Types de pièces moulées en fonte
Types de pièces moulées en fonte
Ce chapitre traitera des différents types de pièces moulées en fonte.
Moulage en fonte grise
La fonte grise se caractérise par sa microstructure graphique, capable de provoquer des fractures et de lui donner un aspect gris. C'est le type de fonte le plus couramment utilisé, et également le matériau de moulage le plus utilisé en raison de son poids. La majorité des fontes grises présentent une décomposition chimique de 2,5 à 4 % de carbone, de 1 à 3 % de silicone, le reste étant composé de fer.
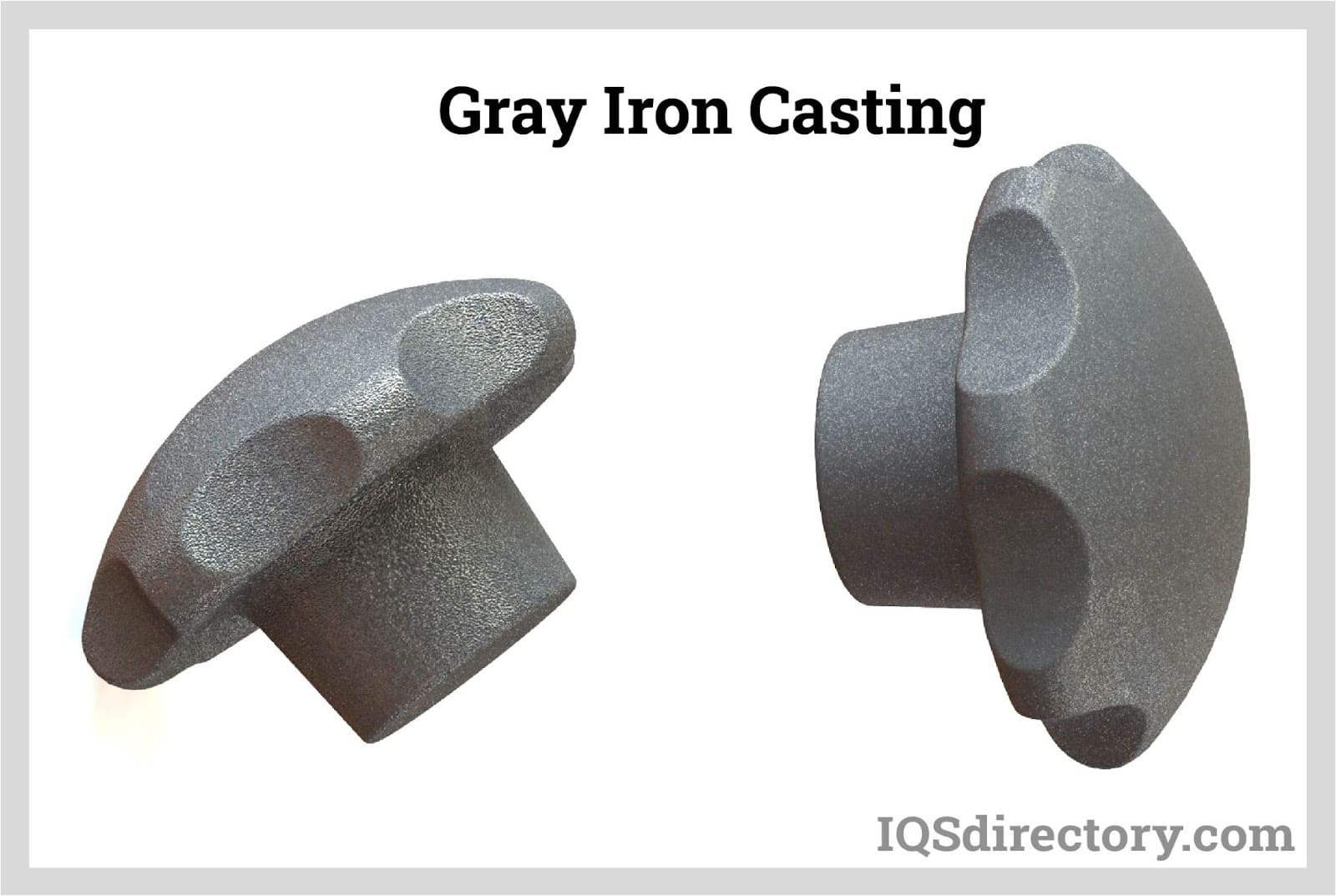
Ce type de fonte présente une résistance à la traction et aux chocs inférieure à celle de l'acier. Sa résistance à la compression est comparable à celle de l'acier à faible et moyenne teneur en carbone.
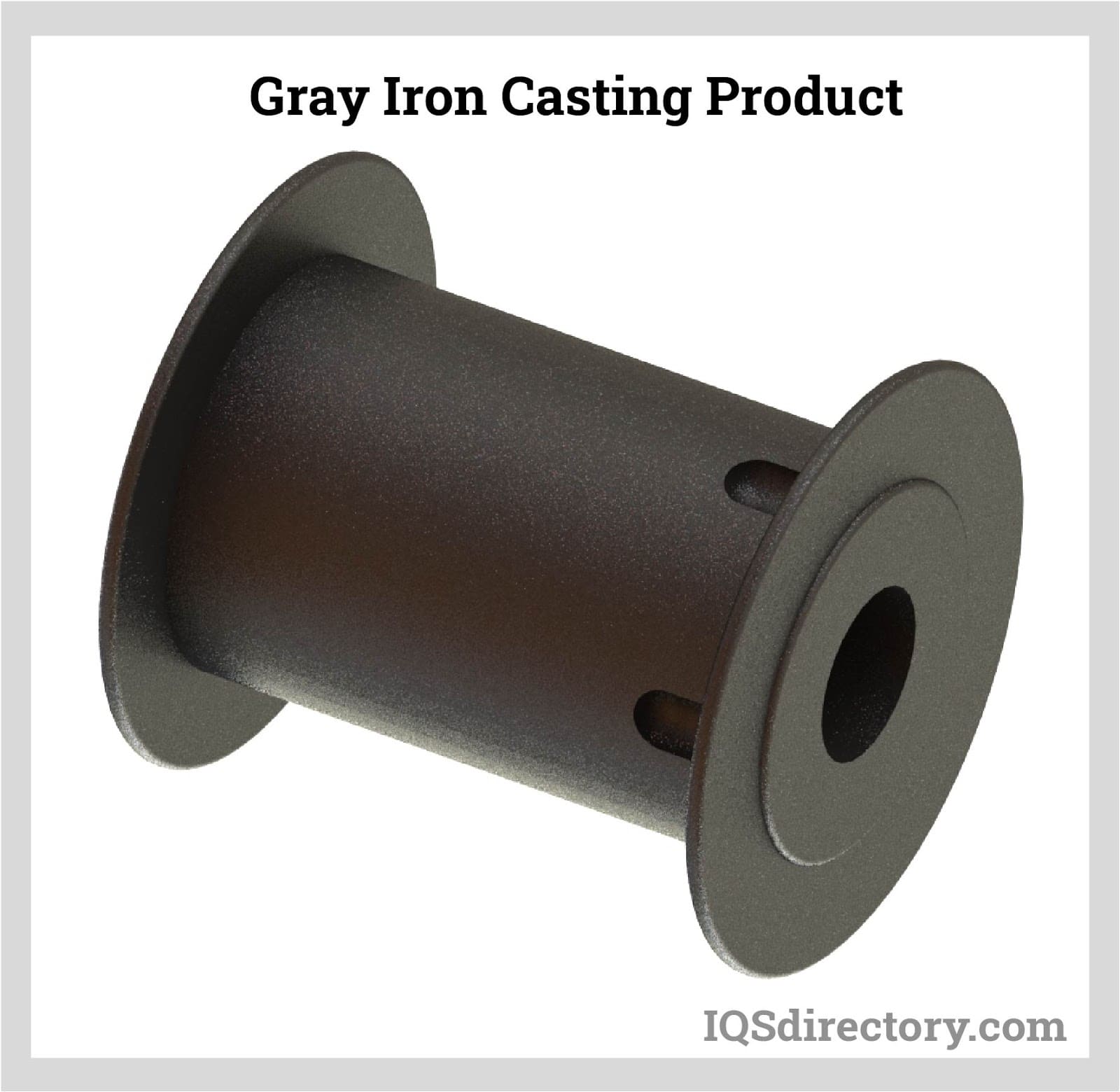
Toutes ces propriétés mécaniques sont contrôlées par la forme des paillettes de graphite et la taille des paillettes de graphite, présentes dans la microstructure de la fonte grise.
Moulage en fonte blanche
Ce type de fonte présente des surfaces fracturées, blanches en raison de la présence d'un précipité de carbure de fer appelé cémentite. Le carbone contenu dans la fonte blanche précipite hors du bain sous forme de cémentite en phase stable plutôt que sous forme de graphite. Ce résultat est obtenu grâce à une teneur en silicium plus faible comme agent graphitisant et à une vitesse de refroidissement plus rapide. Après cette précipitation, la cémentite se forme sous forme de grosses particules.
Lors de la précipitation du carbure de fer, le précipité extrait le carbone du bain d'origine, rapprochant ainsi le mélange de l'eutectique. La phase restante consiste à abaisser le fer en austénite de carbone, laquelle se transforme en martensite une fois refroidie.
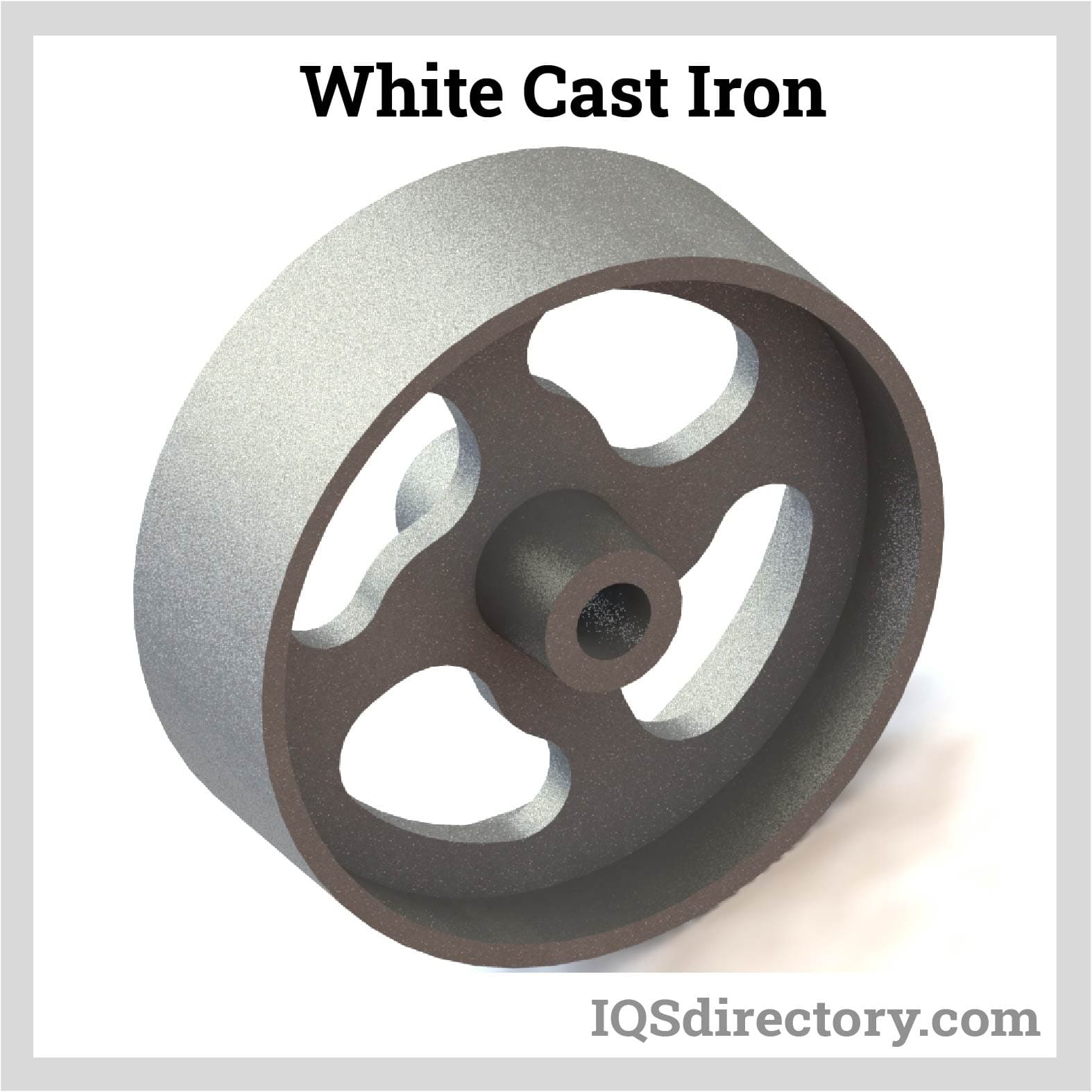
Ces carbures eutectiques contenus sont trop gros pour bénéficier du durcissement par précipitation. Certains aciers peuvent contenir des précipités de cémentite beaucoup plus petits, susceptibles de favoriser la déformation plastique en empêchant le mouvement des dislocations à travers la matrice de ferrite pure. Leur avantage réside dans le fait qu'ils augmentent la dureté volumique de la fonte, simplement grâce à leur dureté et à leur fraction volumique. Il est ainsi possible d'estimer la dureté volumique par une règle de mélange.
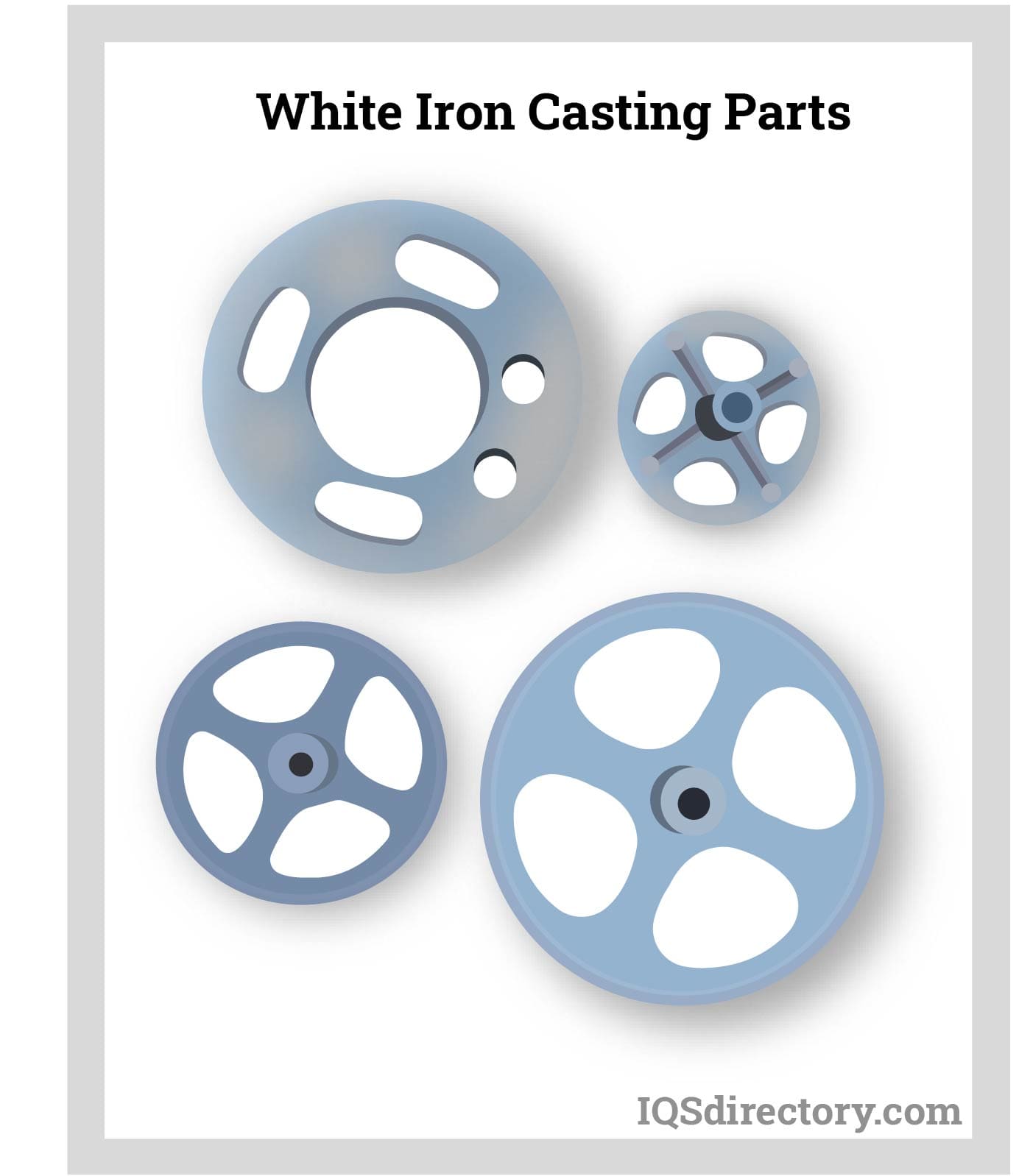
Cette dureté se fait de toute façon au détriment de la ténacité. La fonte blanche peut généralement être classée comme un ciment, car le carbure y constitue une part importante. Trop fragile pour être utilisée dans les composants structurels, la fonte blanche peut néanmoins servir de surface d'usure pour les pompes à boues, grâce à sa bonne dureté, sa résistance à l'abrasion et son faible coût.
Il est difficile de refroidir des pièces moulées épaisses à une vitesse suffisante pour solidifier la fonte en fonte blanche. Cependant, un refroidissement rapide permet de solidifier une grande quantité de fonte blanche, puis de refroidir le reste à une vitesse plus lente, formant ainsi un noyau de fonte grise. Cette pièce moulée est appelée « pièce refroidie » et présente l'avantage d'une surface dure et d'un intérieur plus résistant.
Les alliages de fonte blanche à haute teneur en chrome permettent de couler au sable des turbines d'environ 10 tonnes. Cela s'explique par le fait que le chrome réduit la vitesse de refroidissement nécessaire à la production de carbures malgré des épaisseurs de matériau plus importantes. Des carbures présentant une excellente résistance à l'abrasion sont également produits à partir d'éléments en chrome.
Moulage en fonte malléable
La fonte malléable commence sous forme de pièce moulée en fonte blanche, puis est traitée thermiquement à des températures d'environ 950 °C pendant deux ou un jour, puis elle est refroidie pendant la même période de temps.
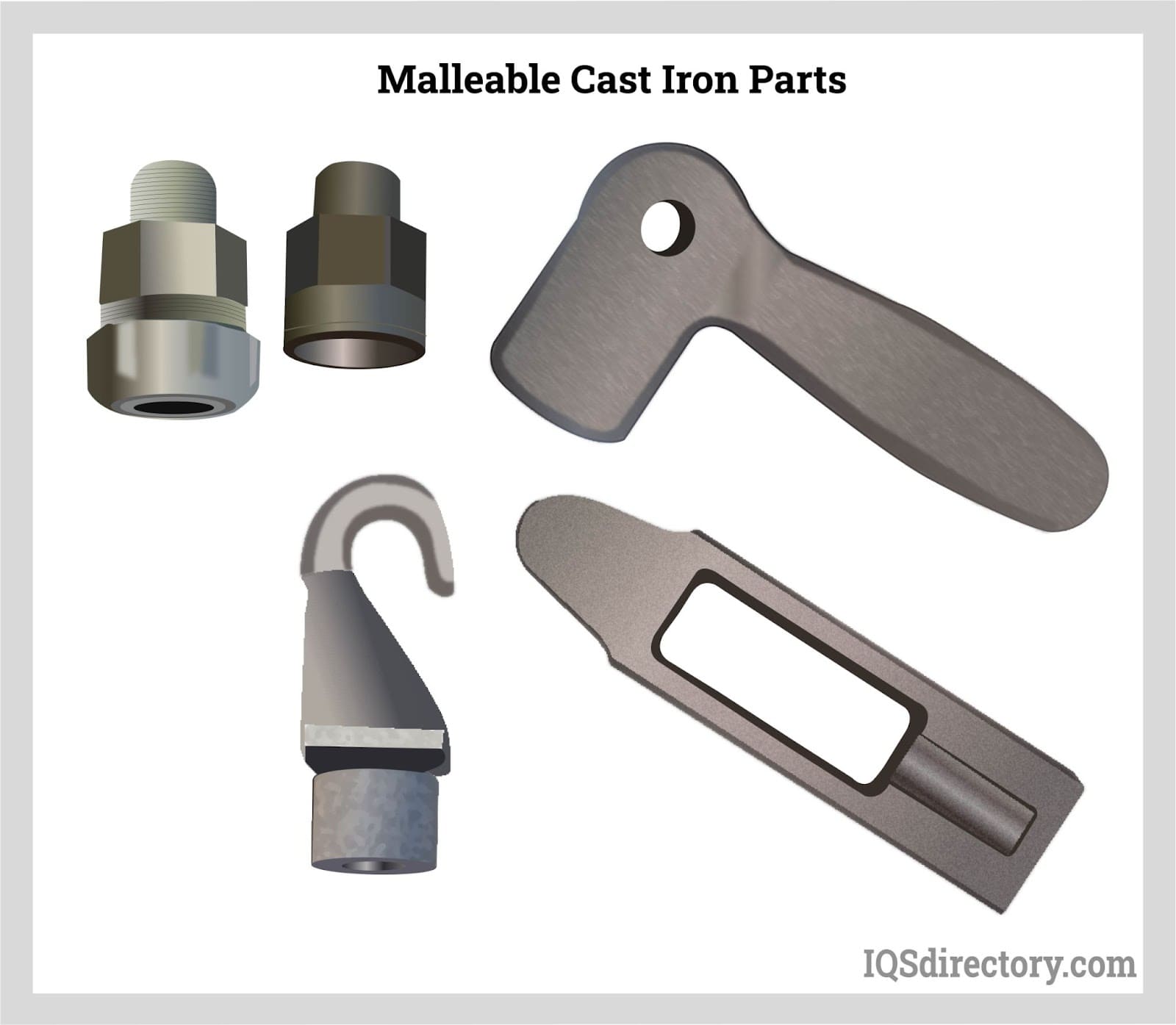
Le carbone du carbure de fer se transforme ensuite en graphite et en ferrite plus carbone grâce à ce processus de chauffage et de refroidissement. Ce processus est lent, mais il permet à la tension superficielle de transformer le graphite en particules sphéroïdales plutôt qu'en paillettes.
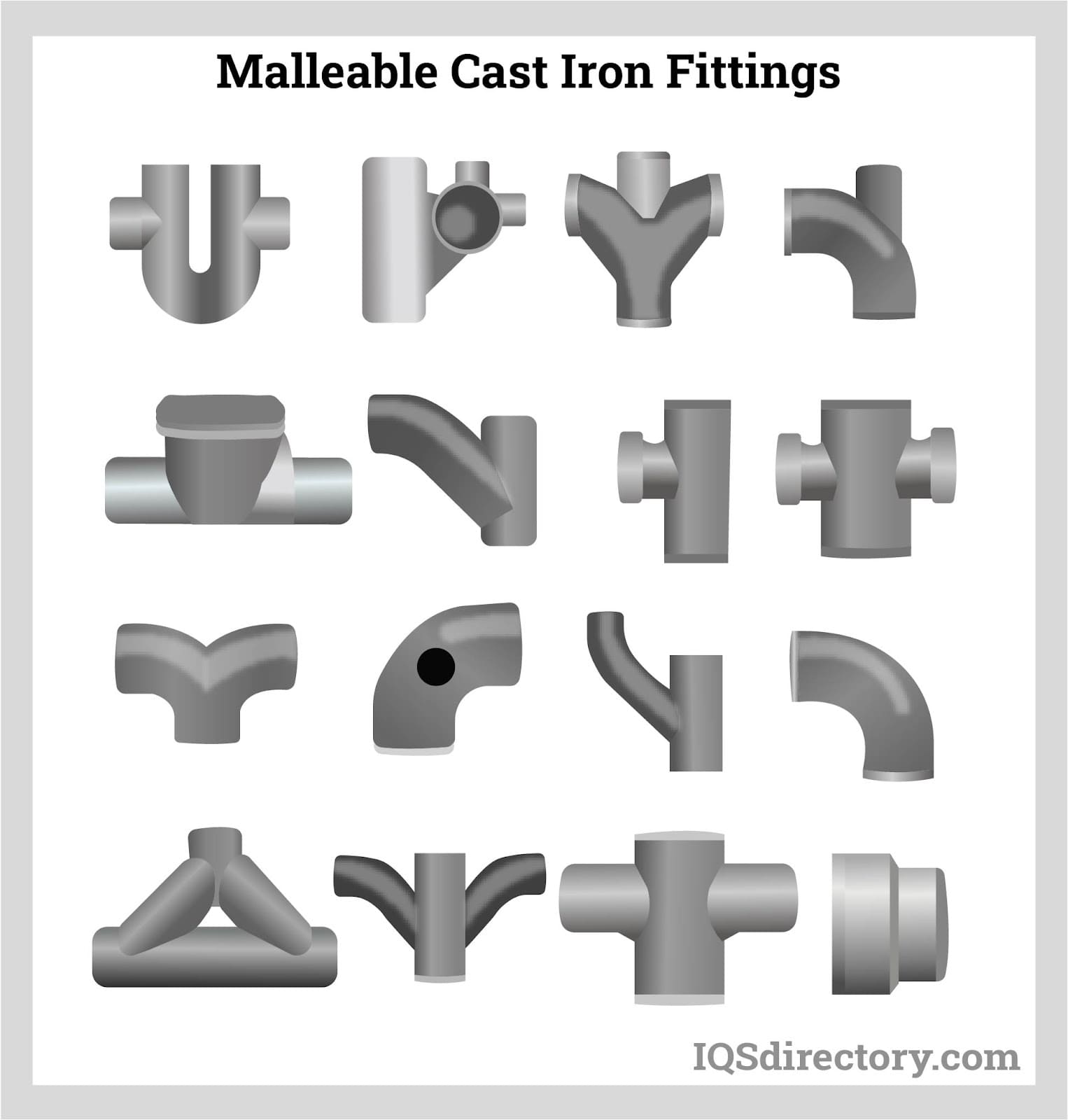
Les sphéroïdes sont relativement courts et plus éloignés les uns des autres en raison de leur faible rapport d'aspect. Ils présentent également une section transversale plus faible, une fissure propagatrice et un photon. Contrairement aux paillettes, leurs limites sont émoussées, ce qui contribue à atténuer les problèmes de concentration de contraintes propres à la fonte grise. Globalement, les propriétés de la fonte malléable sont plus proches de celles de l'acier, qui est doux par nature.
Moulage en fonte ductile
Parfois appelée fonte nodulaire, cette fonte possède un graphite sous forme de minuscules nodules, disposés en couches concentriques formant ainsi les nodules. De ce fait, ses propriétésfonte ductilesont celles d'un acier spongieux qui ne présente pas d'effets de concentration de contraintes produits par les paillettes du graphite.
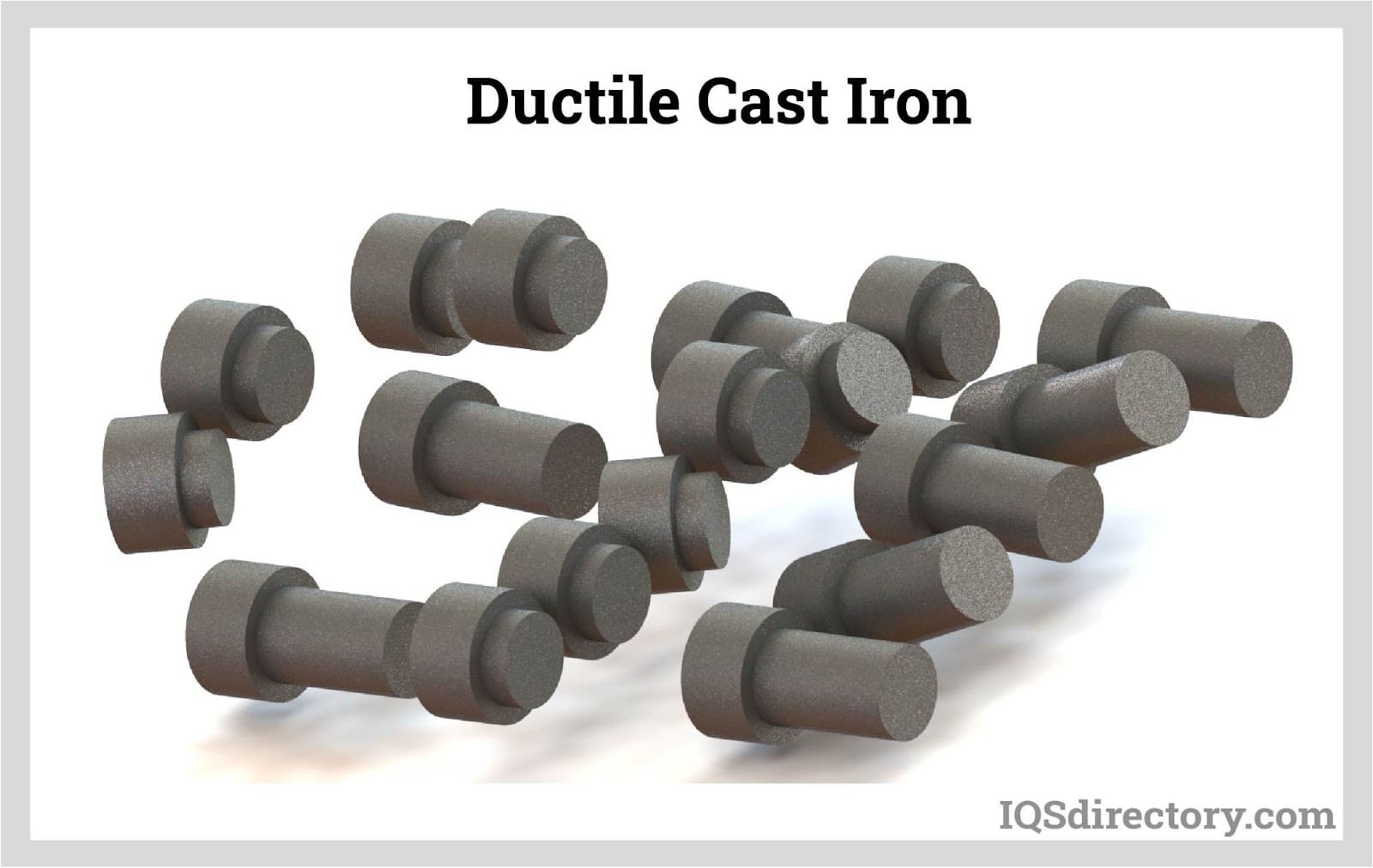
La concentration en carbone est d'environ 3 à 4 %, et celle en silicium d'environ 1,8 à 2,8 %. De faibles quantités de 0,02 à 0,1 % de magnésium et seulement 0,02 à 0,04 % de cérium ajoutées à ces alliages ralentissent la vitesse de précipitation du graphite par liaison aux bords des pistes de graphite.
Le carbone peut se séparer en particules sphéroïdales lors de la solidification du matériau, grâce à un contrôle rigoureux des autres éléments et à un timing précis du processus. Les particules obtenues sont similaires à celles de la fonte malléable, mais des pièces plus grandes peuvent être moulées.
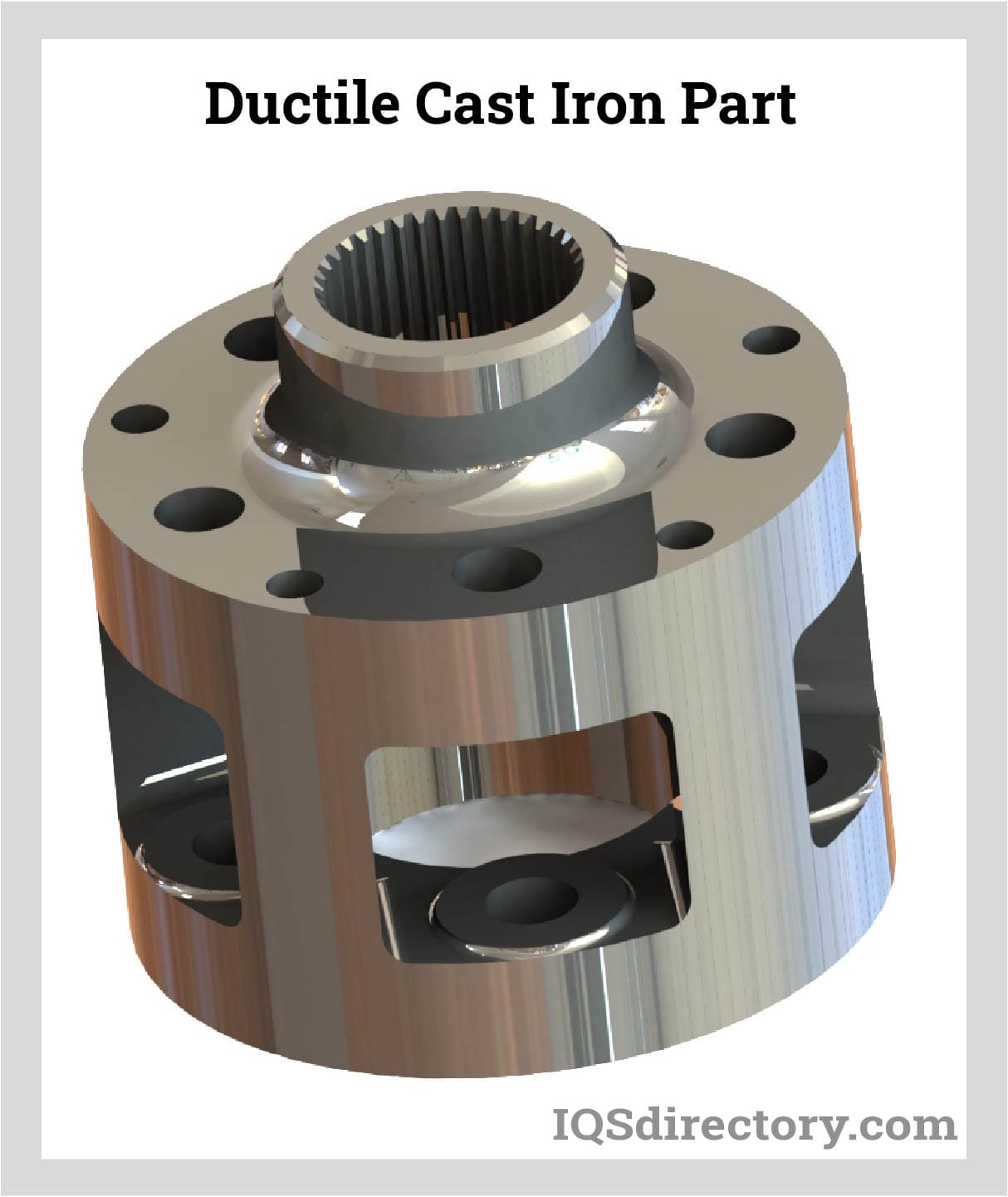
Éléments d'alliage
Les propriétés de la fonte sont modifiées par l'ajout de divers éléments d'alliage. Le silicium, qui s'apparente au carbone, a la capacité d'extraire le carbone de la solution. Un faible pourcentage de silicium ne permet pas d'atteindre cet objectif, car il maintient le carbone en solution, formant ainsi du carbure de fer et produisant de la fonte blanche.
Un pourcentage ou une concentration plus élevée de silicium permet d'extraire le carbone de la solution, formant ainsi du graphite et produisant de la fonte grise. D'autres agents d'alliage, non mentionnés, incluent le manganèse, le chrome, le titane et le vanadium. Ces derniers neutralisent le silicium et favorisent la rétention du carbone, et donc la formation de carbures. Le nickel et le cuivre présentent l'avantage d'augmenter la résistance et l'usinabilité, mais ils ne modifient pas la quantité de carbone formée.
Le carbone sous forme de graphite produit un fer plus tendre, réduisant ainsi l'effet de retrait, la résistance et la densité. Le soufre, principalement présent dans le graphite, est un contaminant et forme du sulfure de fer, ce qui empêche la formation de graphite et augmente la dureté.
L'inconvénient du soufre est qu'il rend la fonte en fusion visqueuse, ce qui entraîne des défauts. Pour compenser et éliminer les effets du soufre, on ajoute du manganèse à la solution. En effet, leur combinaison forme du sulfure de manganèse au lieu du sulfure de fer. Le sulfure de manganèse ainsi obtenu est plus léger que le métal fondu et a tendance à flotter hors du métal fondu et à se retrouver dans le laitier.
La quantité approximative de manganèse nécessaire pour neutraliser les effets du soufre est de 1,7 unité de teneur en soufre, plus 0,3 % ajouté. L'ajout d'une quantité supérieure entraîne la formation de carbure de manganèse, ce qui augmente la dureté et le refroidissement, sauf pour la fonte grise, où jusqu'à 1 % de manganèse peut augmenter la résistance et la densité. Le nickel est l'un des éléments d'alliage les plus courants, car il a tendance à affiner la perlite et la structure du graphite, améliorant ainsi la ténacité et égalisant les différences de dureté entre les épaisseurs de section.
Le chrome est ajouté en petites quantités pour réduire le graphite libre et produire un refroidissement. En effet, le chrome est un puissant stabilisateur de carbure et, dans certains cas, il peut fonctionner en association avec le nickel. Pour le chrome également, une petite quantité d'étain peut être ajoutée. Du cuivre est ajouté en poche ou au four à raison de 0,5 à 2,5 % pour réduire le refroidissement, affiner le graphite et augmenter la fluidité. Du molybdène peut également être ajouté à raison de 0,3 à 1 % pour augmenter le refroidissement, affiner le graphite et affiner la structure de la perlite.
On l'ajoute généralement en association avec le nickel, le cuivre et le chrome pour produire des fontes à haute résistance. Le titane, élément chimique, agit comme dégazeur et désoxydant, et améliore la fluidité. Des proportions de 0,15 % à 0,5 % de vanadium sont ajoutées à la fonte pour stabiliser la cémentite, augmenter la dureté et résister à l'usure et aux effets thermiques.
Le zirconium contribue à la formation du graphite et est ajouté dans des proportions d'environ 0,1 à 0,3 %. Cet élément contribue également à la désoxydation et à la fluidité. Dans les fontes malléables, pour augmenter la quantité de silicium pouvant être ajoutée, on verse du bismuth à raison de 0,002 à 0,01 %. Dans la fonte blanche, on ajoute du bore, ce qui favorise la production de fer malléable et réduit l'effet grossier du bismuth.