimativa di manganese necessaria per annullare gli effetti dello zolfo è pari a 1,7 unità di contenuto di zolfo più un ulteriore 0,3% aggiunto. L'aggiunta di una quantità di manganese superiore a questa si traduce nella formazione di carburo di manganese, che aumenta la durezza e la resistenza al freddo, tranne che nella ghisa grigia, dove fino all'1% di manganese può aumentare la resistenza e la densità. Il nichel è uno degli elementi di lega più generali perché tende a raffinare la perlite e la struttura della grafite, migliorandone così la tenacità e uniformando la differenza di durezza tra gli spessori delle sezioni.
Il cromo viene aggiunto in piccole quantità per ridurre la grafite libera e produrre una temperatura di raffreddamento. Questo perché il cromo è un potente stabilizzatore di carburi e, in alcuni casi, può agire in combinazione con il nichel. Anche per il cromo, è possibile aggiungere una piccola quantità di stagno sostitutivo. Il rame viene aggiunto nella siviera o nel forno in una percentuale compresa tra lo 0,5% e il 2,5% per ottenere una temperatura di raffreddamento inferiore, raffinare la grafite e aumentare la fluidità. Anche il molibdeno può essere aggiunto in una percentuale compresa tra lo 0,3% e l'1% per aumentare la temperatura di raffreddamento, raffinare la grafite e affinare la struttura perlitica.
Viene solitamente aggiunto lavorando in linea con nichel, rame e cromo per produrre ghise ad alta resistenza. Il titanio viene aggiunto per svolgere la funzione di degassante e disossidante, e per aumentarne la fluidità. Vanadio viene aggiunto alla ghisa in percentuali comprese tra lo 0,15% e lo 0,5%, contribuendo a stabilizzare la cementite, aumentandone la durezza e la resistenza all'usura e al calore.
Lo zirconio contribuisce alla formazione della grafite e viene aggiunto in percentuali che vanno dallo 0,1% allo 0,3%. Questo elemento contribuisce anche alla deossidazione e all'aumento della fluidità. Nelle fusioni di ghisa malleabile, per aumentare la quantità di silicio che può essere aggiunta, il bismuto viene colato in una percentuale compresa tra lo 0,002% e lo 0,01%. Nella ghisa bianca, viene aggiunto il boro, che favorisce la produzione di ferro malleabile e riduce l'effetto di ingrossamento del bismuto.