انواع ریختهگری آهن
انواع ریختهگری آهن
در این فصل به بررسی انواع مختلف ریختهگری آهن پرداخته خواهد شد.
ریختهگری چدن خاکستری
مشخصه چدن خاکستری، ریزساختار گرافیکی آن است که میتواند باعث ایجاد شکستگی در ماده شده و ظاهری خاکستری داشته باشد. این نوع چدن رایجترین نوع چدن و همچنین ماده ریختهگری رایج بر اساس وزن است. اکثر چدنهای خاکستری دارای تجزیه شیمیایی ۲.۵ تا ۴ درصد کربن، ۱ تا ۳ درصد سیلیکون و بقیه ترکیبی از آهن هستند.
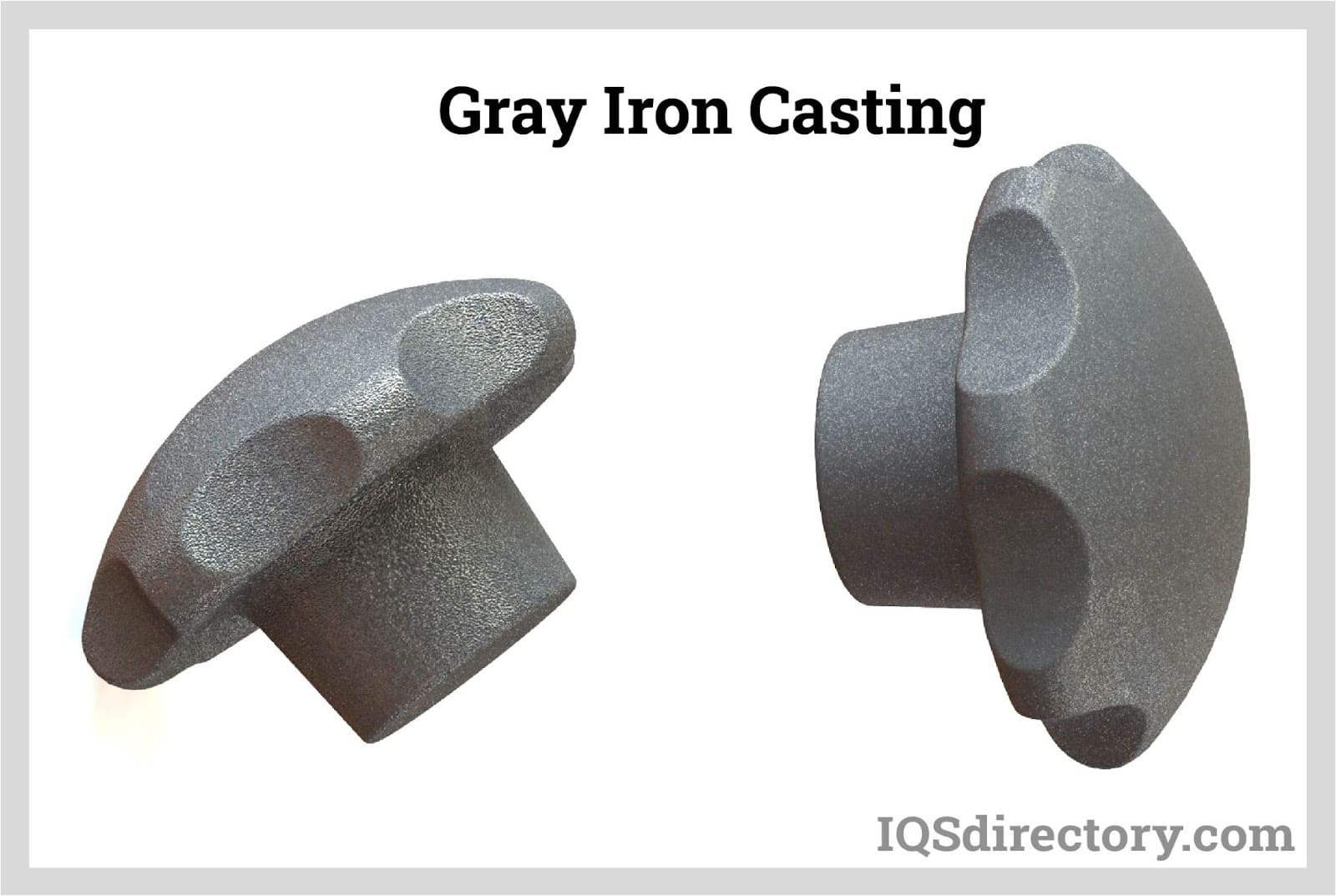
این نوع چدن در مقایسه با فولاد، استحکام کششی کمتر و مقاومت کمتری در برابر ضربه دارد. مقاومت فشاری آن با فولاد کم کربن و متوسط کربن قابل مقایسه است.
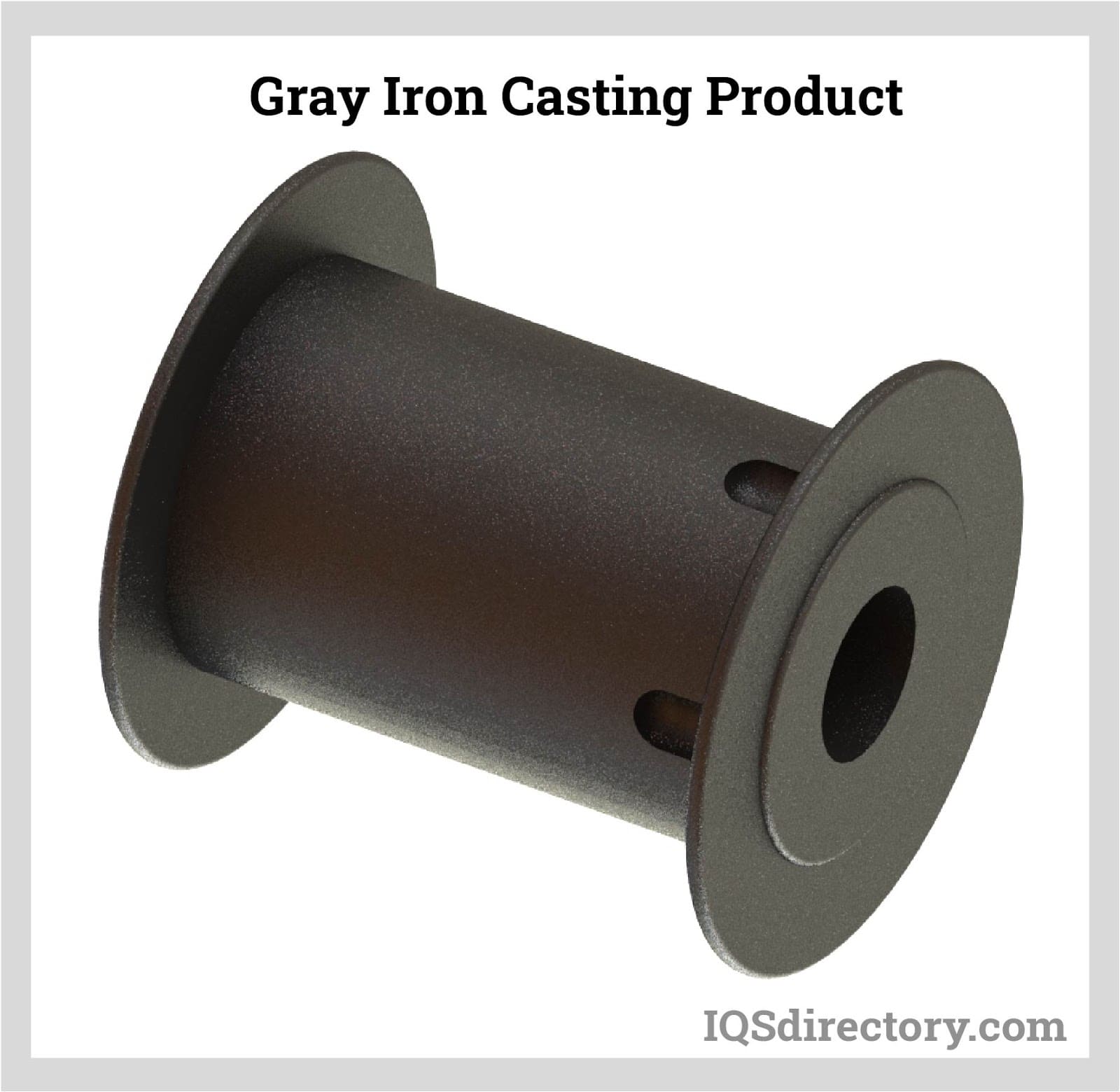
تمام این خواص مکانیکی توسط شکل و اندازه پولکهای گرافیت که در ریزساختار چدن خاکستری وجود دارند، کنترل میشوند.
ریختهگری چدن سفید
این نوع چدن دارای سطوح شکستهای است که به دلیل وجود رسوب کاربید آهن به نام سمنتیت، سفید رنگ هستند. کربن موجود در چدن سفید به جای گرافیت، به صورت فاز پایدار سمنتیت از مذاب خارج میشود. این امر با کاهش مقدار سیلیکون به عنوان عامل گرافیتزا و سرعت خنکسازی سریعتر حاصل میشود. پس از این رسوب، سمنتیت به صورت ذرات بزرگ تشکیل میشود.
در طول رسوب کاربید آهن، رسوب، کربن را از مذاب اولیه جذب میکند و بنابراین مخلوط را به سمت فازی که به یوتکتیک نزدیکتر است، حرکت میدهد. فاز باقی مانده، آهن را به آستنیت کربنی تبدیل میکند که پس از سرد شدن به مارتنزیت تبدیل میشود.
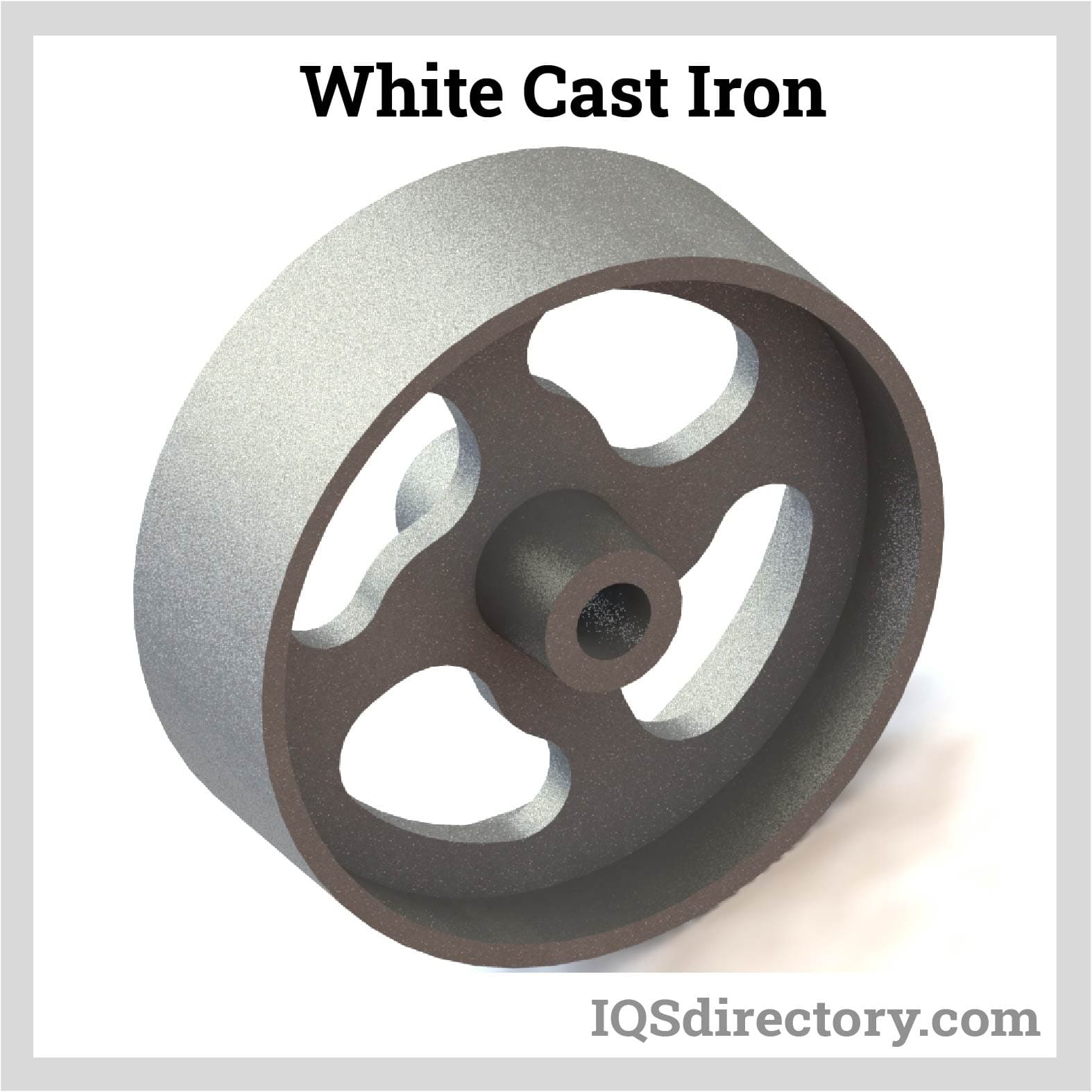
این کاربیدهای یوتکتیک موجود، برای ایجاد مزیت سخت شدن رسوبی بسیار بزرگ هستند. در برخی از فولادها، ممکن است رسوبات سمنتیت بسیار کوچکتری وجود داشته باشند که میتوانند با جلوگیری از حرکت نابجاییها در ماتریس فریت آهن خالص، تغییر شکل پلاستیک را تحمل کنند. آنها مزیتی دارند زیرا سختی توده چدن را صرفاً به دلیل سختی و کسر حجمی خود افزایش میدهند. این امر منجر به این میشود که سختی توده را بتوان با قانون مخلوطها تقریب زد.
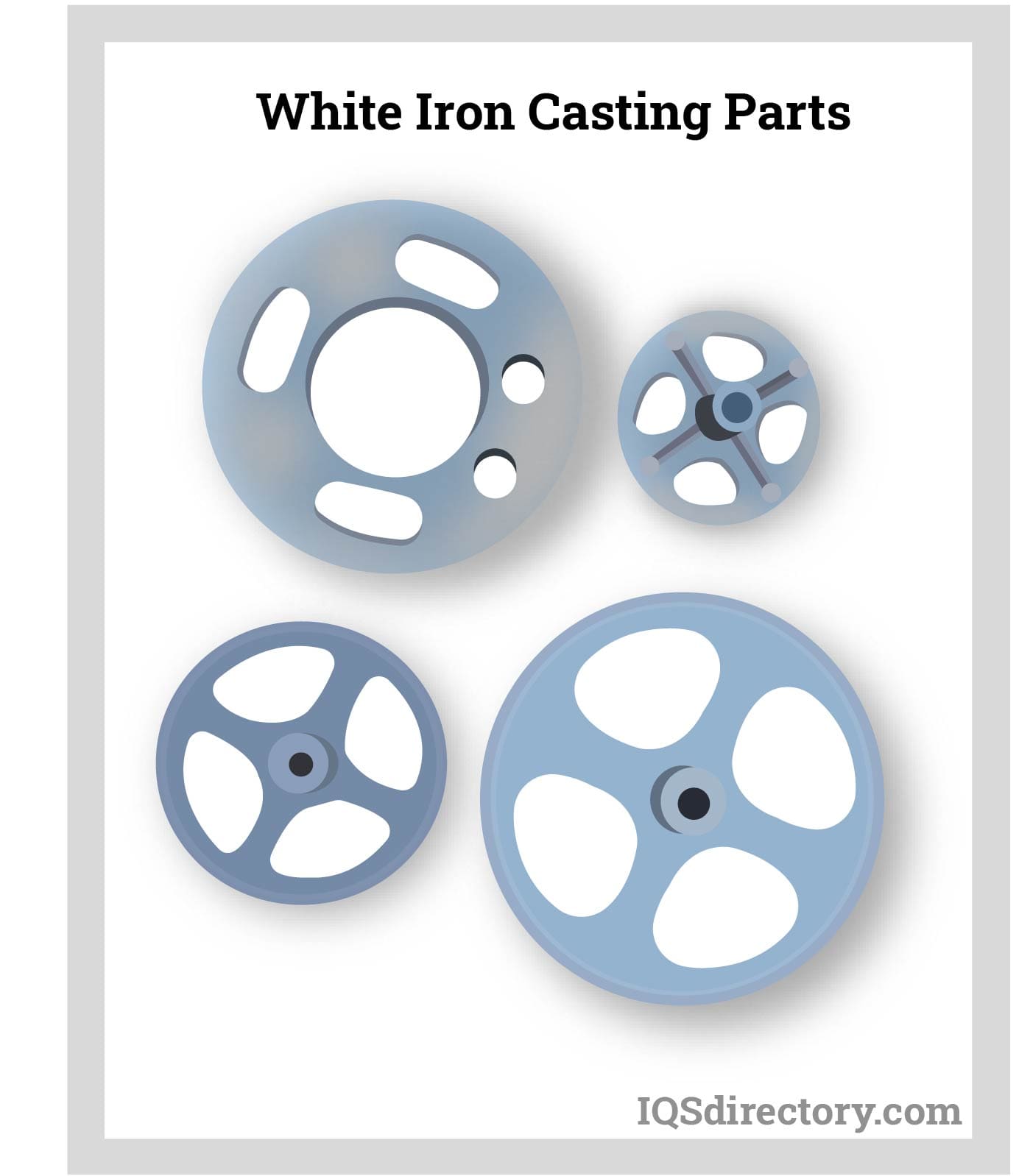
این سختی در هر صورت به قیمت از دست رفتن چقرمگی تمام میشود. چدن سفید را میتوان عموماً به عنوان سیمان طبقهبندی کرد، زیرا کاربید بخش بیشتری از این ماده را تشکیل میدهد. چدن سفید برای استفاده در اجزای سازهای بسیار شکننده است، اما به دلیل سختی خوب، مقاومت در برابر سایش و هزینه کم، میتوان از آن به عنوان سطح سایش پمپهای دوغاب استفاده کرد.
خنک کردن قطعات ریختهگری ضخیم با سرعتی که برای انجماد مذاب به شکل چدن سفید کافی باشد، دشوار است، با این حال میتوان از خنکسازی سریع برای انجماد مقدار زیادی چدن سفید استفاده کرد و پس از آن، باقیمانده آن با سرعت کمتری خنک میشود و در نتیجه هسته چدن خاکستری تشکیل میشود. این ریختهگری حاصل، ریختهگری سرد نامیده میشود و مزایای داشتن سطح سخت اما با داخلی سختتر را دارد.
آلیاژهای آهن سفید پر کروم این قابلیت را داشتند که ریختهگری عظیمی با وزن حدود 10 تن را به صورت ماسهای انجام دهند. این به این دلیل است که کروم سرعت خنک شدن مورد نیاز برای تولید کاربیدها را در ضخامتهای بیشتر ماده کاهش میدهد. کاربیدهایی با مقاومت سایشی عالی نیز توسط عناصر کروم تولید میشوند.
ریختهگری چدن چکشخوار
چدن چکشخوار به صورت ریختهگری چدن سفید تولید میشود، سپس به مدت دو یا یک روز در دمای حدود ۹۵۰ درجه سانتیگراد عملیات حرارتی میشود و سپس برای مدت مشابه سرد میشود.
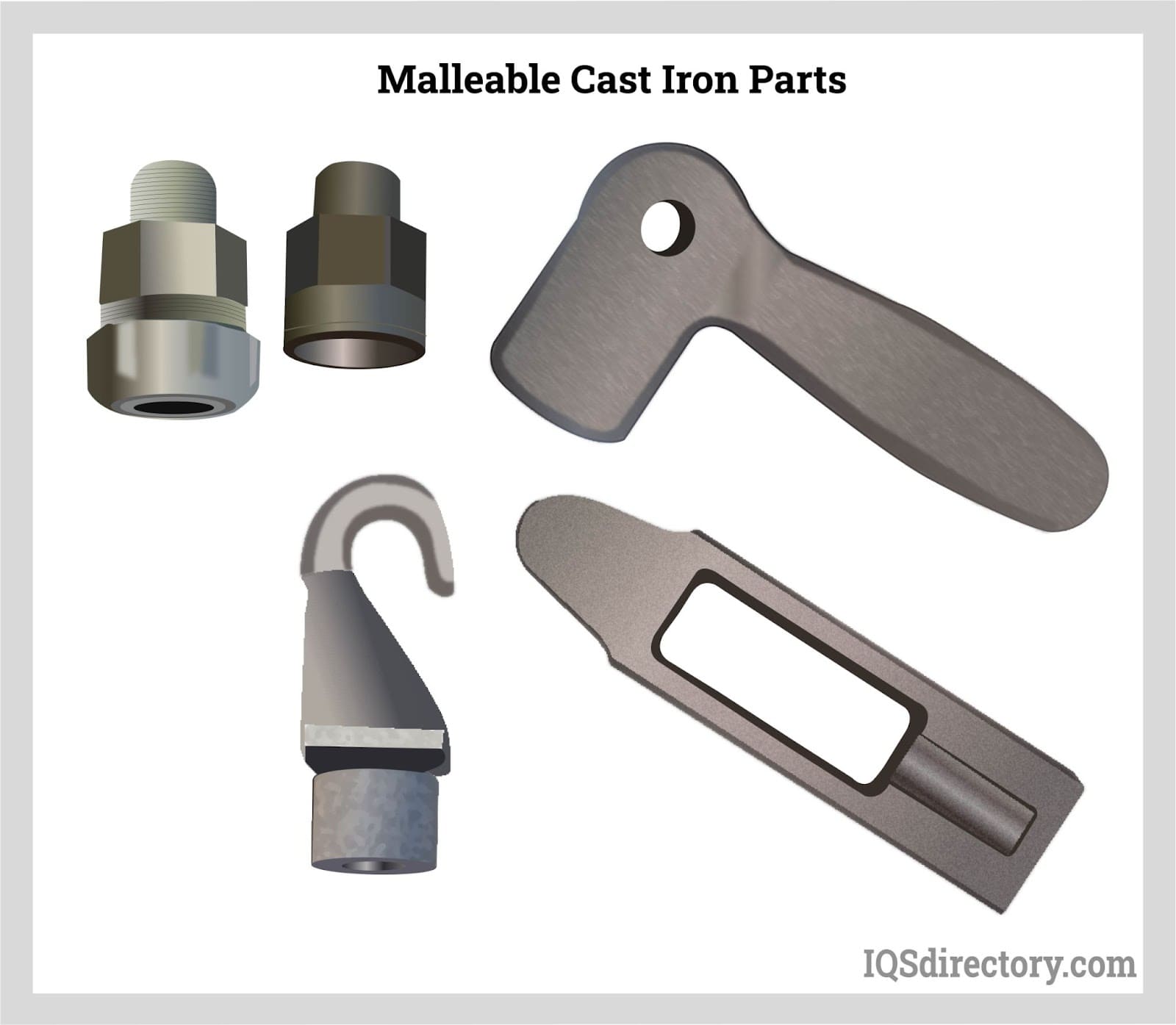
کربن موجود در کاربید آهن سپس به دلیل این فرآیند گرمایش و سرمایش به گرافیت و فریت به علاوه کربن تبدیل میشود. این فرآیند کم است، اما کشش سطحی را قادر میسازد تا گرافیت را به جای پوستهها به ذرات کروی تبدیل کند.
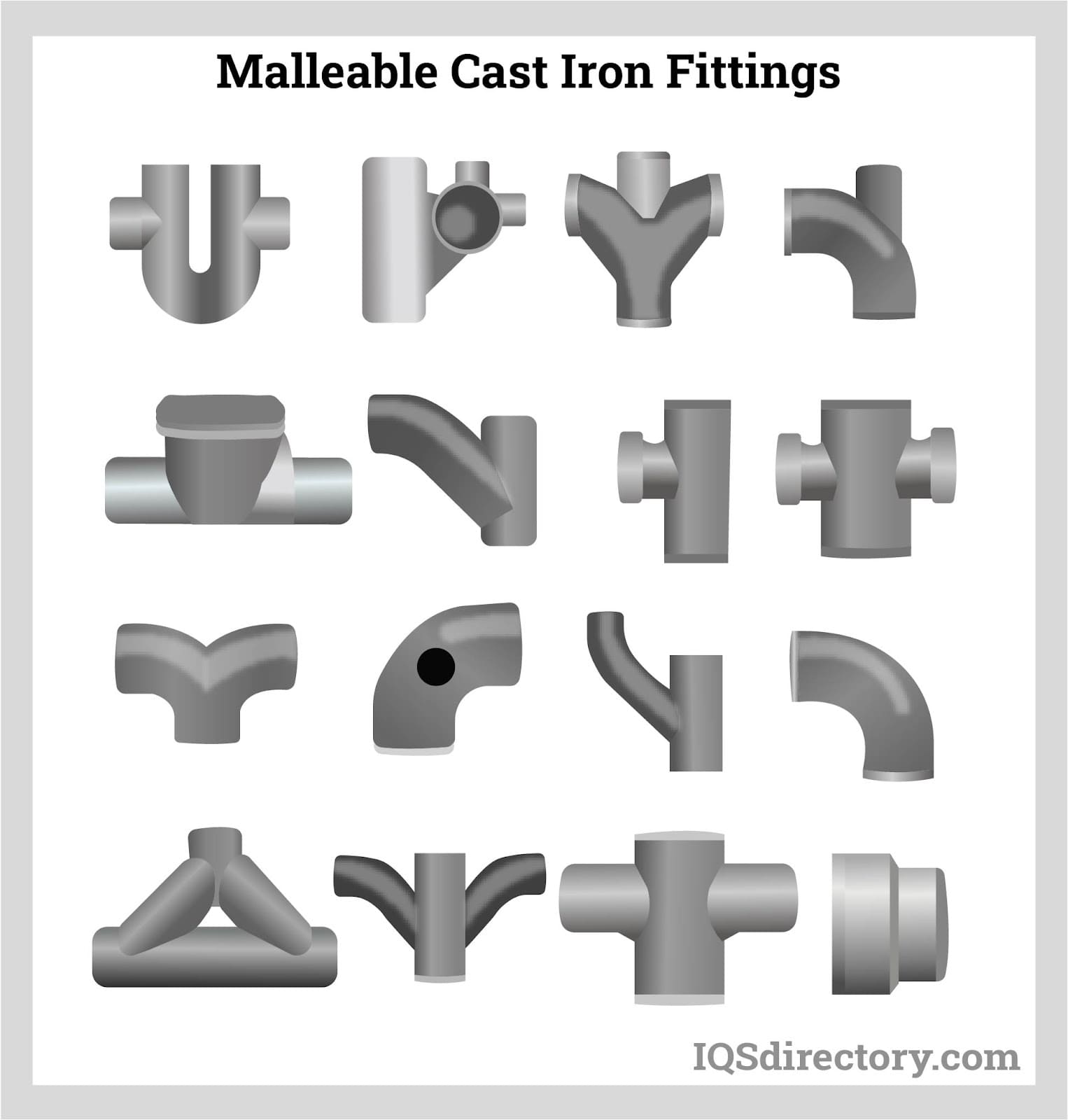
این کرهها به دلیل نسبت ابعاد پایین، نسبتاً کوتاه و از یکدیگر دورتر هستند. آنها همچنین دارای سطح مقطع پایینتری هستند که باعث انتشار ترک و فوتون میشود. برخلاف پولکها، آنها دارای مرزهای صافی هستند که در کاهش مشکلات تمرکز تنش که در چدن خاکستری یافت میشود، نقش دارند. در مجموع، خواص موجود در چدن چکشخوار بیشتر شبیه خواص فولاد است که ماهیت نرمی دارد.
ریختهگری چدن داکتیل
این چدن که گاهی اوقات به عنوان چدن گرهای نیز شناخته میشود، گرافیت خود را به شکل گرههای بسیار ریز دارد که گرافیت به شکل لایههایی متحدالمرکز است و در نتیجه گرهها را تشکیل میدهد. به همین دلیل، خواص ...چدن داکتیلفولاد اسفنجی است که هیچ اثر تمرکز تنشی ناشی از پولکهای گرافیت ندارد.
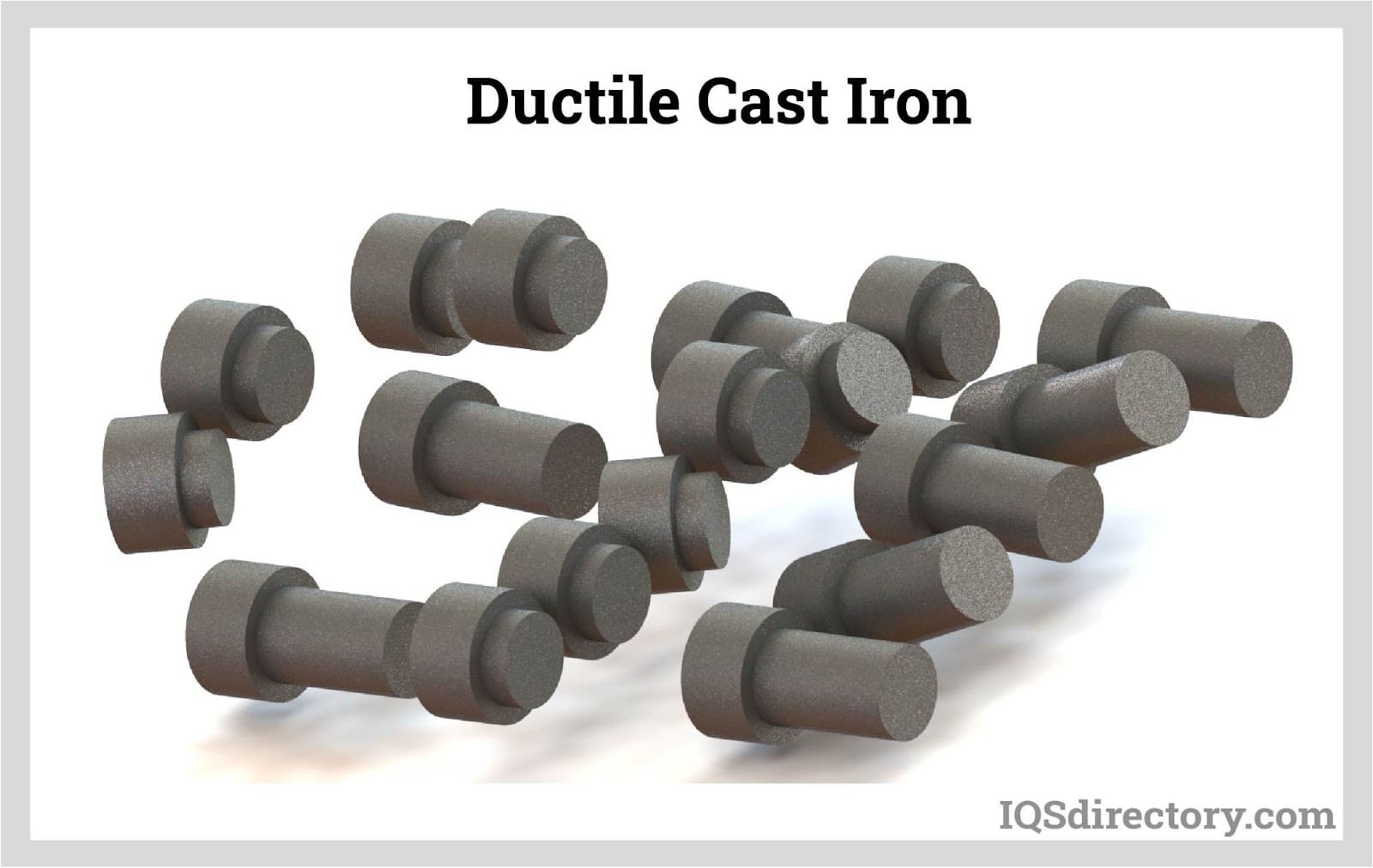
میزان غلظت کربن موجود حدود ۳ تا ۴ درصد و میزان غلظت سیلیکون حدود ۱.۸ تا ۲.۸ درصد است. مقادیر کم ۰.۰۲ تا ۰.۱ درصد منیزیم و تنها ۰.۰۲ تا ۰.۰۴ درصد سریم هنگام اضافه شدن به این آلیاژها، سرعت رشد رسوب گرافیت از طریق اتصال به لبههای خطوط گرافیت را کاهش میدهد.
به دلیل کنترل دقیق سایر عناصر و زمانبندی مناسب در طول فرآیند، کربن میتواند به صورت ذرات کروی در حین انجماد ماده جدا شود. ذرات حاصل شبیه چدن چکشخوار هستند، اما قطعات را میتوان با مقاطع بزرگتر ریختهگری کرد.
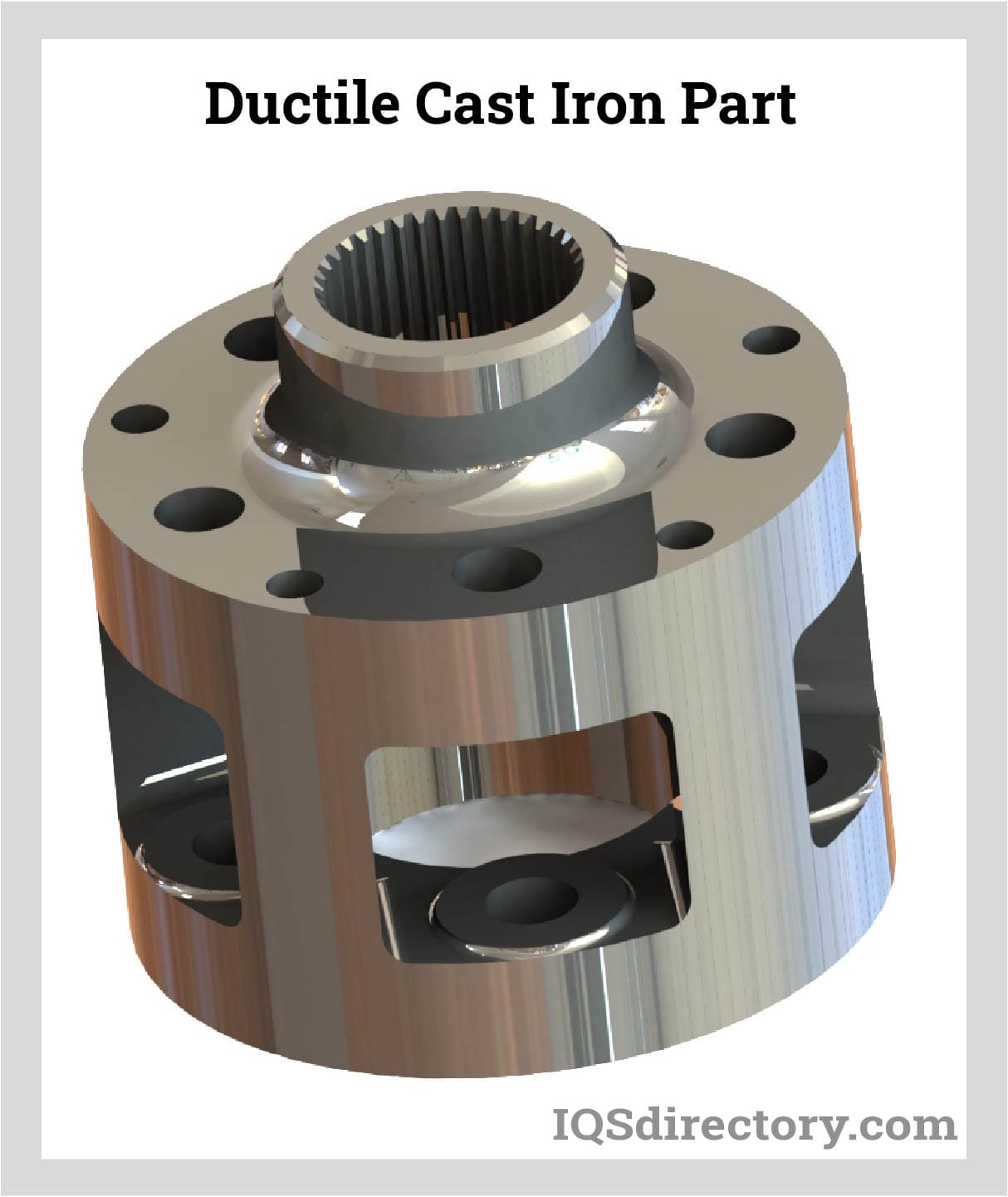
عناصر آلیاژی
خواص چدن تغییر میکند و عناصر آلیاژی یا آلیاژهای مختلفی به چدن اضافه میشوند. در کنار کربن، عنصر سیلیکون قرار دارد زیرا توانایی بیرون راندن کربن از محلول را دارد. درصد کمتر سیلیکون نمیتواند به طور کامل به این هدف دست یابد زیرا به کربن اجازه میدهد در محلول باقی بماند و در نتیجه کاربید آهن تشکیل میشود و همچنین چدن سفید تولید میشود.
درصد یا غلظت بیشتر سیلیکون میتواند کربن را از محلول خارج کرده و سپس گرافیت تشکیل دهد و همچنین چدن خاکستری تولید کند. سایر عوامل آلیاژی که ذکر نشدهاند عبارتند از منگنز، کروم، تیتانیوم و سپس وانادیوم. این مواد با سیلیکون مقابله میکنند، همچنین باعث حفظ کربن و در نتیجه تشکیل کاربیدها میشوند. نیکل و عنصر مس از این نظر مزیت دارند که استحکام و قابلیت ماشینکاری را افزایش میدهند، اما در این صورت قادر به تغییر مقدار کربن تشکیل شده نیستند.
کربنی که به شکل گرافیت است، منجر به نرمتر شدن آهن میشود، بنابراین اثر انقباض را کاهش میدهد، استحکام را پایین میآورد و چگالی موجود را کم میکند. گوگرد در حالت جامد عمدتاً یک آلاینده است و سولفید آهن تشکیل میدهد که از تشکیل گرافیت جلوگیری میکند و همچنین سختی را افزایش میدهد.
عیب گوگرد این است که چدن مذاب را چسبناک میکند و باعث ایجاد نقص میشود. برای جبران و از بین بردن اثرات گوگرد، منگنز به محلول اضافه میشود. این کار به این دلیل انجام میشود که وقتی این دو با هم ترکیب میشوند، به جای سولفید آهن، سولفید منگنز تشکیل میدهند. سولفید منگنز حاصل از مذاب سبکتر است و تمایل دارد از مذاب خارج شده و وارد سرباره شود.
مقدار تقریبی منگنز مورد نیاز برای خنثی کردن اثرات گوگرد، ۱.۷ واحد گوگرد و ۰.۳ درصد اضافی اضافه شده به آن است. افزودن بیش از این مقدار منگنز منجر به تشکیل کاربید منگنز میشود و این باعث افزایش سختی و سرد شدن میشود، به جز در چدن خاکستری که تا ۱ درصد منگنز میتواند استحکام و چگالی موجود را افزایش دهد. نیکل یکی از رایجترین عناصر آلیاژی است زیرا تمایل به تصفیه پرلیت و ساختار گرافیت دارد و در نتیجه چقرمگی را بهبود میبخشد و اختلاف سختی بین ضخامتهای مختلف را یکنواخت میکند.
کروم به مقدار کم اضافه میشود تا گرافیت آزاد را کاهش داده و باعث ایجاد حالت سردی شود. دلیل این امر این است که کروم یک تثبیتکننده کاربید قوی است و در برخی موارد میتواند همراه با نیکل عمل کند. برای کروم نیز میتوان مقدار کمی قلع به عنوان جایگزین اضافه کرد. مس در ملاقه یا کوره به میزان ۰.۵ تا ۲.۵ درصد اضافه میشود تا حالت سردی کاهش یابد، گرافیت تصفیه شود و سیالیت افزایش یابد. مولیبدن نیز میتواند به میزان ۰.۳ تا ۱ درصد اضافه شود تا حالت سردی افزایش یابد، گرافیت تصفیه شود و ساختار پرلیت اصلاح شود.
معمولاً این عنصر همراه با نیکل، مس و کروم برای تولید چدنهای با استحکام بالا اضافه میشود. عنصر تیتانیوم برای گاززدایی و اکسیژنزدایی و افزایش سیالیت اضافه میشود. نسبتهای 0.15 تا 0.5 درصد از عنصر وانادیوم به چدن اضافه میشود و به تثبیت سمنتیت، افزایش سختی و مقاومت در برابر سایش و اثرات گرما کمک میکند.
زیرکونیوم به تشکیل گرافیت کمک میکند و به نسبت حدود ۰.۱ درصد تا ۰.۳ درصد اضافه میشود. این عنصر همچنین به اکسیژنزدایی و افزایش سیالیت کمک میکند. در مذابهای چدن چکشخوار، برای افزایش میزان سیلیکون قابل افزودن، بیسموت در مقیاس ۰.۰۰۲ درصد تا ۰.۰۱ درصد ریخته میشود. در چدن سفید، عنصر بور اضافه میشود که به تولید آهن چکشخوار کمک میکند و اثر درشتکنندگی عنصر بیسموت را کاهش میدهد.